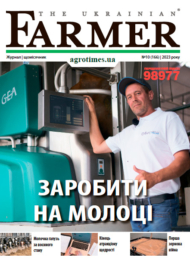
Ще на етапі створення технічного завдання і проєктування елеватора часто трапляються помилки у виборі обладнання, а саме з його продуктивністю і енергоспоживанням
Елеватор без помилок
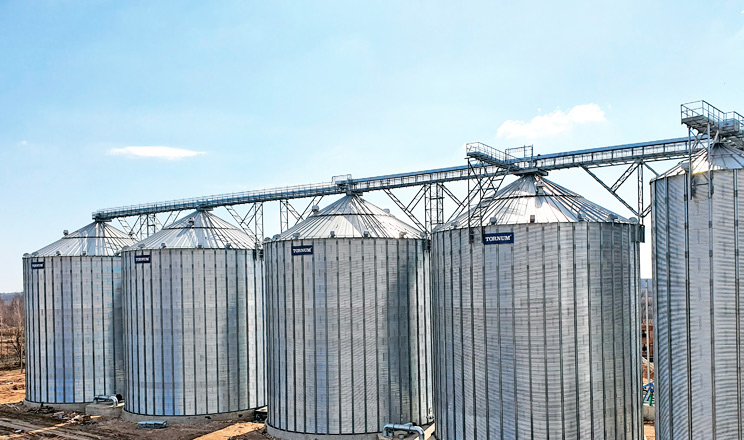
Ще на етапі створення технічного завдання і проєктування елеватора часто трапляються помилки у виборі обладнання, а саме з його продуктивністю і енергоспоживанням.
Спочатку обираємо сушарку
Накопичений досвід із проєктування елеваторів дає підставу зробити певний аналіз помилок, яких припускаються замовники. Їх є багато, але основні — у виборі невідповідного обладнання. Чому так трапляється?
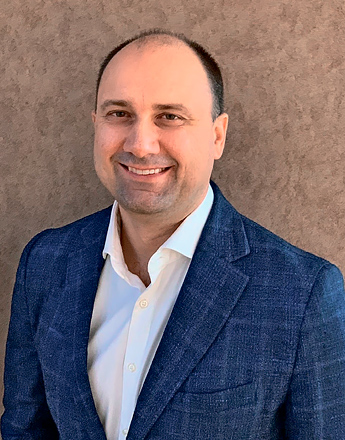
Насамперед неправильно визначають цільове призначення елеватора. Є велика різниця між фермерським і лінійним або маршрутним елеватором. І річ не в принципі роботи, а в обсягах перевалювання і завданнях, які ставлять перед підприємством. Відповідно, інструменти, якими ці завдання будуть виконувати, також будуть різними.
Після визначення типу елеватора створюється його технологічна схема. Тут потрібно зв’язати все технологічне обладнання — сушарку, завальні ями, силоси, хопери тимчасового зберігання, відвантаження — і створити повний комплекс маршрутів, якими переміщатимуть зерно.
Третій етап власне передбачає вибір усього технологічного обладнання. Виходячи з потреб у продуктивності передусім підбирають сушарку, бо саме від характеристик сушарки обирають усе інше.
На ринку є багато виробників, конструкцій і цін. Проте головне — не помилитись із продуктивністю. Наприклад, господарство планує приймати на добу максимум 500 т кукурудзи. Відповідно, є потреба сушити саме таку кількість, щоб під час збирання не було затримування саме через елеватор. Однак це не означає, що сушарка продуктивністю 500 т/добу зможе впоратись із завданням. Нерідко виробники сушарок зазначають продуктивність сушіння кукурудзи з температурою сушильного агента 130 °С. Проте для зменшення пошкоджень зазвичай температуру сушильного агента встановлюють на рівні 110–115 °С, що автоматично знижує продуктивність сушіння на 15%. Отже, замість 500 т продуктивності на добу матимемо 425 т.
Можна також додати, що паспортну продуктивність сушарки вказують для певних погодних умов — температури повітря й відносної вологості. На практиці ж доводиться сушити у значно гірших умовах, і продуктивність стає ще меншою: замість 425 т у кращому випадку отримуємо 400 т/добу замість 500 т. Окрім зниження продуктивності маємо перевитрати на обладнання, бо обирали з розрахунку на 500 т/добу. Звідси слід зробити висновок: від усіх виробників сушарок вимагати надавати продуктивність сушіння з різною температурою сушильного агента (100–110– 115–120–130 градусів).
