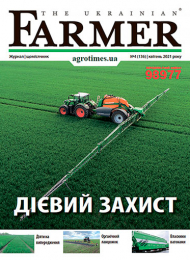
Принципи вибору обладнання для сушіння та зберігання зерна у СТОВ «Агрофірма „Маяк”»
Надійність не має ціни
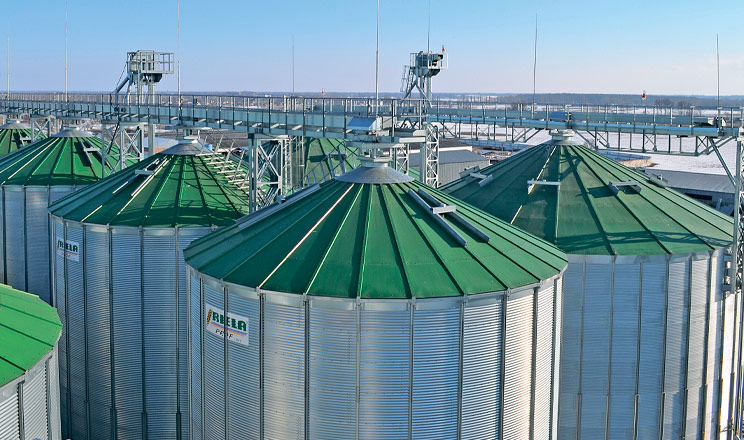
Як перший позитивний досвід може стати основою тривалої співпраці
Господарство «Агрофірма „Маяк”» відоме не лише рослинництвом, а й насамперед молочним і м’ясним тваринництвом. Забезпечення кормами є одним із головних завдань підприємства, тому не дивно, що до власного кормовиробництва було поступово збудовано досить потужний елеватор, який складається з двох сушарок і великої кількості силосів різної потужності загальною місткістю 55 тис. тонн по пшениці. Директор підприємства Олексій Васильченко розповів про створення елеватора, а також про принципи й підходи до вибору обладнання.
Усе розпочалось із будівництва сушарки відомого німецького виробника RIELA. На той момент зерно зберігали в старих підлогових складах, тому вирішили починати з незначних інвестицій. Сушарку «прив’язали» до очисної машини українського виробництва (для вторинного очищення, первинне виконували сепаратором RIELA Prof-seed) і маленької завальної ями, навколо якої зерно лежало під навісом. Не було навіть хоперів для тимчасового зберігання. Певний час підприємство працювало в такому режимі, бо вільних коштів для швидкого будівництва бракувало, а кредитів брати принципово не хотіли.
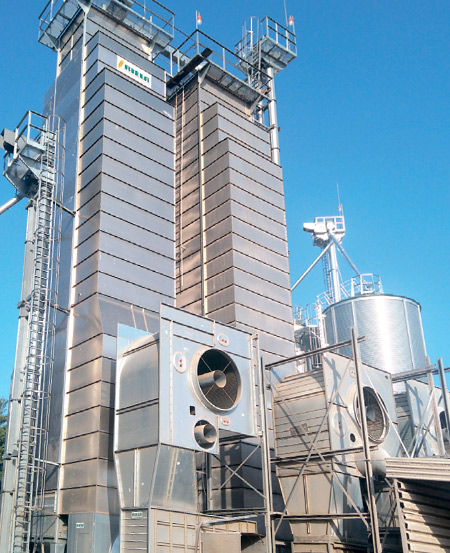
За цей час краще «познайомились» із роботою сушарки RIELA. Вона сподобалася системою вентиляції й вивантаження, якісним монтажем, невеликим енергоспоживанням. Побачивши, що сушарка забезпечує якісне сушіння і для неї є хороший сервіс, під час вибору обладнання для подальшого будівництва вирішили й далі співпрацювати з ТзОВ «РІЛЯ Україна» — офіційним представником торгової марки RIELA. Один з американських виробників пропонував меншу ціну, але це не стало головним аргументом для власника.
