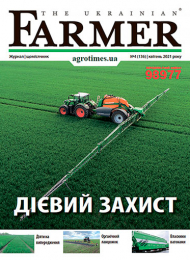
Підприємство «ВКВК», що входить до складу МХП, є найбільшим виробником комбікормів в Україні
Мегазавод по-українськи
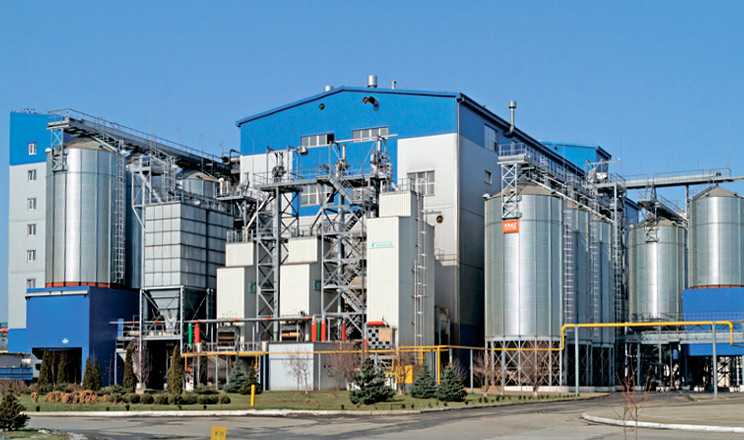
Досвід створення одного з найбільших в Україні підприємств із переробки аграрної продукції — філії «ВКВК» «Вінницької птахофабрики»
Стратегія створення заводу
Досвід великих підприємств завжди цікавий тим, що в них за одиницю часу виконується величезний обсяг робіт. Це дає цінну інформацію про ухвалення рішень, способи керування ресурсами, роботу обладнання та багато іншого.
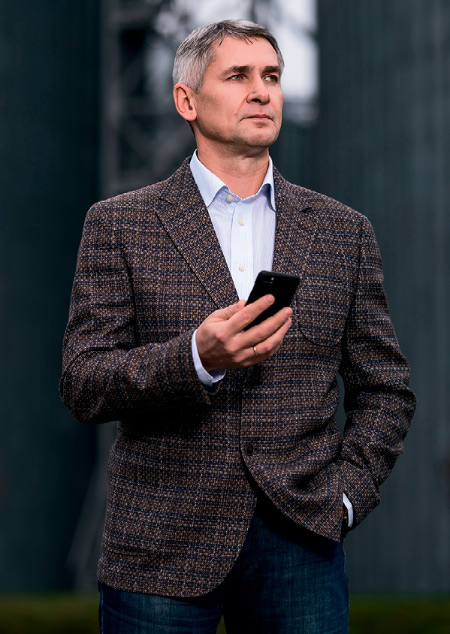
Підприємство «ВКВК», що є філією «Вінницької птахофабрики» (входить до складу МХП), на сьогодні є найбільшим виробником комбікормів в Україні (близько 15% загального обсягу), а також потужним гравцем на ринку виробництва соняшникової олії. Через підприємство через переробку щороку проходить 1,2 млн тонн зернових і олійних культур. Відвантажують тільки продукти переробки: олію, гранульоване лушпиння й комбікорм.
Підприємство будували разом із виробничими майданчиками «Вінницької птахофабрики». Із самого початку власник компанії шукав зручне місце, яке б влаштовувало за низкою параметрів. До цього в МХП вже був досвід будівництва подібного комплексу в Каневі (Черкаської обл.), тож усі вимоги вже були сформовані.
Насамперед створення птахофабрики потребувало розв’язати питання постачання кормів й утилізації пташиного посліду. На той час у Ладижині було створено аграрне підприємство «Зернопродукт» із земельним банком у 100 тис. гектарів, тому почали розглядати цей регіон як перспективний для створення нового потужного підприємства. Брали до уваги забезпечення електроенергією, природним газом, водою. Усі ці ресурси були поблизу Ладижина, тому саме тут і вирішили будувати підприємство.
Роботи стартували навесні 2010 року. Одночасно з виробничими об’єктами почали працювати й над інфраструктурою. Значні зусилля доклали для створення зовнішніх мереж газо та електропостачання. Були збудовані дві базові підстанції, куди заходять лінії класу напруги 110 кВ. Від них до птахофабрики були прокладені ліні класу напруги 35 кВ, що заходили на підстанції 35/10 кВ, і вже з них електроенергія розподіляється лініями класу напруги 10 кВ на майданчики з пташниками.
