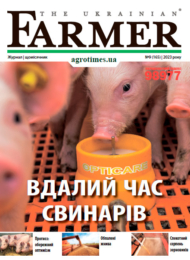
Власний елеватор скоротив логістичні витрати, зменшив собівартість продукції й відкрив шляхи для подальшого розвитку підприємства
Нічого, крім найкращого
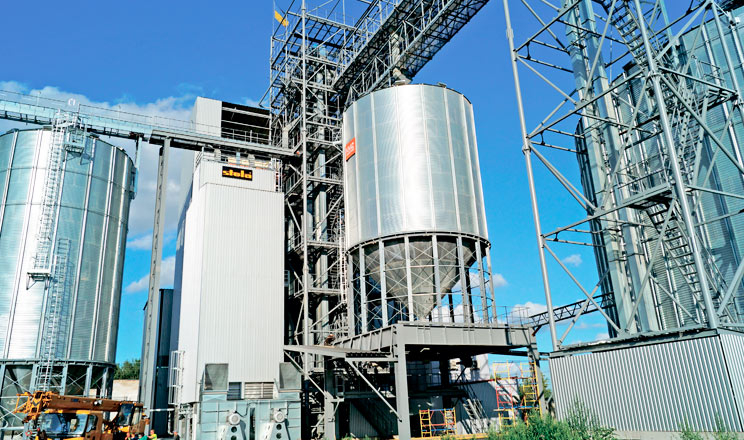
Власний елеватор скоротив логістичні витрати, зменшив собівартість продукції й відкрив шляхи для подальшого розвитку підприємства.
Ми завітали до ПП «Агрон», що на Тернопільщині, щоб дізнатись, як будівництво власного сучасного елеватора вплинуло на діяльність підприємства.
Роман Березовський, заступник директора з юридичних і земельних питань, розповів, що на сьогодні тут обробляють близько 3500 га угідь, вирощують озимий ріпак, озимі пшеницю та ячмінь, сою, соняшник і кукурудзу.
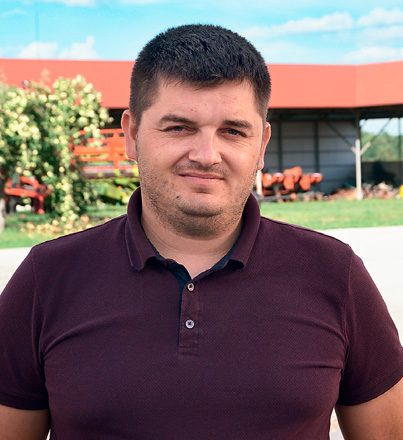
Саме на кукурудзу роблять ставку, і саме під цю культуру придбано повний комплекс найсучаснішої техніки — від сівалок FendtMomentum у повній комплектації до комбайнів Claas Lexion на гусеничних рушіях. Взагалі підхід до технічного оснащення в підприємстві особливий — власники намагаються купувати тільки якісні високопродуктивні машини, що гарантують найвищий рівень технологічності.
Процеси доробки й зберігання зерна у ПП «Агрон» пройшли низку етапів розвитку. У перші роки взагалі не було можливості самостійно сушити й очищувати зерно. Техніка, що лишилась після колгоспу, була малоефективною, тому використовували мало.
У той час багато користувались послугами сторонніх елеваторів і ХПП. Це не завжди було зручно і вигідно. Елеватори беруть зерно від багатьох фермерів, і питання черг, лабораторій і розцінок періодично відбирало частину заробітку. Особливо на ефективність роботи впливали черги. Коли вантажівки стоять, комбайни також не працюють, і це чималою мірою впливало на ефективність виробничих процесів.
Важливим моментом стало придбання зернової сушарки, завдяки якій суттєво зменшилась собівартість сушіння зерна. Її продуктивність становила 150– 300 т кукурудзи на добу, і на той час цього було достатньо для потреб підприємства. Однак подальше розширення земельного банку і збільшення частки кукурудзи в структурі посівів змусив власників замислитись над будівництвом власного повноцінного елеватора.
Новий рівень
Майданчик для елеватора навмисне обрали в промисловій зоні населеного пункту, щоб шум і викиди жодним чином не заважали місцевим жителям. До будівництва готувались досить довго: вивчали обладнання різних виробників, їздили до колег переймати досвід. На кінець 2021 року розпочали будівництво з таким розрахунком, щоб на середину жовтня 2022 року елеватор розпочав повноцінну роботу. Однак втрутилась війна, і доки ситуація не стабілізувалась, будівництво загальмувало. Потім усе ж вирішили продовжувати, але інтенсивність будівництва вже не могла буди такою, як до війни. Здали об’єкт в експлуатацію ближче до кінця року, і першу кукурудзу елеватор прийняв у сере дині січня 2023 року.
