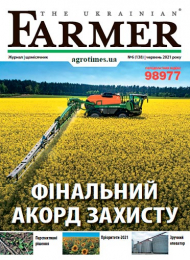
Як збудувати власний елеватор з оптимальними витратами й достатнім рівнем якості
Зручний елеватор
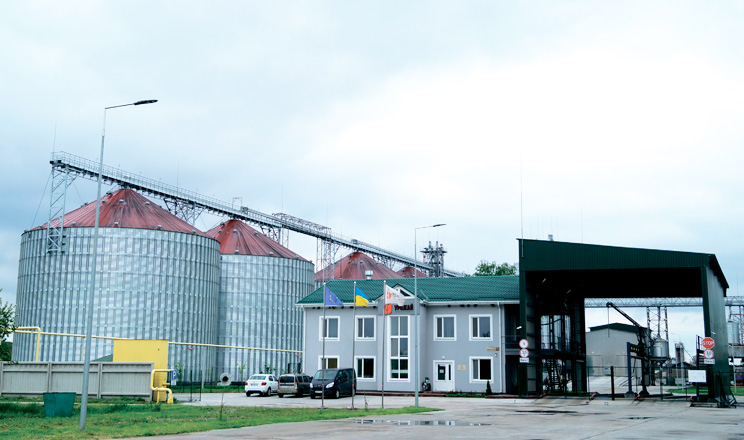
Збудувати власний елеватор з оптимальними витратами й достатнім рівнем якості можливо за правильного вибору підрядника та постачальника обладнання
Фермерське господарство «Урожай» 1996 року заснував Михайло Шевченко, який до цього працював головним агрономом у місцевому колгоспі. З часом підприємство розширилось землями сусідніх сіл — люди бачили, що фермер працює стабільно й успішно, тому віддавали свою землю йому в оренду. Наразі фермерське господарство має в обробітку більше як 11 тис. гектарів і вирощує кукурудзу, пшеницю, соняшник і ячмінь.
Коли земельний банк почав активно зростати, питання доробки й зберігання зерна постало досить гостро. Спочатку користувалися старою технікою на токах, там і зберігали зерно в підлогових сховищах. Однак із часом підприємству наявних потужностей зберігання у 30 тис. тонн забракло, і зерно повезли стороннім елеваторам. Там зерно зберігали до січня-лютого, коли ціни зазвичай зростають, і тоді його продавали. До 2018 року близько 40 тис. тонн доводилось возити за 100 км у Ромодан. Це постійно вимагало додаткових витрат на логістику, іноді взимку доводилося самостійно розчищати дорогу від снігу, щоб можна було вчасно доставити зерно. Усе це підштовхнуло власника до будівництва свого елеватора.
Після ухвалення рішення про будівництво насамперед знайшли підрядника — ним стала місцева компанія «Рубін». Це підприємство має великий досвід будівництва елеваторів, тому саме їй довірили вибрати проєктувальника і виробників обладнання — «ЛУБНИМАШ» і «Хорольський механічний завод». Якість українського обладнання на сьогодні вийшла на той рівень, коли немає сенсу переплачувати закордонним виробникам. До того ж замовник не втрачає в надійності й може отримати додатково державну компенсацію за придбання вітчизняного обладнання.
Будівництво
Підготовку документації розпочали 2017 року, за пів року до початку будівництва. Це тривало досить довго: розробка й узгодження проєкту, отримання дозволу для будівництва. Спочатку з проєктантами визначили потужність сушарок, обсяг одночасного зберігання, транспортного обладнання, приймання і відвантаження. Виходячи з цього, визначили потребу в електроенергії та газопостачанні. Звернулися до місцевих постачальників і з’ясували, що отримати максимальну потужність, визначену проєктувальниками, неможливо, однак наявні потужності також влаштовували, і відповідно до них було зроблено проєкт. Будівельні роботи тривали приблизно пів року, тож усього на створення елеватора знадобився рік. Ще на етапі будівництва побачили, що у весняний період ґрунтові води підіймаються досить високо — до рівня нижніх галерей. Після початку експлуатації таки переконалися, що це не випадково, тож змушені були зробити гідроізоляцію підземних галерей і приямків.