Для газопостачання в Ладижині та селі Четвертинівці реконструювали газорозподільні станції, а також виконали значний обсяг робіт із підведення газових мереж до виробничих майданчиків.
Перші об’єкти (два елеватори для олійних і зернових культур) ввели в експлуатацію восени 2011 року — вони прийняли перший урожай від агропідприємства «Зернопродукт МХП». У 2012 році запрацювали перші майданчики з вирощування птиці. На цьому етапі забезпечення комбікормом виконувало із ТОВ «Катеринопільський елеватор» (Черкаська обл.), а вже з жовтня 2012 року ввели першу лінію місцевого комбікормового заводу продуктивністю 90 т/год. Одночасно було введено в експлуатацію першу лінію олієпресового заводу продуктивністю 500 т/ добу, який окрім олії давав на виході макуху — цінне джерело білка для годівлі птиці.
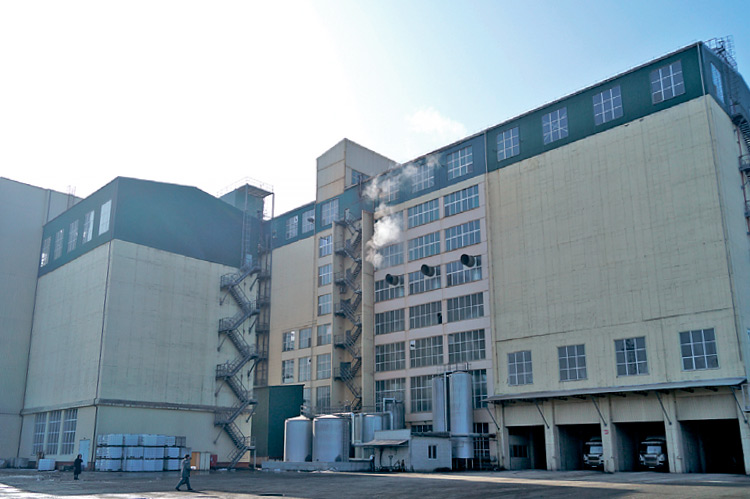
Спираючись на ефективність
Рівень автоматизації підприємства є максимально можливим. Усі процеси — під контролем автоматизованих систем керування, за якими, своєю чергою, наглядають оператори. Коли обирали обладнання для елеваторів (сушарки, очисні машини, транспортери), вирішили придбати найкраще — від німецького виробника фірми Schmidt-Seeger (нині — Buhler AG). На думку директора підприємства Вячеслава Концура, очисні машини Buhler працюють найкраще. Залежно від стану і засміченості зерна можуть відбуватися певні коливання в продуктивності та якості очищення (це притаманне всім без винятку очисним машинам), однак із машинами Buhler вдається досягати найкращих результатів за будь-яких умов. Інші машини також мають високі показники ефективності й надійності, тож для такого потужного підприємства інших варіантів бути не може.
Разом з обладнанням придбали й повний комплект автоматики з шафами керування й програмним забезпеченням. Це дало змогу досягти максимально можливого рівня автоматизації та безпеки. Навіть якщо оператор пульта керування відлучається на якийсь процес, і раптом стається збій — це не призводить до аварійної ситуації або поломки. Система датчиків дає змогу все безпечно зупинити, і далі вже людина визначає характер проблеми й вирішує про подальші дії.
На кожному з маршрутів установлено окрему очисну машину і сушарку. Якщо на елеваторі олійних культур два маршрути, відповідно, там установлено дві очисних машини і стільки ж сушарок. На елеваторі зернових культур три маршрути — відповідно, три очисних машини й сушарки.
На олійному елеваторі дві сушарки мають продуктивність по 60 т/год. З максимальною вологістю вдається сушити до 2000 т/добу, а якщо продукція відносно суха, на добу вдається приймати до 4000 т соняшнику. На зерновому елеваторі встановлено три сушарки, що мають продуктивність 90 т/год кожна (за вологості кукурудзи до 35%). Тобто загальна паспортна продуктивність зерносушарок становить 270 т/год, але, враховуючи, що не вся кукурудза приїжджає з такою вологістю, фактично вдається збільшити продуктивність сушіння кукурудзи до 7500–8000 т/добу залежно від початкової вологості кукурудзи.
Багато товаровиробників намагаються підбирати гібриди кукурудзи таким чином, щоб у період збирання вони мали мінімальну вологість. Тож фактично буває так, що кукурудза надходить із вологістю 16–22%, а в період осінніх дощів підвищується в середньому до 26–28%.