Насамперед збудували п’ять силосів по 2 тис. тонн кожний. Може здатися, що таке рішення є помилковим: чим менший силос, тим дорожче обходиться тонна зберігання, і, навпаки, великий силос дорожче коштує, але зберігання там дешевше. Річ у тому, що «Агрофірма „Маяк”» зосереджена на вирощуванні свиней, ВРХ і виробництві молока. Відповідно, є потреба в одночасному зберіганні різних культур: ячменю, пшениці, сої, кукурудзи для виробництва кормів. Тому таке рішення — будівництво п’яти силосів — було виправданим, бо вони забезпечують основні потреби підприємства.
Ще перед початком будівництва, коли тільки збиралися замовляти сушарку, було розроблено стратегію розвитку підприємства на найближчі роки. Ця стратегія передбачала будівництво елеватора в кілька етапів — це залежало від динаміки розвитку самого підприємства. Такий підхід виявився дуже корисним: коли до сушарки почали добудовувати силоси, було зрозумілим, що, де і як має бути. В результаті збудували елеватор на 55 тис. тонн у чотири етапи, а поруч поставили комбікормовий завод. І головне — нічого не доводилося перебудовувати, всі об’єкти комплексу технологічно з’єдналися без жодних проблем.
Збільшуючи потужності
Щоб дещо здешевити будівництво, під перші силоси копали глибокі котловани й робили фундаменти. Справа виявилася непростою, але зекономити вдалося. Потім компанія «РІЛЯ Україна» виконала монтаж силосів і транспортного обладнання. Усе зробили вчасно, елеватор розпочав роботу без затримок. Коли почало надходити зерно, стало зрозумілим, що це зовсім інший рівень роботи.
Звісно, не обійшлося без труднощів перших років. Виникла проблема пошкодження зерна — особливо це стосувалося кукурудзи. Добре, що ці відходи використовували для приготування комбікормів, і жодних збитків підприємство не зазнало. Однак після ретельного аналізу і вивчення досвіду інших підприємств знайшли причину, яка полягала в неправильній технології роботи із зерном. У результаті кукурудзу перестали пересушувати (тепер лишають 15% вологості), і проблема практично зникла. Після завантаження силоса нижній шар одразу «відкачують» — саме у цьому шарі максимальна кількість травмованого зерна, яке пошкоджується в результаті падіння на тверду підлогу. Таким чином, у силосі лишається тільки чисте зерно.
Одночасно сталися зміни на ринку, які змусили підприємство трансформувати власну сівозміну. Відмовились від вирощування великих площ ярого й озимого ячменю, бо з цією культурою не вдавалося досягати стабільних результатів. Вирішили замість неї збільшити площі під соєю, пшеницею й кукурудзою. Необхідну для виробництва комбікорму кількість ячменю підприємство почало купувати в інших виробників.
Зросли обсяги виробництва зерна, і наявних потужностей для зберігання вже стало замало. Постало питання будівництва другої черги. Цього разу вирішили не гратись із риттям глибоких котлованів, і під силоси зробили пальове поле. Знову звели п’ять місткостей по 2 тис. тонн, і постачальником обладнання й підрядником знову стала ТзОВ «РІЛЯ Україна». З’явилась можливість працювати не лише з власним зерном, а ще й надавати послуги стороннім підприємствам.
Нині важко передбачити, які напрями приноситимуть найбільший прибуток, тому інвестиції повинні передбачати можливість диверсифікації й зменшення ризиків. Елеватор будується на багато десятиліть, і треба бути готовим швидко змінювати напрям роботи. На сьогодні зручність у великій кількості силосів полягає в можливості окремо зберігати зерно з кожного поля. По завершенню жнив можна ретельніше проаналізувати якість зерна й сформувати партії з однаковими характеристиками.