Монтаж технологічного обладнання виконували переважно силами спеціалістів «ЛУБНИМАШ»: вони звели силоси, сушарки, місткості для тимчасового зберігання, вузли відвантаження, змонтували частину транспортерів.
Систему автоматизації встановила компанія «Геракс». Усе робили під час монтажу обладнання, і навіть коли на транспортерах ще не встановили двигуни, кабелі вже підвели, і вони чекали на приєднання. Програмне забезпечення також розробили й установили на комп’ютери ще до початку пусконалагоджувальних робіт.
Наразі об’єкт уважається завершеним, хоча за потреби тут є всі можливості для збільшення обсягів одночасного зберігання, добудувавши додаткові силоси. Наприклад, торік було добудовано підлогове сховище на 14 тис. тонн із верхнім завантаженням, нижньою галереєю, окремою завальною ямою й автомобільним відвантаженням. Тут зерно практично не травмується, бо висота падіння не перевищує 10 м.
Приймання
На ваговому комплексі на в’їзді до елеватора встановлено тільки один автоматичний пробовідбірник італійського виробництва, який може пересуватися вздовж вантажівки й відбирати зразки з кузова автомобіля. Таке рішення аж ніяк не впливає на продуктивність роботи лабораторії й не затримує транспорт, проте коштує дешевше.
Загалом потужність приймання досить велика, враховуючи продуктивність транспортного обладнання у 175 т/год. Однак після заповнення оперативних місткостей приймання (2 ×500 т і 2 ×600 т) обмежується швидкістю сушіння. Практика показала, що підприємство здатне сушити близько 2000 т кукурудзи на добу, знімаючи 6–10%.
Норії й транспортери від «ЛУБНИМАШ» забезпечують пропускну здатність у 175 т/год. Нижні галереї оснащено стрічковими транспортерами, інші — ланцюгові.
Очисні машини
Для первинного очищення використовують скальператор СПО-175. Його залучено на прийманні, щоб відібрати пил і велике сміття перед сушінням. Після того як зерно висушать, його закладають на зберігання, і тільки перед відвантаженням пропускають через барабанний сепаратор БСХ-200. Зазичай лише нижні шари зернового масиву в силосі потребують доочищення, бо травмується під час завантаження. Відходи віддають у тваринництво.
Сушіння
До будівництва елеватора у відділках активно використовували сушарки «Бриг» на соломі й щепі, але вони не встигали сушити весь обсяг зерна. З появою двох сушарок «ЛУБНИМАШ» продуктивністю 65 т/год кожна практично весь обсяг зерна висушують не елеваторі. Також надають послуги із сушіння іншим фермерам.
Сушарки на елеваторі чистять приблизно раз на тиждень. У зміні працює всього одна людина, яка налаштовує й контролює сушіння. Сушарки оснащено трьома рівнями датчиків температури, за допомогою яких можна регулювати сушіння залежно від культури, вологості й вимог до ощадності. Вологість вимірюють вручну перед завантаженням в оперативні місткості та на виході із сушарки (кожні пів години). Зазвичай цього достатньо, але якщо на виході із сушарки показники вологості нестабільні, додають ще одну перевірку — безпосередньо перед входом у сушарку.
Ураховуючи, що одночасно працюють дві сушарки, можна розділяти потоки з різним умістом вологи. На одну сушарку подають зерно з умістом вологи меншим як 20%, на другу — з умістом вологи більшим за 20%. Таким чином немає потреби постійно змінювати налаштування сушарок. Вони працюють у сталому режимі, і навіть якщо вхідні параметри зерна змінюють, то тільки в незначних межах. Крім того, є можливість одночасно працювати з кількома культурами або своїм і давальницьким зерном.