Сушарка є серцем елеватора, отже, власники ретельно проаналізували ринок і сформували для себе всі вимоги, яким має відповідати це обладнання. Вивчали всі бренди, представлені в Україні, їх функціонал і конструктивні особливості, слухали відгуки користувачів. Кінцевою метою було обрати саме таке обладнання, яке б дало змогу виконувати роботу максимально якісно. І з того, що розглядали, за характеристиками, будовою й новаціями сушарка Stela пристала найкраще, бо забезпечує ощадне сушіння, практично не пошкоджуючи зерно.
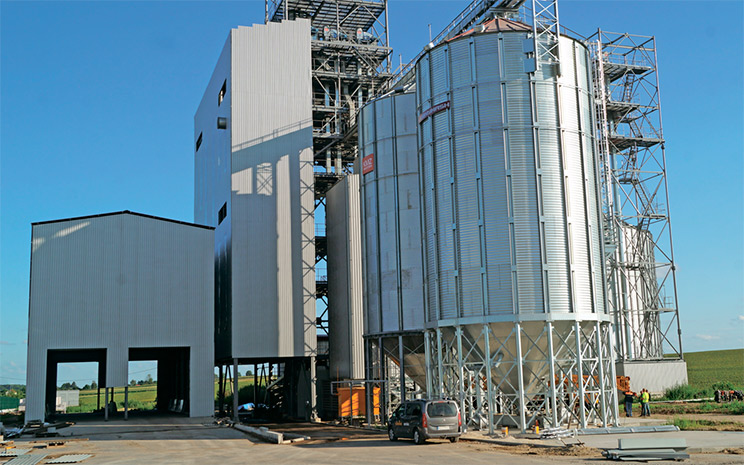
Оскільки повноцінний сезон ще не відпрацювали, зробити висновки щодо роботи сушарки досить складно. На сьогодні напрацювання становить до 6 тис. тонн кукурудзи. Культури збирали в січні, бо в запланований осінній час погода не дозволила це зробити. Сушили за температури –10…–20 градусів, вологість зерна —28–32%. Сушили за один прохід, що є граничними нормами для сушіння кукурудзи. Сушарка впоралась із завданням добре, але витрати газу були дещо більшими, ніж це могло бути за сприятливіших умов. Звісно, «допомогли» вимикання електроенергії — періодичні зупинки сушарки зменшували ефективність роботи. Допомагав дизель-генератор, але певні паузи все одно виникали, бо перемикання на аварійне джерело живлення потребувало певного часу. Добре, що сам генератор встигли придбати й установити ще до виникнення ажіотажного попиту. Цей сезон планується відпрацювати повноцінно, і є впевненість, що робота піде легше,бо за плечима — торішній досвід. С
Сушарка Stela показала фактичну продуктивність 580–600 т/добу, хоча за нормами мали вийти на продуктивність у 670 т/добу. Це пояснюється досить несприятливими умовами роботи:часті зупинки, вологість 30% і вище,низька температура навколишнього повітря (до –20 °С). Виробник стверджує, що за умов стабільної роботи (без зупинок кожні 3–4 год на перемикання до мережі чи генератора) сушарка вийде на заплановану продуктивність.
Елеватор із перспективою
До першої черги будівництва ввійшов один силос на 8700 м. від КМЗ, два хопери тимчасового зберігання (один — від КМЗ, другий — від «Лубнимаш»). Транспортне обладнання складається з двох ліній приймання по 175 т/год. Тобто розраховувати можна на 150 т/год з кожної лінії. Для первинного очищення застосовують вітчизняний сепаратор OLIS, а на вторинне встановили очисну машину Buhler.
Елеватор проектували із запасом — на сьогодні чотири комбайни намолочують 1500–1700 т пшениці на день. Тому одна з ліній приймання здатна таку кількість зерна прийняти. Друга лінія ще не готова: її будують тільки на перспективу. Власники не до вподоби щось переробляти або змінювати невдовзі після завершення будівництва. Тож спочатку ретельно вивчили можливі шляхи розвитку підприємства й елеватора як окремої виробничої одиниці, і з урахуванням цього створювали технічне завдання на проєктування.
