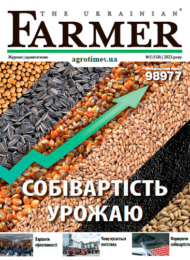
Зберігати зерно хочеться у власному елеваторі, навіть попри війну, бо чужий елеватор — це завжди дорого
З прицілом на економіку
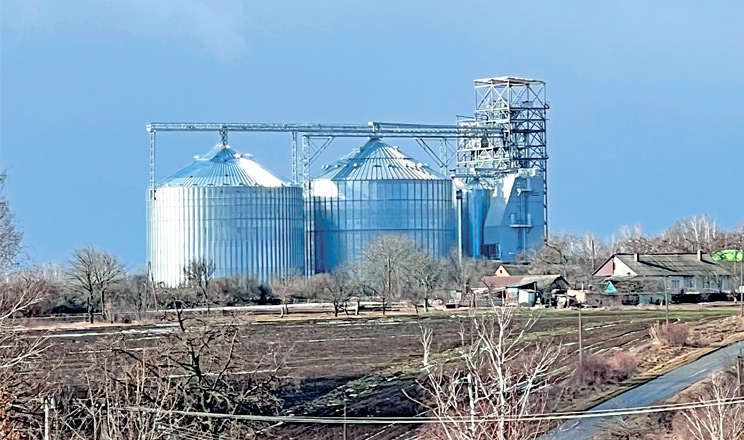
Зберігати зерно хочеться у власному елеваторі, навіть попри війну, бо чужий елеватор — це завжди дорого.
Сергій Гоцуляк, директор ТОВ «Елеватор ”Родина”», розповів, що досить тривалий час їх родинне підприємство змушене було користуватись послугами сторонніх елеваторів. Власні підлогові склади на кілька тисяч тонн давали змогу зберігати вкрай незначну в масштабах господарства кількість зерна. Тож переважна більшість збіжжя одразу прямувала до найближчих елеваторів, де виконували очищення і сушіння за потреби.
З погляду економіки такий спосіб господарювання не був ефективним, хоча й мав свої переваги — менше клопоту, менше відповідальності, більше вільного часу. Але будь-який бізнес вимагає удосконалення, щоб і далі приносити прибуток його власнику. Умови постійно змінюються, і кожен процес доводиться аналізувати й за потреби удосконалювати. Тому практично для кожного аграрія з чималим земельним банком настає момент, коли власний повноцінний елеватор із мрії перетворюється на необхідність. І справа не в наявності або відсутності грошей, а тільки в ефективності. Якщо три роки тому можна було працювати не оглядаючись на вартість доробки, то тепер тільки одне сушіння «на стороні» може «з’їсти» чималу частину прибутку. Вижити в такі часи можна лише маючи можливість власними силами керувати витратами впродовж усього виробничого ланцюжка — від сівби до відвантаження зерна.
Підприємство має в обробітку близько 4600 га, що розташовані у Вінницькій і Хмельницькій областях. Вирощують озимий ріпак, озиму пшеницю, соняшник і значну кількість кукурудзи. Потреба в сушінні досить велика: наприклад, минулого сезону довелось сушити 15 тис. тонн кукурудзи. Інші культури — це приблизно така сама кількість. Тож до останнього часу доводилось платити чималі кошти за доробку й зберігання всього врожаю. Будівництво власного повноцінного елеватора давало надію на суттєве скорочення цієї статті витрат, і наприкінці 2021 року рішення було ухвалено.
Як вибирали обладнання
Елеватор комплектували, зважаючи на доцільність й ефективність. Тож сушарку одразу запланували від шведського виробника Tornum, а силоси й транспортне обладнання вирішили придбати вітчизняного виробника. Чому саме так, розповів Сергій Гоцуляк: «Насамперед ми хотіли досягти економічного ефекту, тому шукали сушарку з відповідними технічними характерис тиками. Ми розуміли, що її початкова вартість практично не має значення — головне, щоб вона давала змогу максимально ефективно сушити зерно. Також одним із важливих критеріїв вибору була надійність — як із боку конструктиву, так і з пожежної безпеки. Поспілкувавшись із колегами-аграріями, ми вирішили зупинити свій вибір на сушарці Tornum. Досвід показав, що цей виробник забезпечує одну з найнижчих витрат палива на зняття тонно-відсотка вологи. Сушарку обладнано достатньою кількістю датчиків температури й вологості, щоб працювати в повністю автоматичному режимі й у жодному разі не пересушувати зерно».
