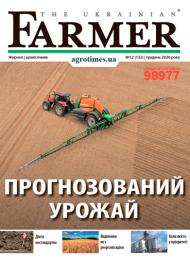
Досвід є обов’язковим складником будівництва будь-якого елеватора
Елеватор із досвідом
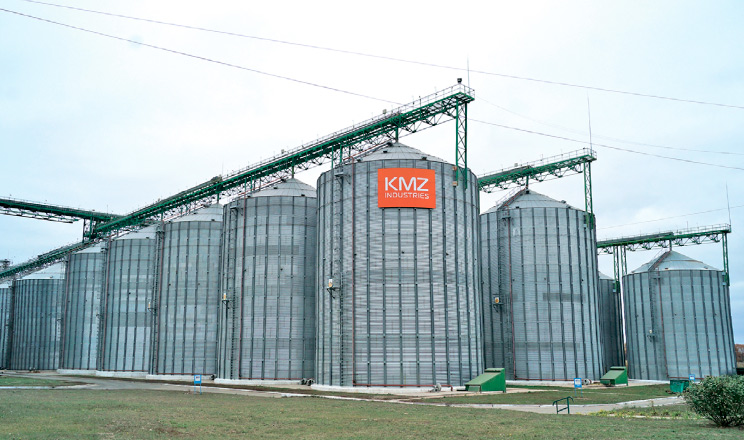
Досвід є обов’язковим складником будівництва будь-якого елеватора, але щоб його отримати, треба збудувати хоча б один об’єкт і кілька років його експлуатувати.
Першим елеватором агрогрупи «Агрейн» стало підприємство «Елеватор Агро» в с. Івківці, що під Прилуками. Його будівництво відбувалось у 2009–2010 роках, і, власне, тут компанія отримала перший досвід створення елеватора з нуля.
Потреба в будівництві власного елеватора виникла головним чином через економічні чинники. У цьому регіоні — найбільший підрозділ компанії «Агрікор Холдинг», у якого тільки сезонний вал кукурудзи сягає 300 тис. тонн. Ураховуючи, що регіон достатньо вологий, є потреба в сушінні зерна, а це, як відомо, одна з найбільших статей витрат. Віддавати десятки мільйонів гривень за сушіння, очищення та зберігання стороннім елеваторам не було жодного сенсу, тож вирішили будувати власне підприємство.
На сьогодні елеватор в Івківцях є одним із найбільших у Чернігівській області — він має потужність у 190 тис. тонн одночасного зберігання. Перша черга була на 100 тис. тонн, але практично за рік виникла потреба суттєво збільшити потужності. Змінилися пріоритети у вирощуваних культурах, кукурудза вийшла на перше місце, що потребувало збільшення потужностей майже вдвічі. Можна було будувати окремий елеватор, який би розташовувався ближче до земель компанії. Однак вирішили добудувати на цьому самому місці: територія дозволяла, залізничну гілку було прокладено, так само як і електрику й газ, і можна було суттєво заощадити на створенні інфраструктури. Потужність другої черги становила 90 тис. тонн. Окрім стаціонарних силосів елеватор має великий майданчик для зберігання зерна в рукавах, що потенційно збільшує його потужність ще на 100 тис. тонн.
Коли будували елеватор, ще не було їх розділення на маршрутні й інші. Однак ще на етапі вибору місця вирішили розташовувати підприємство поблизу великої залізничної станції. Потрібно було забезпечити оперативність відвантаження, що є ключовим чинником для успіху.