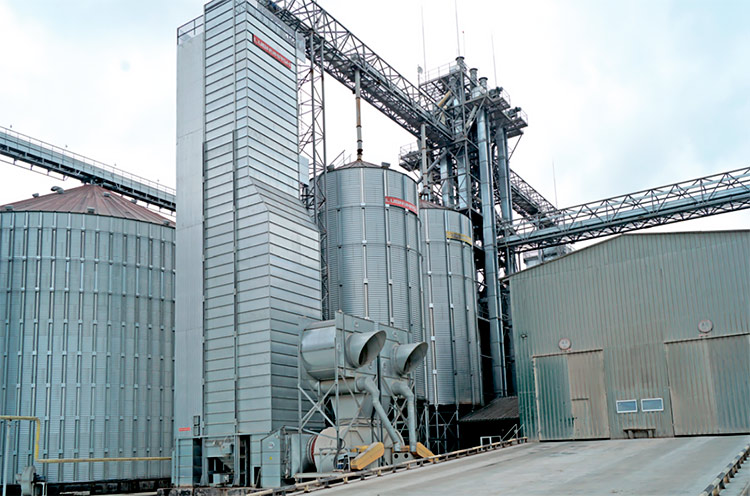
Сушарки оснащено циклофанами, які практично повністю видаляють пил і летку домішку з відпрацьованого повітря. Таким чином, територія елеватора практично не потребує прибирання, а прилеглі території навіть теоретично не можуть забруднюватись. Пил і сміття збирають у мішки й вивозять.
З власного зерна сушать пшеницю і кукурудзу. Із соняшником ситуація дещо інша. Останні роки соняшник практично не потребує сушіння, збирання також відбувається без попередньої десикації. Отже, для скорочення логістики й зменшення пошкоджень було вирішено сушити цю культуру на токах, і там його лишати на зберігання в підлогових сховищах.
Силоси
Компанія «ЛУБНИМАШ» поставила на цей об’єкт 7 силосів по 10 тис. тонн. Силоси обладнано двома витяжними вентиляторами на даху і чотирма аераційними, які використовують для охолодження зерна після сушіння й запобігання самозігрівання під час тривалого зберігання. В конструкції даху застосовано ферми, що забезпечує кращу несну здатність і стійкість до снігових і вітрових навантажень. На дахах є полімерне покриття, що збільшує довговічність конструкції, а також зменшує температурні коливання.
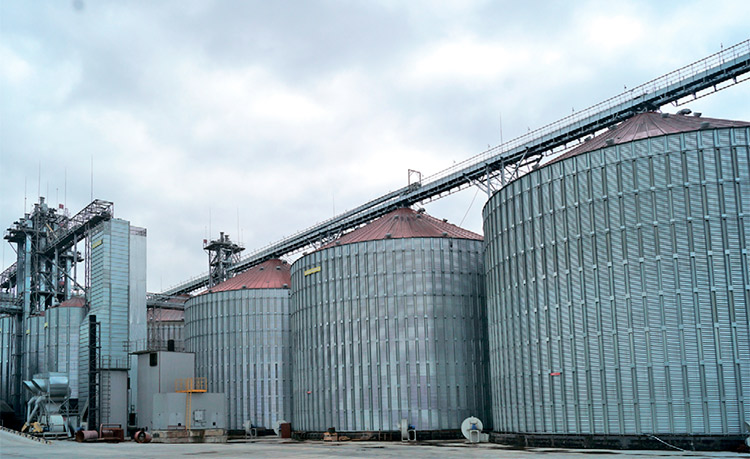
Для контролю стану зерна використовують кабельну термометрію. Кожна оснащується 30 кабелями, чого цілком достатньо, щоб детально оцінити стан усього зернового масиву. Зачисні шнеки встановлено також від «ЛУБНИМАШ», і за цей час вони показали себе надійними та високопродуктивними.