Будували у війну
Підготовка до будівництва розпочалася наприкінці 2021-го року, а пікова активність припала саме на початок війни. Тільки замовили обладнання і здійснили перші проплати, як вранці 24 лютого ситуація в країні різко змінилась. У перші місяці бойових дій ніяких робіт не виконували, чекали бодай якогось розуміння, куди все рухається. Проте після того, як Київщину й інші північні території звільнили, будівництво вирішили продовжувати, хоч і з деякими корективами. Через те, що український виробник фізично не встигав виконати замовлення (підприємство перебувало в зоні постійних обстрілів), транспортне обладнання й один силос вирішили придбати у компанії Tornum. Першу чергу також скоротили з 30 до 20 тис. тонн одночасного зберігання, збудувавши тільки два силоси по 10 тис. тонн кожен. Один із них — шведського виробництва, другий — українського.
Перший досвід
Будівництво завершилося досить швидко — все технологічне обладнання було змонтоване до середини осені, і в кінці жовтня сушарка прийняла першу кукурудзу. Зберігання запрацювало ближче до кінця жовтня, і таким чином 15 тис. тонн кукурудзи не довелося везти на чужі елеватори. Сушити доводилося зерно з різною вологістю — від 21 до 33% (середня — 26–27%). Ураховуючи, що сушарка працювала на скрапленому газі, витрати становили 0,75 кг на тонно-відсоток. Підприємство готується використовувати теплогенератори на альтернативних видах палива. Це перспектива наступного року, бо неможливо все зробити в один момент.
Сушити цілодобово вдалося тільки в перші тижні листопада. Потім почалися труднощі з постачанням електрики, і доводилось адаптуватись до циклічного режиму роботи. Також використовували нічні часи для роботи, щоб не переривати технологічний процес. Якщо ситуація не покращиться до наступного сезону, підприємство буде змушене купувати генератор потужністю 400–450 кВт. Звісно, це додаткова інвестиція й додаткові витрати. Попередні розрахунки показують, що використання власного генератора додасть до собівартості сушіння 10–15 грн за тонно-відсоток.
ГОВОРИТЬ ЕКСПЕРТ
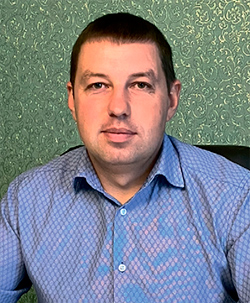
Сергій Гоцуляк, директор ТОВ «Елеватор „Родина”»
— Для нас було важливим, щоб зерно після сушіння лишалося неушкодженим і непересушеним. У сушарці Tornum встановлено достатню кількість датчиків вологості й температури, щоб система керування самостійно, без втручання оператора, регулювала процес сушіння. Таким чином, ми звели до мінімуму вплив людського чинника на якість технологічного процесу. Сушарка автоматично визначає вхідну вологість і регулює швидкість руху зерна всередині.
Оператори навчилися працювати сушаркою доволі швидко: протягом трьох днів представники Tornum були на об’єкті й повноцінно підготували наш персонал. Також знадобилося ще кілька тижнів, щоб відпрацювати всі режими роботи. Результат роботи можна було бачити впродовж усього періоду відвантаження — вологість зерна на виході становила 14%±0,5%. Це ще раз підтверджує, що наш сушильний комплекс працює так, як очікували.
Хочу зазначити, що жодних питань із чистотою немає — сушарка не викидає сміття і не забруднює довкілля.
Лабораторія готується до акредитації й цього сезону вже буде повноцінно працювати з усіма культурами. Транспортне обладнання має продуктивність 160 т/год виробництва Scandia. Футеровку самопливів виконала дніпропетровська компанія «Полімерхімгруп». Також елеватор оснащено двома очисними машинами БСХ-150 продуктивністю до 150 т/год. Одна машина очищує зерно на вході до елеватора, інша працює із зерном перед його відвантаженням. Така схема дає змогу гнучкіше підходити до процесу доробки й незалежно від погодних умов і графіків відвантаження працювати з максимальною продуктивністю.
Ситуація із відвантаженням налагодилася — ми знайшли партнерів у Румунії, вони забирають частину пшениці. Залишок реалізуємо на місцевому ринку виробникам борошна. Кукурудзу також продають на місцевому ринку, бо возити її за кордон автомобільним транспортом невигідно. Залізничне відвантаження поки що не готове, але найближчим часом ця частина проєкту також буде реалізована.
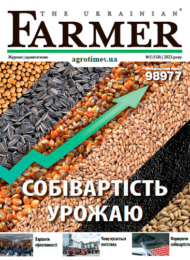