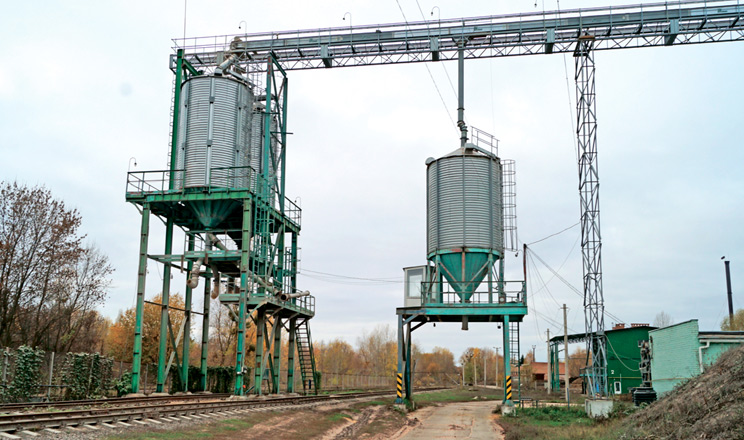
Будівництво
Проєктування першої черги виконувала компанія «Проєктконтрактсервіс», другої — ТОВ «НДПВІ Полтавагропроєкт». Коли обирали підрядника на будівельно-монтажні роботи, шукали компанії з досвідом. Загальні будівельні роботи виконувало підприємство ПП «Трансвіт», а монтаж технологічного обладнання — одеська компанія «ХайРейз Констракшн Холдинг». Вона будувала олійно-екстракційний завод у Миколаївській області для «Кернел», і такий досвід був однозначною перевагою.
Як для першого, так і для інших елеваторів, компанія дотримувалась таких принципів: серце елеватора (сушарка й очисні машини) — імпортні, все інше обирали за принципом доцільності. Оскільки цей елеватор був першим, тут встановили дві німецьких сушарки Petkus, але сепаратори вирішили обрати вітчизняні. Перші роки експлуатації показали, що сепаратори не завжди здатні забезпечувати стабільні показники за чистотою зерна, і тому через три роки від початку експлуатації тут встановили очисні машини Buhler.
Особливістю першої черги є велика кількість силосів різної місткості — їх тут 30, і це без урахування чотирьох хоперів тимчасового зберігання. Силоси обрали вітчизняні (КМЗ), і вони виявились нічим не гіршими за імпортні.
Транспортне обладнання встановили також українського виробництва (КМЗ і «Лубнимаш»). Продуктивність брали із запасом, щоб тільки можливості сушарки були обмежувальним чинником. Наприклад, на прийманні транспортери забезпечують 175 т/год, щоб зерно швидко доправити в проміжні хопери й далі на сушіння й очищення. Це дає змогу уникнути черг вантажівок біля елеватора — усі процеси з прийняття зерна відбуваються оперативно.
Другу чергу елеватора будували практично відразу за першою, але її створювали як повноцінний окремий елеватор, що буде спеціалізуватися на кукурудзі. Так на одній території з’явилося два елеватори, що мають спільну залізничну гілку.
Для другої черги основне обладнання обрали американського виробництва: потужні сушарки баштового типу Sukup, сепаратори — Dakota. Щоправда, згодом очищувальні машини також замінили на Buhler. Силоси й транспортне обладнання вирішили придбати теж американське, від компанії Brock. Збудували додаткову лінію приймання (ваговий пункт і дві завальних ями з авторозвантажувачами), а також пункт відвантаження в залізничні вагони.
Сьогодення й перспективи
На сьогодні елеватор щомісяця приймає по 100 тис. тонн зерна. Привозять збіжжя з підрозділів, що розташовані і близько, і доволі далеко — до 200 км. Також не відмовляються від кооперації з іншими агрохолдингами, використовуючи елеватори один одного задля зменшення логістичних витрат. Цього року через недовантаження елеваторів така схема не спрацювала: почалась агресивна цінова боротьба, що підштовхнуло багатьох гравців ринку звозити власне зерно тільки до своїх сховищ.
Ваговий комплекс об’єднано з лабораторією. Там відбувається документальний контроль, автоматичний пробовідбірник подає зразки безпосередньо до лабораторії, де спеціалісти за допомогою сучасного обладнання оперативно визначають усі параметри зерна. До повної автоматизації лабораторії ще не дійшли (це потребує інвестицій у 250–300 тисяч доларів), однак питання вже розглядається.