На зняття тонно-відсотка вологості сушарки в середньому витрачається 1,6– 1,7 м. газу. Все залежить від температури навколишнього середовища. У вересні цей показник менший, а в кінці листопада, коли температура знижується до нуля, витрати можуть доходити до 2 м. на тонно-відсоток.
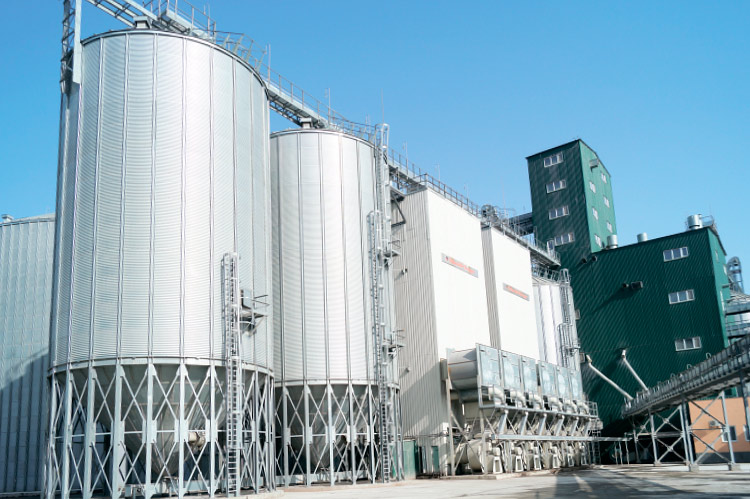
Ресурс — головний складник стабільної роботи
Значна вартість обладнання виправдовується великим ресурсом і високою надійністю обладнання. На перший погляд, ціна може здаватися надто високою, але якщо порахувати строк експлуатації, вартість експлуатаційних витрат на одиницю часу, то таке рішення є абсолютно прийнятним.
Коли настає потреба ремонтувати й замінювати певні деталі, завжди розглядаються варіанти заміни тільки на оригінальні запчастини або замінники. Однак знайти пристойну альтернативу дуже важко. Для виготовлення неоригінальної деталі потрібно розробити креслення, правильно підібрати матеріали, а потім виготовити й провести оцінювання результату в умовах експлуатації на виробництві. Це робиться і для ухвалення правильних, обґрунтованих рішень — головний механік підприємства веде облік упроваджених замінників, проводить порівняння вартості оригінальних запчастин і аналогів, оцінює їх реальний ресурс.
Основа зберігання
На обох елеваторах установлено зернові силоси іспанського виробника Symaga. Майже десятирічна експлуатація показала їх високу якість і стабільність конструкції, незважаючи на великі обсяги перевалки. Щоправда, у перший рік виявилося кілька помилок, що були допущені під час монтажу. Наприклад, кріплення кабельної термометрії виведено на дах, відповідно, після першої зими разом зі снігом «зійшли» й кріплення. До початку наступного сезону постачальник разом із монтажною організацією проблему усунули. Також не зовсім коректно було змонтовано вентиляційні клапани квадратного перерізу: їх установили на дахах так, що з одного боку нагромаджувався пил. З часом це могло стати причиною пошкодження оцинкованого шару і появи корозії. Аби уникнути такого небажаного явища підрядну організацію попросили розвернути вентиляційні клапани на 45°, щоб унеможливити нагромадження пилу. Щороку дах обов’язково миють водою, що зменшує ймовірність появи корозії від нагромадженого зернового пилу. На сьогодні силоси мають такий вигляд, ніби підприємство тільки вчора почали експлуатувати.
Олієпресовий завод
Олієпресовий завод на цьому підприємстві є третім у компанії МХП. На попередніх двох заводах вдалося набути достатньо досвіду в технології й обладнанні, що дало змогу створити максимально ефективне виробництво.
Завод складається з обладнання різних виробників. Наприклад, транспортне обладнання — від швейцарської компанії Buhler AG і французької компанії Denis. Це максимально близькі за якістю й технологічністю виробники, тому віддавали перевагу тому, хто пропонував кращі умови поставки.
Щодо сушарок, тут всі три сушарки на перший олієпресовий завод поставила компанія Buhler. Для нового заводу, який тільки розпочинає будуватися, вже придбали четверту сушарку й уклали контракт на поставку п’ятої також зі швейцарською компанією Buhler AG. Таке рішення було ухвалено не тільки через вигіднішу пропозицію. Досить зручно, коли на підприємстві однотипне обладнання від одного виробника. Це значно спрощує експлуатацію, починаючи від налаштувань, обслуговування й резерву запасних частин і закінчуючи мінімальною кількістю обслуговчих організацій. З цих міркувань обирали й очисні машини — тут працюють також сепаратори Buhler, але меншої, ніж на елеваторах, продуктивності.