Відвантаження
Для відвантаження передбачено дві залізничні гілки, на кожну з яких стає по сім вагонів. Потужності блока відвантаження цілком достатньо для завантаження маршруту за 24 год, однак для цього потрібно швидко подавати порожні вагони й відвозити на станцію заповнені. Локомотив від Укрзалізниці досить часто доводилося чекати по 3–4 години, що спричиняло суттєві затримки з відвантаженням і аж ніяк не влаштовувало власника підприємства. Тому було вирішено придбати власний локомотив, і з цього сезону на формування маршруту буде витрачатися не більше як доба.
Для відвантаження зерна у вагони використовують чотири оперативні місткості, які вміщують по 40 т. Таким чином, кожен вагон завантажується з двох місткостей. На пункті автомобільного відвантаження встановлено дві місткості по 30 т.
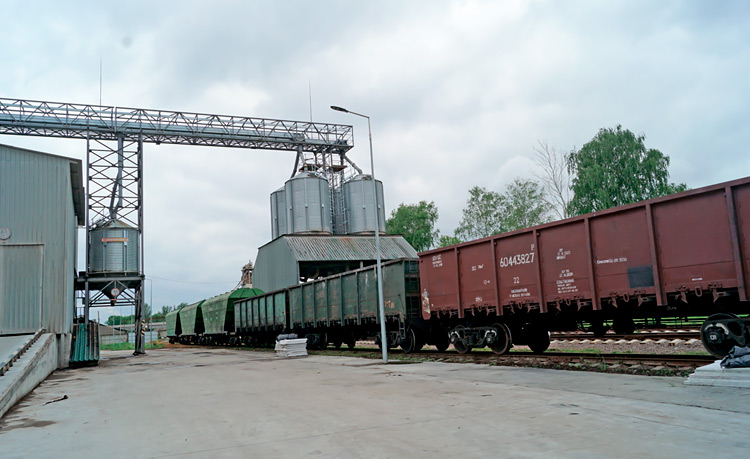
Відвантаження в автомобільний транспорт має приблизно таку саму продуктивність — 160 т/год. Однак практично всі обсяги зерна вивозять залізничним транспортом. Автомобілі застосовують тільки для внутрішніх переміщень, а також коли поклажодавці забирають своє зерно. Торік елеватор перевалив 98 тис. тонн власного зерна і 36 тис. стороннього. Підприємство планує збільшувати обсяги перевалки, оскільки для цього є всі можливості. Власний тепловоз суттєво пришвидшить формування маршрутів, збільшиться оперативність відвантаження і відправлення зерна покупцям. Інфраструктура дозволяє паралельно працювати з власним і стороннім зерном на повністю відокремлених лініях. Ще однією перевагою елеватора є планування роботи таким чином, щоб не утворювати черги з багатьох десятків вантажівок. Транспорт не повинен чекати, бо це автоматично призводить до простоїв комбайнів.
Персонал
Усього на елеваторі працюють 33 працівники. З тим сім — працює на зміні. Це оператор, один або два оператори сушарки, залежності від того, одна чи дві сушарки працюють, приймальник, вагар і лаборант. Також у робочі дні працюють слюсар і електрик, бухгалтер і завідувач лабораторії. З появою власного тепловоза на зміні працюватиме машиніст і складач поїздів.
