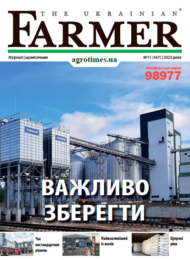
У сучасних умовах вузькоспеціалізовані елеватори прагнуть розширити свої можливості шляхом модернізації
З прицілом на оберти
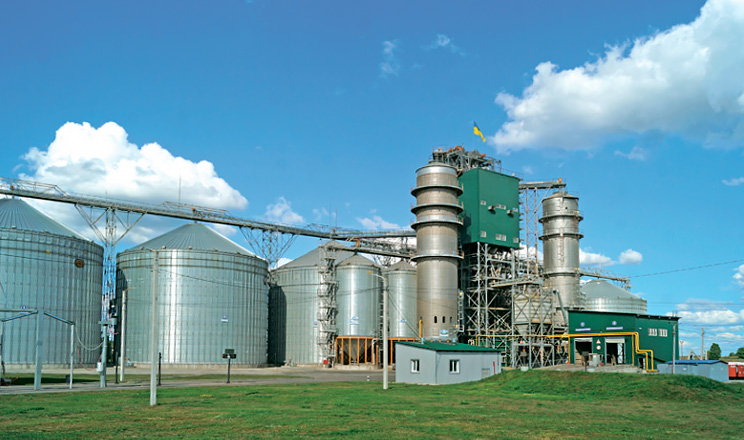
У сучасних умовах вузькоспеціалізовані елеватори прагнуть розширити свої можливості шляхом модернізації.
Кукурудзяна концепція
Коли 2012 року ТОВ «Сігнет Холдинг» починав будівництво елеватора в Андрушках Житомирської області, власники розраховували на те, що основною культурою, з якою працюватиме підприємство, буде кукурудза. Для цього поїхали у Сполучені Штати Америки подивитись, які технологічні схеми застосовують і яким обладнанням користуються заокеанські фермери. Узявши до уваги цей досвід, розпочали проєктування й будівництво власного підприємства.
У результаті було створено елеватор потужністю 60 тис. тонн одночасного зберігання. Тут є шість силосів по 10 тис. тонн, дві баштові сушарки, дві завальні ями, дві лінії відвантаження на автомобільний і залізничний транспорт. Транспортне обладнання має продуктивність 200 т/год. Усе обладнання придбали в компанії GSI. Винятком стали очисні машини — вони мають німецьке коріння.
Після 2016 року тенденції в українському рослинництві змінились. Було ухвалено рішення працювати не лише з кукурудзою, а й з іншими культурами: соєю, пшеницею, ячменем і навіть соняшником. Не приймають тільки ріпак — баштові сушарки не розраховано для такого формату зерна.
Ранню зернову групу приймають по 30–50 тис. тонн за сезон і завжди намагаються відвантажувати їх до початку збирання пізніх культур.
Елеватор із самого початку проєктували як маршрутний. За добу встигають відвантажувати до 35 вагонів. Є два власних тепловози: один працює на лінії між елеватором і залізничною станцією (відстань — 14 км), а другий працює на місці, обслуговуючи одночасно потреби елеватора і місцевого цукрового заводу, що також належить «Сігнет».
Оперативне приймання
Елеватор не робить преференцій власному автотранспорту — і свої, і «чужі» вантажівки заїжджають у порядку живої черги. Зазвичай очікувати доводиться недовго. Наприклад, у період збирання ранніх зернових перед ворітьми можуть стояти 2–3 машини. Це досягається завдяки оперативній і злагодженій роботі всіх підрозділів — від вагаря до оператора приймання. Приймальні бункери вміщують по 120 т, і машини можуть вільно розвантажуватись одна за одною, не очікуючи звільнення завальної ями.
Ще на етапі завантаження зерна в машину фіксується тип культури, і коли водій підносить картку до зчитувача на в’їзді, оператор знає, що в кузові. Після зважування лабораторія отримує завдання визначити якісні показники й внести їх у систему. На кожному етапі працює пропускна система, і якщо раптом будь-яку інформацію не внесено до системи, автомобіль не виїде за межі елеватора.