Із сушінням питання також остаточно не закрито. Наприклад, першу сушарку розмістили якомога ближче до робочої вежі, щоб досягти максимальної продуктивності. Для цього передбачалась робота тільки на природному газі. Це стабільне джерело енергії, з яким легко працювати. Тут прості регулювання, сушіння максимально автоматизоване і безпечне. На кінцевому етапі будівництва елеватора передбачено встановлення другої сушарки з твердопаливним теплогенератором. Це дасть змогу зменшити витрати на сушіння й бути гнучкішим в умовах нестабільних цін на енергоносії. Другу сушарку встановлять на певній відстані від основного комплексу задля безпеки. Таким чином, підприємство обиратиме вигідніше джерело енергії,не втрачаючи продуктивність і якісні показники.
Що отримали
Перша черга елеватора тільки почала роботу і ще не показала всі свої переваги повною мірою. Окрім очевидної економії витрат на сушінні й очищенні відчутно зменшились витрати на логістику зерна під час збирання. Наприклад, цього року пшеницю звозили всього чотири вантажівки замість шести, і, відповідно, додатковий транспорт не винаймали. Також є впевненість, що, незважаючи на потенційні загрози, сезон відпрацюють нормально, не порушуючи технологію і оптимальні терміни.
ГОВОРИТЬ ЕКСПЕРТ
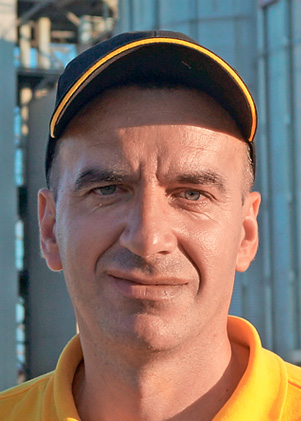
Андрій Януш, представник компанії Stela в Україні
— Це вже п’ятий об’єкт у Тернопільській області, де встановлено сушарку фірми Stela. Для ПП «Агрон» ми встановили модель MDB XN 2/13-SU продуктивністю 30 т/год кукурудзи зі зняттям 14% вологості (з 28 до 14%). З пшеницею сушарка здатна працювати значно швидше — до 100 т/год. Витрати газу становлять 1,1–1,3 м. на тонно-відсоток. Корпус сушарки теплоізольовано мінеральною ватою завтовшки120 мм, чого не пропонує жоден виробник. Система рекуперації дає змогу сушити кукурудзу з меншими втратами тепла, тоді як для олійних культур ця функція вимикається задля безпеки. Сушарка повністю виготовлена з легованого алюмінію, тому навіть через 30 років вона на вигляд буде такою самою, як сьогодні. Монтаж виконувала українська бригада під керівництвом нашого шеф-монтажника. За часом весь процес тривав близько двох місяців, оскільки бригада вперше мала справу із сушаркою саме цього виробника. Бригади з досвідом зазвичай витрачають на монтаж таких сушарок не більше як місяць.
На сушарку встановлено два потокових вологоміри компанії Imko. Один вимірює вологість приблизно на половині висоти сушарки, другий — на виході. Система автоматичного керування у першу чергу керується показниками верхнього датчика, а нижній починає впливати на процес тільки в разі, коли показник вологості виходить за межі встановленого оператором діапазону. Корегування процесу сушіння відбувається шляхом зміни швидкості вивантаження.
Під час сушіння кукурудзи сушарку потрібно очищувати щонайменше раз на тиждень. Із соняшником варто перевіряти стан сушарки щодня і робити хоча б поверхневе очищення. У кожній зоні сушіння встановлено температурні датчики, які дають змогу контролювати стан зерна. Також усередині додатково встановлено 40 датчиків пожежної безпеки (вимірюють температуру відпрацьованого повітря в кожній секції сушарки) і централізовану систему пожежогасіння, яка заливає водою сушильну колону на трьох рівнях. Це значно зменшує пошкодження сушарки в разі займання зерна і цим самим заощаджує чималі кошти на ремонті.
На всіх вентиляторах установлено частотні перетворювачі, що дає змогу змінювати швидкість повітряного потоку. Наприклад, на ріпак потрібен менший повітряний потік, а на кукурудзу, навпаки — більший. Загалом частотні перетворювачі — недешеве задоволення, але вони сприяють економії електроенергії (до 20%) і забезпечують плавний пуск. Також це дозволяє економити на потужності дизель-генератора і на кабелях.
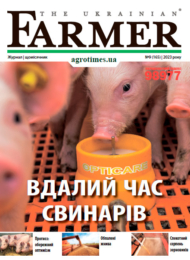