Аби переконатись, що сушарка зможе видавати потрібну продуктивність, слід звернути увагу на інший показник: кількість повітря, що проходить крізь зернову шахту. Іншими словами потрібно дізнатись продуктивність вентиляторів (м³/год). Існує залежність — 1 м³ повітря за час проходження шару зерна може ввібрати в середньому 19 г води. Тому, якщо з 500 т потрібно видалити 10% вологи (з 24 до 14%), це 50 т води (50 000 кг). Ділимо 50 000 на 0,019 й отримуємо 2 631 000 м³ повітря на добу або близько 110 000 м./год. Також слід зауважити на такий момент. Часто продуктивність вентиляторів указують паспортну, без опору зерна. А коли доводиться продувати зерно, опір становить близько 200 Па. Відповідно, реальна продуктивність вентиляторів може бути на 30% меншою.
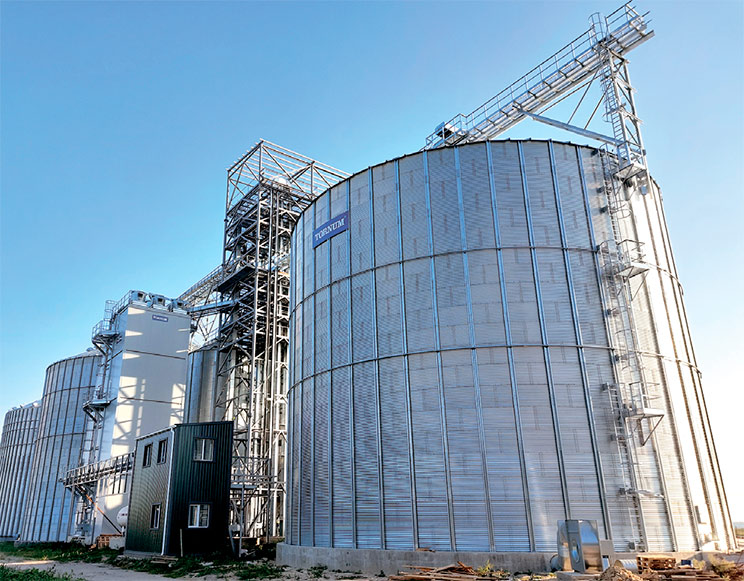
Підбиваємо підсумки: обираючи сушарку, слід дізнатись у виробника продуктивність за різних температур і який об’єм повітря видають вентилятори з урахуванням опору зерна. Звичайно слід поцікавитись потужністю пальника — це також може бути «вузьким місцем» сушарки, яке обмежує продуктивність. Тому компанія TORNUM зазвичай пропонує клієнтам сушарки з номінальною продуктивністю на 25–30% вищою від максимальних вимог, щоб гарантувати потрібну продуктивність без втрат якості. Хтось скаже, що це забагато, але тут є одна особливість, яка може бути важливою. Коли сушарка працює на межі своїх можливостей, мінімальне погіршення умов роботи (збільшується вологість зерна, погіршуються погодні умови) стане причиною різкого зниження продуктивності. Якщо ж запас є, погіршення умов призведе тільки до незначного зменшення продуктивності, яке суттєво не вплине на роботу підприємства.
Від керування залежить точність сушіння й втрати палива
Рівень автоматизації впливає як на продуктивність роботи сушарки, так і на паливну економічність. Часто замовники тільки питають, чи працює сушарка в автоматичному режимі, і коли отримують позитивну відповідь, їм цього достатньо. Але тут також є розбіжності, від яких залежить результат.
Автоматика більшості виробників орієнтується на температуру повітря холодної зони шахти. Відомо, що після відбору вологи температура має становити близько +47 °С. Якщо температура вища, це означає, що зерно пересушується, якщо нижча — зерно виходить із сушарки недосушеним. Система керування постійно відстежує температуру вихідного повітря і в разі відхилень від еталонного значення (+47 °С) корегує швидкість вивантаження. Але ця система має високу інертність, бо по всій шахті датчики не встановиш — вони досить дорогі. Тому корегування режимів роботи зазвичай відбуваються не моментально, а із запізненням, і похибка вологості зерна на виході може становити до 3%. Щоб уникнути таких коливань, слід завантажувати в сушарку зерно однакової вологості. Якщо вологість зерна суттєво коливається, режим роботи змінюється, але, враховуючи інертність, не завжди це відбувається вдало. Нерідко трапляється так, що вхідна вологість змінюється досить часто, і зерно, що треба сушити інтенсивніше, сушиться, навпаки, ще менше. У такому разі оператор вимикає автоматику й працює в ручному режимі.