Для обтрушування соняшнику встановили обладнання «Хорольського механічного заводу», який є виробником повного комплексу основного та допоміжного обладнання для рушально-віяльного відділення. Воно забезпечує достатню якість і продуктивність. Ураховуючи досвід експлуатації такого обладнання та для підвищення надійності, на наступному постачанні було досягнуто домовленості про встановлення підшипників імпортного виробника, а також установлення електродвигунів із рівнем енергоефективності ІЕ-3 турецького виробництва. Українські електродвигуни збирають із китайських складників, тому їх надійність нижча. Крім того, пильну увагу приділяють енергоефективності електродвигунів. Якщо раніше купували обладнання з електродвигунами першого або другого рівня енергоефективності, то тепер обирано двигуни третього рівня. За умови цілодобової роботи заводу переплата за вищий рівень енергоефективності окупається за рік.
Для гідротермічної обробки та пресування взяли обладнання німецького виробника Harburg-Freudenberger Maschinenbau GmbH. Очищується олія за допомогою машини шведської компанії Alfa Laval. Для охолодження макухи використовується обладнання голландської компанії Geelen Counterflow. Є інші виробники такого обладнання, але ці — визнані за якістю, підтверджені досвідом експлуатації, і щоб мінімізувати ризики, було вирішено обрати саме ці бренди.
Протягом 2013–2015 років потужність олієпресового виробництва філії «ВКВК» збільшилась до 1620 т/добу з переробки соняшнику.
Комбікормовий завод
Підприємство з виробництва комбікормів також було не першим — компанія МХП до цього вже побудувала три таких заводи: у Миронівці, Катеринополі й Таврійську. В жовтні 2012 року завершено будівництво й уведено в експлуатацію обладнання першої черги будівництва комбікормового заводу, де встановлено комплектну автоматизовану лінію продуктивністю 90 т/ год фірми Buhler AG (Швейцарія) з виробництва комбікормів з інфраструктурою для приймання сировини, відвантаження готової продукції на спеціалізований автомобільний транспорт й інженерними мережами. Оскільки Таврійське підприємство у 2015 році перестало функціонувати, обладнання з нього було демонтовано і перевезено до Ладижина. Це обладнання детально оглянули, відремонтували зношені вузли і з нього зібрали другу лінію комбікормового заводу продуктивністю 30 т/год фірми Andritz. Перед будівництвом третьої лінії провели тендер, у якому взяли участь шість європейських виробників. Виграла компанія Ottevanger із Нідерландів. Вона поставила обладнання продуктивністю 60 т/год, і в результаті загальна потужність комбікормового виробництва досягла 180 т/ год. Фактично за 2020 рік було виготовлено 948 тис. тонн комбікормів для бройлерів, що становить 15% усього виробництва комбікормів в Україні. На сьогодні щоденно відвантажують 2000–2200 т комбікормів, а в дні з максимальним навантаженням — до 3000 т.
Логістичний квест
Рух вантажів на філії «ВКВК» можна порівняти з великим портовим елеватором. Щороку тут приймають 380– 450 тис. тонн соняшнику. З цього обсягу до 100 тис. постачають із власних підприємств, усе інше — від сторонніх виробників. Закупівлі можуть відбуватись не лише у Вінницькій області, а й в інших регіонах України, звідки продукцію доставляють залізничним й автомобільним транспортом. Ураховуючи, що олієпресові заводи працюють також у Миронівці та Катеринополі, компанія МХП шукає оптимальні рішення за ціною й географією джерела постачання.
Щодо кукурудзи, нині споживання становить більше як 600 тис. тонн на рік. З них 65–70% вирощують всередині компанії, а все інше закуповують. Географія закупівель залежить від ціни та відстані до підприємства. Наприклад, якщо у Сумській області є певна партія кукурудзи, буває вигідніше її продати на місці й купити той самий обсяг десь поблизу, щоб не витрачати гроші на логістику. Також іноді практикується обмін партіями продукції між агрохолдингами, якщо це вигідно для обох сторін.