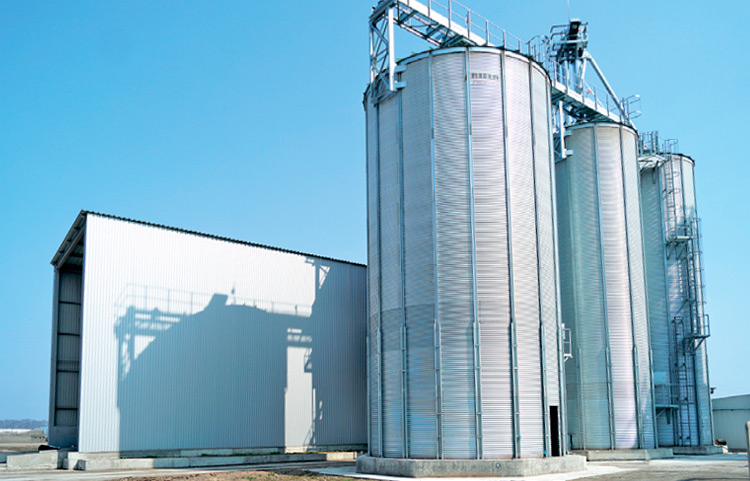
Паралельно з будівництвом другої черги тривали роботи з відновлення системи штучного зрошення на площі в 1500 га. Відповідно, зменшилась залежність від погодних умов, урожайність стала більш прогнозованою й зросла в кількісному виразі. Підлогового сховища для кукурудзи стало замало, знову з’явилась потреба в додаткових силосах. Коли з переміщенням і зберіганням на вчились працювати, побачили, що вузьким місцем є первинне очищення. Знову продовжилось будівництво: звели два хопери RIELA для тимчасового зберігання по 250 т кожний, завальну яму, придбали потужну очисну машину RIELA Prof-Seed 2006 B і змонтували сушарку RIELA тип GDT 300/24/3.
Коли персонал елеватора спокійно спить вдома?
Після завершення монтажу другої сушарки помітили, що зовні вона нічим не відрізняється від першої, яка відпрацювала майже 20 років. Силоси теж стійко витримали вплив часу і погоди. Міцні дахи силосів RIELA вкрито полімерним матеріалом SOLANO, який інші виробники не застосовують. Полімер завтовшки 0,2 мм накладається на оцинковану сталь і захищає від впливу ультрафіолетових променів і агресивних природних опадів. Він належить до 3-го класу захисту від корозії, згідно з нормою DIN 55928. Це забезпечило повну збереженість конструкцій, незважаючи на 10-річну експлуатацію. Для порівняння керівник приводить приклад сусіднього підприємства, у якому дахи на силосах не мають нормального захисту і вже почали активно кородувати.
Для первинного очищення встановили машину ЛУЧ-150 одеського виробника «ОЛИС». Два хопери дозволяють сортувати зерно різної вологості й з різною кількістю смітної домішки. Це дає змогу легко налаштовувати сушарку й працювати без постійних змін режимів. Після встановлення хоперів персонал тепер спокійно спить удома — зникла потреба підгортати зерно до завальної ями. Дещо пізніше добудували два силоси по 5 тис. тонн, а на завершальному етапі звели хопер на 500 т, один силос на 2 тис. тонн, два силоси на 5 тис. тонн, і один на 7500 т. У результаті обсяги одночасного зберігання сягнули 55 тис. тонн. Фінальним штрихом стало впровадження системи автоматизації. Цю роботу також виконала компанія ТзОВ «РІЛЯ Україна», і відтепер цим процесом у наземно-очисному комплексі може управляти одна людина.
ГОВОРЯТЬ ЕКСПЕРТИ
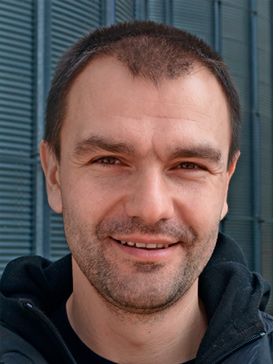
Олексій Васильченко, директор СТОВ «Агрофірма „Маяк”»
— Багато хто економить на конструкціях, що підтримують верхні транспортери. До того ж норії й транспортери зроблені з цинкування, а все, на чому воно тримається, роблять зі звичайного чорного металу. Власники тішать себе думкою, що вони будуть щороку ці конструкції фарбувати. Однак реалії дещо відрізняються від мрій: після введення в експлуатацію елеватора ніхто нічого не фарбує, аж доки іржу не почнуть змивати опади на оцинковані дахи силосів. Птахи додають свій «вклад» до створення агресивного середовища на даху, і той успішно кородує. Тому я вважаю, що неприпустимо економити на матеріалі конструкцій. По-перше, це може призвести до ржавіння поверхонь, по-друге, фарбувати ці конструкції в перші роки ніхто не стане. А потім буде пізно. До того ж фарбування на висоті складне й небезпечне. Тож навіщо вносити елементи ризику в роботу високотехнологічного підприємства?