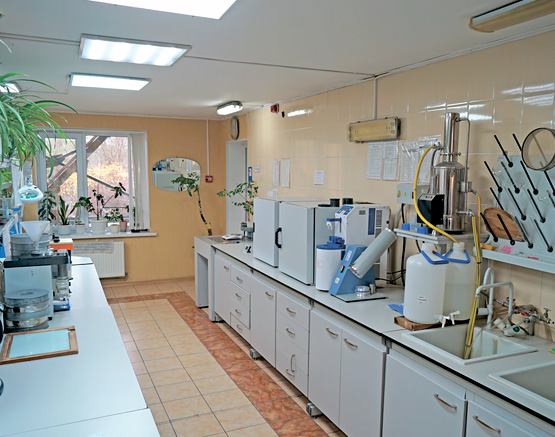
Вагові комплекси обладнано датчиками постановки автомобілів, що гарантує зважування тільки тоді, якщо повністю заїхати на ваги. Компанія «Ай Ті Гранд» саме впроваджує системи моніторингу, яка за допомогою відеоконтролю й зчитування номерних знаків оптимізує роботу ваговиків і лабораторії й на 15–20% пришвидшить приймання зерна. Це може сприяти збільшенню продуктивності елеватора, особливо коли зерно має низьку вологість і на сушіння витрачається менше часу. Відеоспостереження дасть змогу фіксувати переміщення транспорту територією елеватора, а також бачити вміст кузова. На момент будівництва такі системи не були широко розповсюджені, однак тепер це треба мати й користуватися цим.
Для контролю зерна в силосах встановлено систему термометрії. Залежно від діаметра й висоти силосів кількість кабелів і датчиків відрізняється. Система чітко показує температуру зерна по всьому об’єму силоса, що дозволяє запобігти будь-яким небажаним процесам.
Для автоматичного контролю кількості зерна в силосах буде застосовуватись аналітика «силосна дошка». Це дасть змогу чітко розуміти, на скільки заповнений силос, і відповідно до цього ухвалювати певні управлінські рішення. Наприклад, якщо є контракт на приймання кукурудзи на 60 тис. тонн протягом 15–20 днів, виникає потреба у вільних місткостях, і треба розуміти, у яких силосах скільки чого зберігається. Наприклад, коли в силосі на 5 тис. тонн зберігається всього 500 т соняшнику, можна його перевантажити в меншу місткість або стимулювати поклажодавця, щоб той продав або забрав зерно. Також розглядається питання про придбання ультразвукових датчиків, що контролюватимуть фактичний обсяг заповнення силосів.
Одним із головних кроків оптимізації цього року була закупівля газу в літній період, коли ціна була найнижчою. Відповідно, собівартість сушіння значно знижується, і це дає конкурентну перевагу перед іншими елеваторами навіть з урахуванням додаткових витрат на закачування на зберігання, саме зберігання та відбирання. Так усе одно вигідно, ніж купувати енергоносій в опалювальний сезон.
Приймання
Після того як лабораторія визначає якісні показники, зерно залежно від вологості й засмічення подається на одну з чотирьох приймальних ліній. Звідти — у проміжний бункер, а потім на попереднє очищення й сушіння. Оскільки сушарки першої черги у 4 рази менш продуктивні, ніж сушарки другої черги, тому першою чергою приймається сухіше зерно, другою — вологіше. Вивантаження з автотранспорту — заднє й бокове, одночасно можна приймати дві культури. Приймальний блок оснащено трьома авторозвантажувачами, а ще одна завальна яма приймає тільки самоскиди.
Усі лінії приймання мають паспортну потужність 175 т/год, але загальна потужність прив’язується до продуктивності сушарки. За вологості кукурудзи 23–25% підприємство може сушити до 5 тис. тонн на добу. За меншої вологості продуктивність може бути вищою. Цього року вологість кукурудзи на початку збирання становила 19–20%, а на середину листопада підвищилася до 24–25%. Проте середній показник приймання як був близько 4 тис. тонн на добу, таким і є.