Тільки три відомих виробники сушарок у світі пішли іншим шляхом, і один із них — TORNUM.
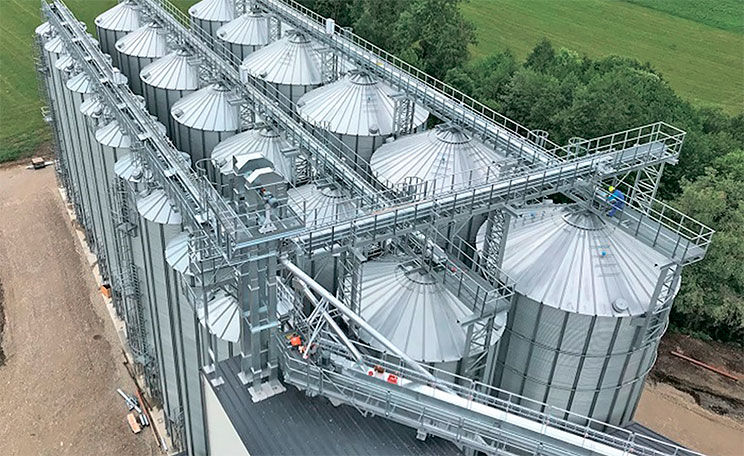
Вони встановили датчики вологості безпосередньо у шахту і контролюють процес сушіння саме за показником вологості, а не температури. Це значно зменшує коливання вологості зерна на виході (до 1%). Наприклад, у компанії TORNUM градуювання похибки становить 0,3%, 0,5 і 0,7%. Це досягається завдяки точності роботи датчика вологості й програмного забезпечення, яке одночасно аналізує безліч чинників, що впливають на сушіння. До того ж на простих моделях установлюють один датчик вологості, а на складніших — два: на вході на виході. Інші виробники також почали встановлювати датчики вологості на свої сушарки, але вони не «прив’язані» до системи автоматичного керування. З них інформація виводиться на екран, щоб оператор міг бачити фактичну вологість. Однак автоматика не бере до уваги цю інформацію, алгоритм керується тільки температурою повітря на виході.
Увага на джерело енергії
Важливо ще на самому початку визначитись із джерелом тепла, бо сушарка має бути адаптована до роботи з різними типами пальників або теплогенераторів. Найкраще рішення з боку якості роботи сушарки це, звичайно — газ (природний або скраплений), потім — теплогенератори на біопаливі з теплообмінником і в останню чергу — теплогенератори без теплообмінника.
Газові пальники забезпечують стабільні показники температури теплового агента за будь-яких умов роботи — у цьому їхня головна цінність, плюс вони надійні та прості в експлуатації. Теплогенератори складніші в експлуатації, вимагають ретельного контролю та частого обслуговування. Також показники температури теплового агента мають вищі відхилення, що негативно відбивається як на продуктивності сушарки, так і на безпеці — варто звернути увагу що автоматизація працює зі значними відхиленнями й втрачає свою доцільність. Виняток — випадки, коли сушарку постачають із теплообмінниками типу рідина-повітря або пар-повітря, встановленими на заводі. У такому разі гарантується стабільна робота сушарки від водогрійних або парових котлів, що також працюють на біопаливі
Економимо на прийманні
Приймання варто розраховувати так, щоб можна було прийняти розрахункову кількість тонн не протягом доби, а за 10–11 год, як це зазвичай буває на практиці. Відповідно до цього слід розраховувати розмір завальних ям, хоперів тимчасового зберігання і продуктивність транспортерів і норій. Щодо хоперів тут є ще один момент, на який слід зауважувати. Задля якіснішого і більш економічного сушіння зерно повинно мати практично однакову вологість. Якщо розбіжність вологості у різних партіях сягає 3–4% і більше, слід виконати таку операцію, як вирівнювання вологості. У хопері тимчасового зберігання вмикають аерацію, що має на меті не сушіння, а саме вирівнювання вологості. Протягом 10–12 год вдається знизити розбіжність вологості до 2%, і таке зерно можна сушити у стабільному режимі з мінімальними витратами палива. Однак для нормальної роботи елеватора доведеться побудувати два хопери місткістю 50–60% добового обсягу приймання. Якщо на добу планується приймати до 500 т, хопери мають уміщувати по 300 т кожен. З одного зерно сушитиметься в сушарці, а другий тим часом наповнюватиметься.