Підприємство із самого початку проєктувалось під активну роботу із залізничним транспортом. Це дало змогу відразу передбачити обсяги перевалки й розробити зручні маршрути. На території одночасно можуть перебувати до 100 вагонів. Річний обіг становить 8000–8500 вагонів. Після початку експлуатації, коли підприємство вийшло на повну потужність, побачили, що власні маневрові тепловози не встигають переміщувати вагони, оскільки робота тривала одночасно на кількох «фронтах». Відповідно, у 2015– 2016 рр. поступово всі «точки» завантаження й розвантаження було обладнано лебідками.
Практично 99% олії вивозять залізницею. Гранульоване лушпиння теж відвантажують тільки у вагони. Сировина надходить як залізницею, так і автомобільним транспортом — усе залежить від періоду, і коливання обсягів можуть становити 10–20%. На це впливають різниця в ритмічності, у цінах на перевезення, а також відстані. Вагони вигідно використовувати на далекі відстані, автотранспорт, навпаки — на короткі.
Нарощувати потужності й зменшувати витрати
Перший напрям для розвитку — це будівництво ще одного олієпресового заводу. Наявні потужності збільшаться на 1200 т/ добу і сягнуть 2820 т/добу з переробки соняшнику. Завод планується ввести в експлуатацію у квітні 2022 року. На сьогодні вже проведено тендери, обрано постачальників обладнання й підрядників для виконання будівельних робіт.
Ще одним способом покращити роботу підприємства є оптимізація логістики автотранспорту на під’їздах і безпосередньо на території. Коли автомобіль приїжджає на підприємство, його реєструють на в’їзді, це дає розуміння того, скільки автомобілів і з яким вантажем очікують вивантаження. Наприклад, якщо черга змішана, є можливість за номерами телефонів запрошувати водіїв на в’їзд.
Проїхавши КПП, водій отримує картку, у якій відмічають кожен етап маршруту всередині підприємства. Також автомобіль додатково оснащують радіоміткою, за якою можна відстежувати по секундах час на зважуванні, на контролі якості, на вивантаженні. Система дає змогу аналізувати переміщення транспорту й виявляти «вузькі» місця. Наприклад, якщо автомобіль надовго затримується на вагах, цьому процесу приділяється додаткова увага. Шукають способи зменшення витрат часу, щоб збільшити загальну продуктивність і забезпечити кращу пропускну спроможність.
Також заплановано запуск інформаційного веб-сайту з електронною чергою для кожної лінії приймання. Цим сайтом зможуть скористатись зовнішні постачальники. Наприклад, якщо фермер планує привезти продукцію, він може ознайомитися, скільки машин очікують розвантаження, й записатись в електронну чергу. Це суттєво зменшить простої автотранспорту і зменшить логістичні витрати.
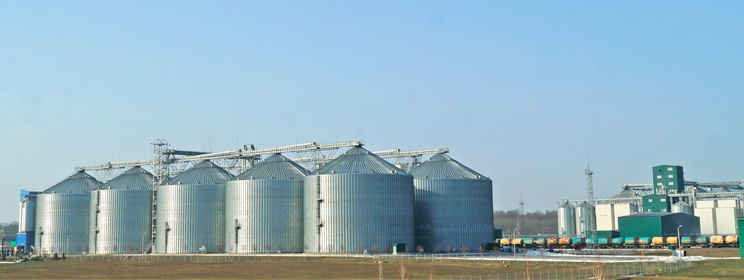
ГОВОРИТЬ ЕКСПЕРТ
Іван Невмержицький, директор департаменту «Обладнання і технології для харчових продуктів, олії та комбікормів», Buhler AG
— Це був найбільший в Україні проєкт заводу для виробництва комбікормів і найбільш значущий проєкт для «Бюлер» у Європі, успішний для обох компаній.
Ставилося завдання — збудувати завод з урахуванням найсучасніших світових напрацювань у галузі виробництва повнораціональних кормів. Як результат, конверсія вироблених кормів — на рівні найкращих світових показників. Вирішальним було саме вибрати найефективніше технологічне рішення без обмеження по габаритах будівлі й створення компонування обладнання за вертикальною схемою.
Володимир Огійчук
журнал The Ukrainian Farmer, квітень 2021 року
Усі авторські права на інформацію розміщену у журналі The Ukrainian Farmer та інтернет–сторінці журналу за адресою https://agrotimes.ua/ належать виключно видавничому дому «АГП Медіа» та авторам публікацій, згідно Закону України “Про авторське право та суміжні права”.
Використання інформації дозволяється тільки після отримання письмової згоди від видавничого дому «АГП Медіа».
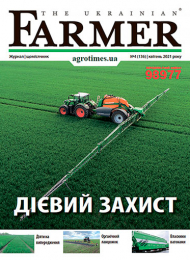