ГОВОРИТЬ ЕКСПЕРТ
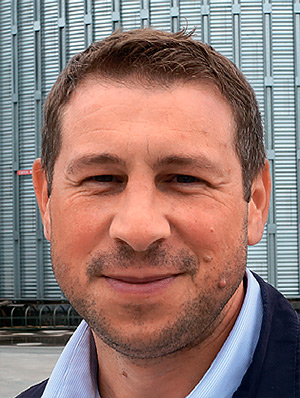
Володимир Шевченко, заступник голови правління
— Ми добре розуміємо фермерів, тому в роботі зі сторонніми поклажодавцями намагаємось запропонувати саме такі умови співпраці, які були б максимально зручними. Вони шукають, куди діти зерно відразу після збирання, і до того ж треба планувати комбайни й автотранспорт. Далеко не всі елеватори можуть оперативно приймати зерно від сторонніх поклажодавців. Великі черги, пріоритет для власного транспорту і великих клієнтів змушують фермерів шукати альтернативу. Ми можемо це забезпечити й пропонуємо нормальні ціни. Наша лабораторія сертифікована, видає чесні показники, які можна перевірити будь-де. Ми співпрацюємо з компаніями «НІБУЛОН» і «Кернел», через них продаємо власне зерно. Також можемо запропонувати продати збіжжя своїм поклажодавцям.
Торік головним викликом були погодні умови, хоча для Сумської й Чернігівської областей усе пройшло відносно легко. Що запропонує природа цього річ — сказати важко. Зафіксували аномально холодну весну, що вплинуло на терміни сівби. Однак загрози врожайності поки що не бачимо. Більше турбує відкриття ринку землі — мабуть, саме це питання стане основним цього сезону для кожного аграрія в Україні. За нашими очікуваннями від 10 до 20% власників паїв захочуть одразу продати землю, і залежно від того, хто її купить, трансформуватиметься структура земельного банку.
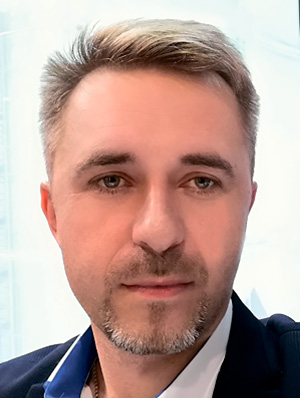
Олег Сад, головний конструктор ПП «ЛУБНИМАШ»
— Під час будівництва власник разом із підрядниками щотижня влаштовували наради, що дало змогу уникати тривалих затримок. Хочу зазначити, що з нашого боку затримок не було — усі питання, що виникали під час роботи, вирішували оперативно.
Замовник ухвалив вдале рішення, обравши мотор-редуктори німецького виробництва з двигунами третього класу енергоефективності. В результаті було отримано економію електроенергії, а також більш плавну роботу транспортерів без вібрацій і шумів.
Транспортне обладнання має продуктивність 175 т/год, що дає змогу приймати великі обсяги зерна і не створювати черг перед елеватором. Ураховуючи, що дві сушарки мають сумарну потужність 130 т/год, транспортери не будуть завантажені на усі 100%. Відповідно, їх ресурсу вистачить на довше. Корпуси транспортерів виготовлено з оцинковки, що сприяє їх довговічності й не вимагає фарбування.
За нашою рекомендацією власник вирішив установити на силосах дахи з полімерним покриттям фінського виробництва. Тож протягом десятків років вони легко витримають вплив природних чинників. Важливо, що кожен сектор у процесі монтажу лишається вкритим додатковою захисною плівкою, яка знімається тільки після завершення збирання даху.

Наші сушарки показали себе досить ефективними — вони витрачають 1,2–1,3 м³ газу на зняття тонно-відсотка вологості. Власник спочатку збирався встановити вологоміри на вході й виході, але генеральний підрядник переконав, що можна спокійно працювати й без них. У результаті оператори спостерігають за температурою в різних зонах сушарки, і таким чином забезпечують доведення вологості до заданих показників.
Елеватор розпочав роботу ще до остаточного завершення монтажу усіх силосів. Коли зводили два останніх силоси, інші вже наповнювали зерном. Протягом доби приймали по 1000 т і більше: торік із токів звозили висушене зерно на зберігання, тож не було потреби застосовувати сушарки. Загалом монтаж обладнання тривав близько шести місяців.
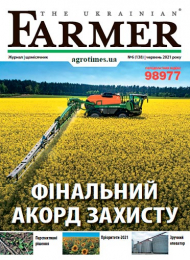