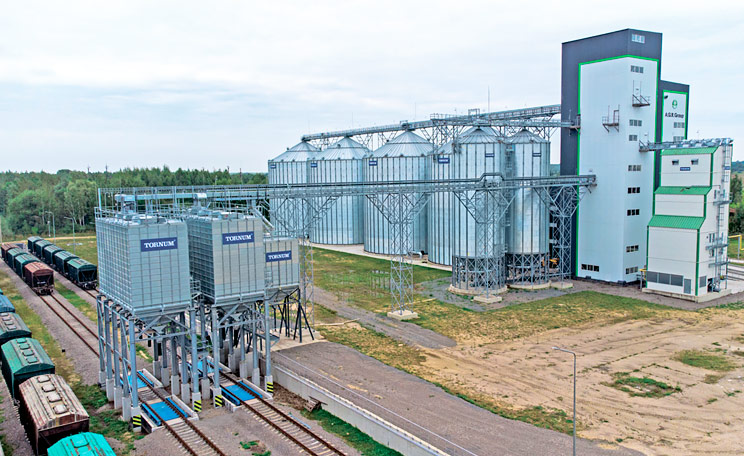
Транспортне обладнання із запасом
Розрахунок продуктивності конвеєрів і норій має відповідати максимальним режимам роботи приймання і сушіння з невеликим запасом. Запас потрібен для надійності, але варто пам’ятати, що додаткова потужність мотор-редукторів і більша міцність ланцюгів означає більше споживання електроенергії, більшу вагу і додаткові витрати на металоконструкції. Тут переплата означатиме задарма витрачені гроші. Однак слід брати до уваги, що продуктивність транспортного обладнання завжди вказують для сухого зерна. Коли ж доводиться працювати з вологим, продуктивність транспортера знижується на 3% з кожним зайвим відсотком вологості. Окрім того, варто звертати увагу на сервіс-фактор мотор-редуктора та клас енергоефективності, геометрію модульної зірочки й міцність ланцюга та його швидкість руху. Якщо всі ці компоненти якісні, можна розраховувати, що транспортер видасть заявлену продуктивність. Неабияку увагу слід звернути на перелік і тип швидкозношуваних частин, що в майбутньому через певну кількість годин напрацювання потрібно замінювати на нові.
З норіями ситуація дещо інша. Тут треба дивитись на частоту встановлення ковшів, їх форму, а також швидкість руху стрічки та можливість транспортування олійних культур. Крім того, для легких і важких культур ефективність наповнення може відрізнятись залежно від того, чи ківш черпає зерно або завантажується насипом.
Особливості зберігання і відвантаження
Силоси також можуть впливати на продуктивність елеватора. Залежно від розміру силосів може змінюватись час на переміщення зерна — усе залежить від призначення елеватора і культур, з якими він працює. Потужність аераційних вентиляторів має залежати від того, як довго планується зберігати зерно. Якщо воно лежить усього кілька місяців, аерація потрібна мінімальна. Це саме стосується і термометрії, бо впродовж тривалого зберігання дуже важливо тримати температуру всередині під постійним контролем. Тут потрібно виводити усі дані на один екран, щоб оператор міг одразу бачити стан зерна в кожному силосі. За короткострокового зберігання вистачить термометрії, що показує температуру зерна з виводом інформації на переносний ручний пристрій.
На відвантаженні продуктивність також може бути підвищена завдяки кільком рішенням. Перше — встановлення кількох місткостей на одну точку відвантаження. Наприклад, компанія TORNUM на автовідвантаження пропонує встановлювати три квадратних місткості. Це дає змогу більш рівномірно розподіляти зерно по кузову і пришвидшувати завантаження. При цьому обсяг місткості має бути не меншим за подвійний обсяг вантажу для автотранспорту. У цьому разі під час завантаження автомобіля не відбувається повне звільнення місткостей, і наступний автомобіль може почати завантажуватись без затримання — транспортна система постійно поповнює місткість.
Друге рішення, що набуває поширення по нових і робочих елеваторах, це тензодатчики на бункерах відвантаження. З їх допомогою оператор може точно завантажити автомобіль без додаткового корегування ваги. Це зменшує час перебування автотранспорту на елеваторі й гарантує уникнення його перевантаження.
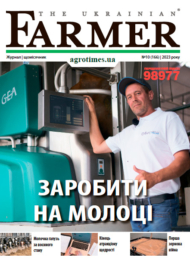