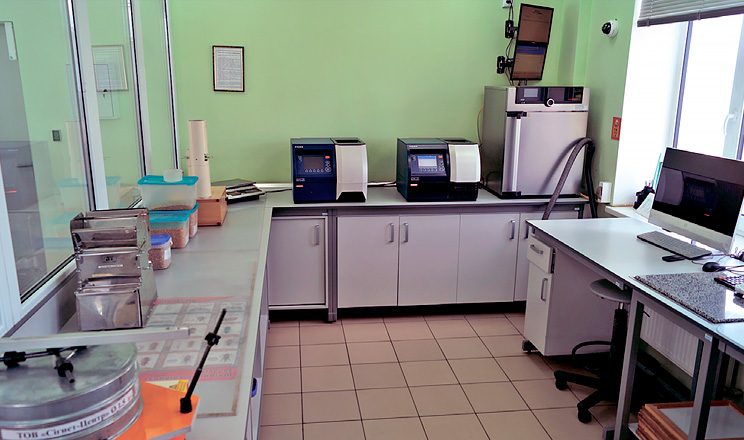
Іноді автомобіль може затриматись, наприклад, коли різко змінюється показник якості — може бути високий уміст смітної домішки або погіршується клас чи вологість завелика. Таку машину відразу зупиняють, власнику зерна телефонують і повідомляють про ситуацію. Якщо той погоджується, працюють далі. Якщо ні, тоді welcome до лабораторії робити аналізи разом. Практикують присутність представників поклажодавців, які контролюють вагу, якісні показники зерна і навіть знімають пломби з тентів. Усе залежить від алгоритмів роботи служб безпеки. На прохання виводять середньодобові показники для кожного поклажодавця.
Очищення без зауважень
Очищають зерно на сепараторах Buhler TAS 206 продуктивністю 200 т/год, а також на двох скальператорах німецького виробництва, які застосовують тільки для попереднього очищення кукурудзи. Пшеницю, сою і соняшник чистять тільки сепараторами Buhler. Вони забезпечують високу якість за будь-яких умов і водночас демонструють розрахункову продуктивність. В експлуатації німецька техніка показала себе з найкращого боку. За 10 років замінили один двигун і щосезону міняють паски. За потреби замінюють очисники сит — це витратний матеріал. Крім того, виконують передсезонне очищення й періодичний огляд очисних машин — більше уваги вони не потребують. Заміна всіх решіт (48 м.) триває не більше як годину. Це досить зручно, коли доводиться налаштовувати очищення нової культури.
Для очищення від пилу і дрібного леткого сміття по всьому елеватору застосовують рукавні фільтри. Це значно зменшує забруднення довкілля й, відповідно, скорочує час на прибирання території й очищення обладнання.
Непросте сушіння
Баштові сушарки переробити під використання альтернативного палива неможливо. Тому доводиться їх використовувати аж до моменту фізичного зношення. Знову ж таки, враховуючи оберти підприємства, цей час наближається.
Продуктивність сушіння по кукурудзі — 100–110 т/год, а витрати за нульової температури повітря — 1,4 м./т/%. Влітку для сушіння пшениці вологістю 20–22% й температури повітря близько +20 °С достатньо 0,6 м. газу для зняття тонно-відсотка. Продуктивність по пшениці доходить до 180 т/год.
Робота сушарок максимально автоматизована. Після запуску і встановлення потрібних параметрів оператор тільки стежить, щоб не було відхилень. Комп’ютер орієнтується на датчики температури й вологості та самостійно регулює швидкість вивантаження. Також сушарки оснащено пожежними датчиками: якщо температура перевищує порогове значення, сушарка автоматично зупиняється.