Сушарки
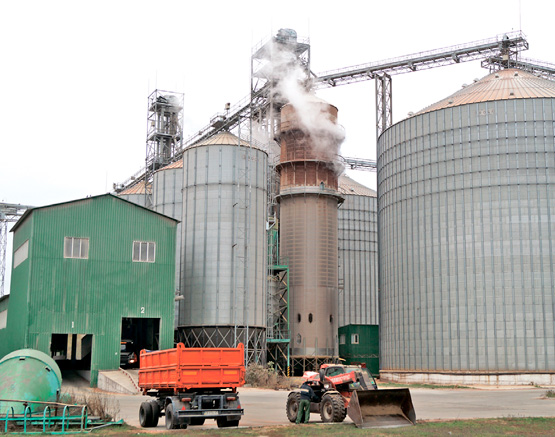
Коли починалося проєктування першої черги, частка кукурудзи була незначною, тому й обсяги сушіння планували не такими масштабними. Вибір шахтних сушарок Petkus продуктивністю по 500 т на добу на той момент здавався достатнім. Однак уже під час роботи над другою чергою пріоритети компанії змістились у бік кукурудзи — культури, що потребує інтенсивного сушіння. Тому тут установили значно продуктивніші баштові сушарки Sukup (2 шт.) із пальниками по 20 МВт. Продуктивність кожної сушарки — понад 100 т/год за умови зниження вологості з 20 до 14%. Загальна продуктивність цих двох сушарок може сягати 5 тис. тонн на добу. Середній показник витрат газу по елеватору під час сушіння кукурудзи — 1,3 м. на тонно-відсоток.
Сепаратори
Сьогодні для очищення зерна на обох чергах використовують сепаратори Buhler. Незважаючи на високу ціну, вони повністю виправдовують вкладені кошти. З ними підприємство не має проблем з якісними показниками зерна, очищення відбувається чітко до заданого рівня.
Вітчизняні сепаратори не змогли забезпечити стабільні показники, і їх замінили. Однак і відомий американський виробник теж не впорався із завданням. Його машини містили багато дерев’яних деталей, які з часом набирали вологу й ускладнювали налаштування. Якість очищення з часом перестала відповідати встановленим нормам, а ремонт вирішили не робити, бо з часом ситуація виникла б знову.
Для попереднього очищення використовують сепаратори КБС — ними відбирають грубу домішку перед сушінням.
Силоси
Унікальність елеватора в Івківцях полягає у його силосах. Тут установлено 34 (!) місткості — від 2 тис. до майже 20 тис. тонн. Це дає можливість окремо зберігати партії зерна різного класу. Навіть якщо клієнт хоче зберігати своє зерно уособлено (наприклад, 3–5 тис. тонн), тут є така можливість.
Переважна більшість силосів — українського виробництва, від компанії КМЗ. За словами директора елеватора Сергія Назарова вони нічим не поступаються імпортним, дешевші, і до того ж можна отримати державну компенсацію. Тільки на другій черзі елеватора встановлено чотири великих силоси по 20 тис. тонн американського виробника Brock. Таке рішення було ухвалено через те, що сушарки й очищувальні машини із самого початку планували також американського виробництва, тож вирішили, що друга черга буде повністю американська. Усі силоси оснащено системою аерації й верхньої вентиляції, що дає можливість підтримувати зерно в оптимальному стані за вологістю та температурою.
Для тимчасового зберігання вологого зерна використовують чотири хопери по 500 т на першій черзі й чотири хопери по 1 тис. тонн — на другій. Тобто загальний обсяг тимчасового зберігання становить 6 тис. тонн. Усі місткості оснащено вентиляторами, що дає змогу вирівнювати вологість зерна перед відправленням на первинне очищення та сушіння.
ГОВОРИТЬ ЕКСПЕРТ
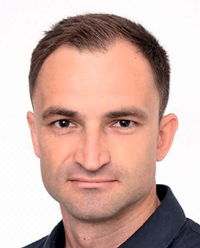
Віталій Штемпель, фінансовий директор «Агрейн»
— Коли ми вибирали обладнання, то вирішили піти таким шляхом: там, де потрібна якість — обирали лідерів ринку. Там, де потрібна продуктивність, обирали вітчизняного виробника. За власним досвідом транспортне обладнання й силоси українського виробництва нічим не гірші за імпортні, але коштують менше і в експлуатації питань не виникає.