Також не можу зрозуміти тих, хто будує елеватор, що коштує мільйони доларів, і економить на засобах автоматизації. Засувки з електроприводом коштують 7 тис. гривень, а звичайні — всього тисячу. Якщо порахувати всі такі деталі, набігає різниця в 50 і більше тисяч. Однак якщо врахувати, що кожного разу доведеться відправляти до цієї засувки людину, вийде зовсім не та економія. Для цього знадобиться додатковий персонал на зміні, якому потрібно платити гроші. Тож за рік елементи автоматизації окупляться тільки на скороченні потрібної кількості персоналу. Зараз весна, і на елеваторі практично немає людей. Оператор може одночасно чистити, сушити й відвантажувати зерно, і для цього достатньо розуміти, що як працює, а також елементарно дотримуватися технологій.
Хочу звернути увагу тих, хто будує перший свій елеватор: важливо обирати такого виробника обладнання, який не поведеться на забаганки замовника. Буває, що замовник через власне незнання категорично відмовляється від певних обов’язкових речей. З часом приходить розуміння, що те, про що говорив виробник обладнання, є обов’язковим, і через її відсутність тепер страждає якийсь етап виробництва або неможливе будівництво наступної черги.
У процесі перемовин із представниками ТзОВ «РІЛЯ Україна» такого не виникало. Ми донесли своє бачення стратегії розвитку підприємства, а вони запропонували конкретний проєкт з урахуванням власного досвіду будівництва схожих об’єктів в Україні та світі. Тому перед початком будівництва елеватора в умовах дефіциту коштів потрібно відразу розуміти, яким має бути об’єкт після завершення останнього етапу будівництва через 5 або 10 років.
Ігор Окіпняк, заступник директора СТОВ «Агрофірма „Маяк”»
— Ми не витрачаємо багато коштів на сушіння. Намагаємось обирати сорти й гібриди, які на момент збирання матимуть мінімальну вологість. Наприклад, торік кукурудзу збирали з вологістю 13–13,5%. Її взагалі потрібно було зволожувати, а не сушити на якісному обладнанні. Тепер користуємося газом, оскільки це економічно вигідно. Але про всяк випадок лишили місце для встановлення твердопаливних котлів.
У процесі будівництва у якийсь момент вузьким місцем стала сушарка. За добу встигали сушити тільки 500 т. Це призводило до того, що змушені були починати збирання, коли вологість кукурудзи була вищою за оптимальні значення для цього гібрида. Інакше збирання розтягнулось би в часі на невизначений термін. З другою сушаркою продуктивність сушіння збільшилась, змогли збирати кукурудзу за мінімальної вологості й таким чином зменшити загальні витрати газу. Витрати газу на зняття тонно-відсотка вологості становлять 1,3 м.
Павло Довгаль
журнал The Ukrainian Farmer, квітень 2021 року
Усі авторські права на інформацію розміщену у журналі The Ukrainian Farmer та інтернет–сторінці журналу за адресою https://agrotimes.ua/ належать виключно видавничому дому «АГП Медіа» та авторам публікацій, згідно Закону України “Про авторське право та суміжні права”.
Використання інформації дозволяється тільки після отримання письмової згоди від видавничого дому «АГП Медіа».
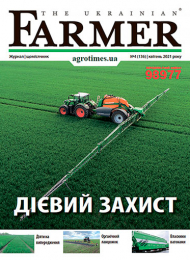