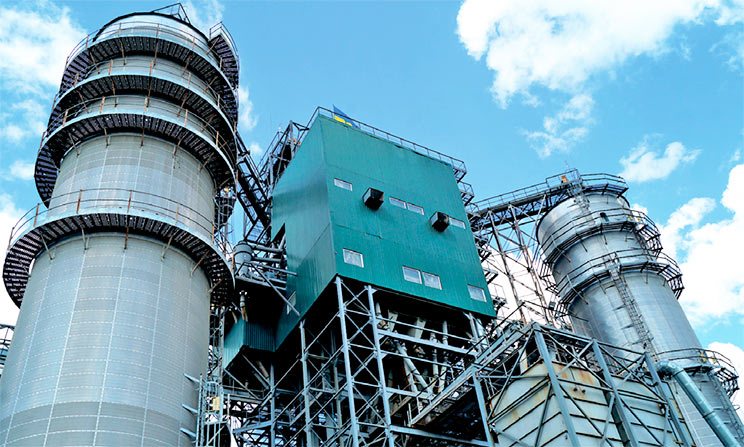
Кукурудзу з великим умістом вологи сушать у два проходи — для цього використовують дві сушарки. Перша знімає вологу до 24%, друга досушує до базового рівня. Після першої сушарки зерну дають відлежатись для кращої вологовіддачі.
Соняшник спочатку боялись сушити власними баштовими сушарками через небезпеку займання соняшникового пилу. Довелось навчитись регулювати пальники так, щоб знизити ризик загоряння до мінімуму. Під час сушіння соняшнику поруч стоїть пожежна машина, окрім автоматики працівники постійно застосовують візуальний контроль.
Очищення сушарок виконують за напрацьованим алгоритмом. Наприклад, упродовж сезону пшениці сушарку чистять двічі. На соняшнику підхід зовсім інший — сушарки чистять кожну зміну — це триває близько години. Раз на тиждень виконують генеральне прибирання — звільняють усі шахти, всередині чистять усі місця, де може накопичуватись пил. З кукурудзою очищення виконують зазвичай раз на 3–4 дні, але всі 18 колон перевіряють кожну зміну.
Оборотність на максимумі
Річні обсяги перевалки в найкращі часи становили 7–7,5 оберту. Однак у середньому вдається пропускати 240–290 тис. тонн на рік. До війни легко встигали повністю звільняти елеватор перед початком нового сезону, проте нині через ускладнену логістику є незначні перехідні залишки.
Кукурудзи перевалюють 200–250 тис. тонн на рік. Добова продуктивність сушіння кукурудзи за вологості 22–24% становить 4,5–5,2 тис. тонн. Зерно надходить цілодобово як із власних полів, так і з фермерських. Спочатку працювали більше з власним збіжжям. Його частка сягала 70%. Проте в останні роки пріоритет змістився у бік сторонніх поклажодавців. Частину власного зерна спрямували до нового елеватора компанії у Козятин, а в Андрушках збільшили приймання від місцевих фермерів. Наприклад, частка давальницької кукурудзи зросла до 50%. Упродовж кукурудзяного сезону доводиться працювати цілодобово протягом двох місяців, зупиняючись тільки для профілактики обладнання.
Торік обсяг перевалювання становив усього 200 тис. тонн. Якщо враховувати велику врожайність цього року, перевалка може зрости до семи обертів, але це буде і внутрішня логістика — із силосів у рукави. Цей спосіб зберігання тут активно застосовують упродовж усього періоду експлуатації елеватора. Мінімальна кількість у рукавах — 30 тис. тонн, максимальна — 180 тис. Певною мірою це вимушений крок, адже за умови добового приймання 4,5–5 тис. тонн кукурудзи відвантажувати таку саму кількість не вдається. Маршрут (3500 т) відправляють за 40 год, тому разом із вагонами завантажують і рукави. У такому режимі добовий обсяг відвантаження становить 7,5 тис. тонн. Завантаження в рукави відбувається аж до завершення жнив. Як тільки в силосах звільняється місце, зерно з рукавів починають переміщувати у металеві місткості.
У вагони й бігбегі
Основне відвантаження відбувається через залізницю. Спочатку фронт подачі становив 10 вагонів, але з часом його збільшили до 15. Це суттєво зменшило навантаження на бригаду машиністів і пришвидшило процес відвантаження загалом. Наявність двох тепловозів допомагає оптимізувати менеджмент вагонів: доки один тепловоз відвозить заповнені вагони на станцію, другий ставить порожні під завантаження.