Сушарки обирали з рекуперацією, щоб зменшити витрати газу. В Україні середні витрати на зняття одного тонно-відсотка вологи становлять 1,7–2,2 кубометра газу, нам удалося досягти показника в 1,3 кубометра газу на тонно-відсоток.
Досить корисний досвід отримали із сепараторами: після того як відомий американський виробник не зміг запропонувати машину, яка б вона нас влаштовувала, ми зрозуміли, що наші вимоги задовольнить тільки лідер — компанія Buhler.
На відвантаженні крім дефіциту вагонів ми стикнулись із надто повільною логістикою між станцією «Прилуки» й елеватором (відстань близько 12 км). Щоб позбутися цієї проблеми, довелося посприяти збільшенню класності самої станції, що дало змогу пришвидшити рух вагонів між станцією й елеватором.
Під час будівництва першої черги було зроблено всього один комплекс із відвантаження. Уже через рік після початку експлуатації збудували ще один «відпуск», що значно пришвидшило завантаження вагонів.
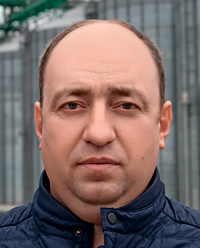
Сергій Назаров, директор ТОВ «Елеватор Агро»
— Ураховуючи, що підприємство працює далеко не перший рік, виникла потреба в модернізації та реконструкції обладнання й навіть цілих технологічних схем. Наприклад, збільшили фронти подачі вагонів — із 8 + 8 до 9 + 9, а в перспективі збільшити до 9 + 11 вагонів. Таким чином, замість одночасної подачі 16 вагонів можна буде подавати 20. Крім того, ремонтується під’їзна колія, що дасть змогу значно пришвидшити рух вагонів між елеватором і станцією. Також планується збільшити продуктивність однієї з двох транспортних ліній, щоб пришвидшити процес завантаження вагонів. Якщо говорити про тогорічну швидкість завантаження вагонів, у середньому витрачалось 65 хв на один вагон. Тепер цей показник зменшився до 40 хв.
Серед останніх робіт із модернізації елеваторного обладнання слід згадати відновлення системи термометрії, заміну самопливів, зменшення швидкості руху зерна самопливами для уникнення його пошкодження. Триває робота з оптимізації маршрутів. Усе це вже дало результат у вигляді меншої кількості битого зерна. Також удосконалюється система автоматизації шляхом поступової заміни окремих блоків. Це збільшить загальну ефективність підприємства і полегшить його експлуатацію. Наприклад, можна буде вести облік мото-годин обладнання й раціональніше планувати сервісні роботи.
За десять років експлуатації транспортне обладнання перевантажило більше як 2 млн тонн. І тільки тепер виникла потреба в заміні ланцюгів. Наразі замінили 600 м, і планується до заміни ще 1200 м. Перед цим замінили напрямні.
Найближчим часом планується об’єднати першу і другу черги елеватора транспортним обладнанням, що дасть змогу ефективніше використовувати силоси і зменшувати логістику зерна всередині підприємства. Це також важливо в періоди, коли елеватор одночасно приймає кілька різних культур.
Володимир Огійчук
журнал The Ukrainian Farmer, грудень 2020 року
Усі авторські права на інформацію розміщену у журналі The Ukrainian Farmer та інтернет–сторінці журналу за адресою https://agrotimes.ua/ належать виключно видавничому дому «АГП Медіа» та авторам публікацій, згідно Закону України “Про авторське право та суміжні права”.
Використання інформації дозволяється тільки після отримання письмової згоди від видавничого дому «АГП Медіа».
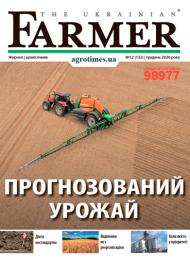