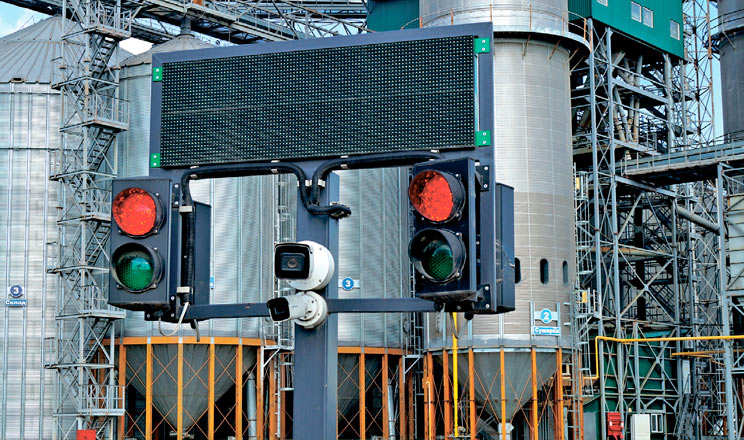
Під час війни довелось вантажити зерно у 40-футові контейнери на платформах. Один із поклажодавців своє зерно відправляв у Польщу в напіввагонах. Усередину встановлювали вкладиші і вантажили зерно. Це потребувало трохи більше часу, але в таких умовах використовували будь-яку можливість для відвантаження. Також вантажили зерно у бігбеги і відправляли автотранспортом в Прибалтику. Спочатку за день вдавалось завантажувати п’ять автомобілів, але згодом продуктивність зросла до 12 машин.
Що змінилось
Упродовж експлуатації елеватор поступово модернізували. На момент будівництва компанія GSI запропонувала використовувати їх технологію, яка передбачала роботу здебільшого з кукурудзою. Щоб бути гнучкішими в прийманні різних культур, зробили кілька нових маршрутів, додали кілька нових клапанів, футерували самопливи. Торік розпочали замінювати норійні стрічки. Для збільшення продуктивності приймання удосконалили лабораторію, придбавши прилади Інфратек. Тепер усі базові показники визначають протягом кількох хвилин, а загальний час перебування вантажівки на території елеватора скоротився до 15 хв.
На кількох транспортерах у приймальних зонах замінили днище. Почали обговорювати заміну сушарки — метал помалу протирається, сітчасті пластини лопаються. Їх ремонтують, але настає момент, коли ремонти стають економічно недоцільними. Розглядають варіанти шахтних сушарок і прораховують доцільність застосування альтернативного палива. Крім того, оцінюють можливість встановлення додаткових силосів, щоб зробити підприємство гнучкішим. Хоча, за словами директора елеватора Сергія Гуцулюка, вартість зберігання в рукавах на сьогодні є найнижчою.
ГОВОРИТЬ ЕКСПЕРТ
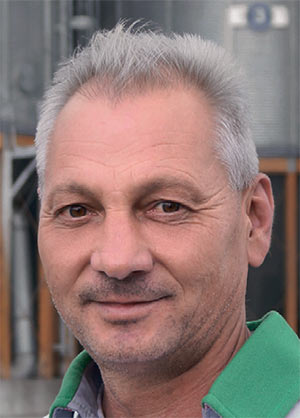
Сергій Гуцулюк, директор Андрушківського елеватора
— В елеваторному бізнесі я працюю з 2001 року, і ще жод ного разу не було схожих сезонів. Щороку щось змінюється — від погоди й сівозміни до логістики та технологій. Завжди потрібно бути готовим до будь-якого розвитку подій, тому підготовку до нового сезону розпочинаємо ще взимку: у грудні-січні проводимо тендери, купуємо запчастини й витратні матеріали. Завжди тримаємо солідний запас запчастин, щоб у разі потреби не доводилось зупиняти елеватор на тривалий час. Після зими оглядаємо всі конструкції, і бригада промислових альпіністів їх очищує, а за потреби — фарбує. Після цього виконуємо фумігацію силосів, транспортного обладнання й інших об’єктів елеватора, що контактують із зерном. Наступним кроком є подача заявки до Держпродспоживслужби на акредитацію елеватора для експорту в Китай таких культур, як пшениця, ячмінь, соя і кукурудза.
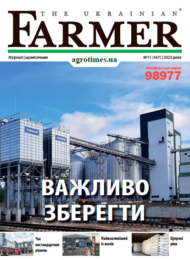