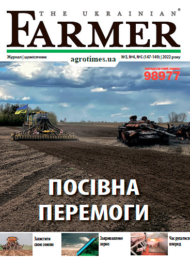
Незалежність від газу цього року набуває неабиякого сенсу як через війну, так і через вартість
Актуальна економія
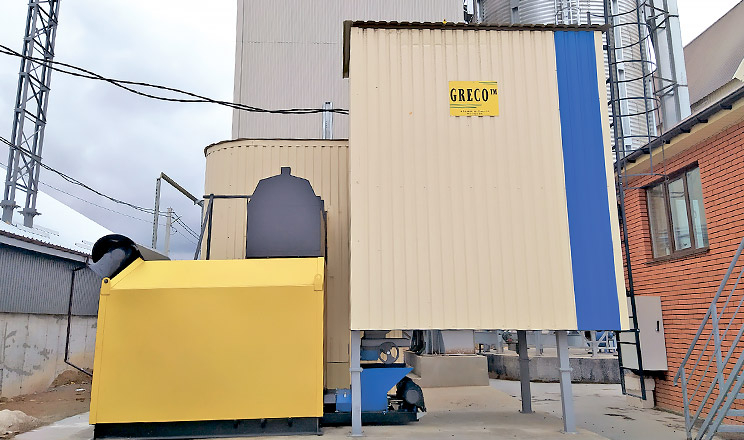
Незалежність від газу цього року набуває неабиякого сенсу як через війну, так і через вартість.
Хоч нині й весна, але подумки більшість аграріїв уже перемістились до осіннього сезону збирання. Думають про своє і про глобальне: якою буде ціна на зерно, чи буде достатньо пального, коли закінчиться війна… — усе це не дає зосередитись і нормально планувати діяльність хоч на пів року чи рік. Серед інших досить важливим є підхід до сушіння зерна. Нині важко прогнозувати, що буде з газом, і навіть не ціна є потенційною загрозою, а сама наявність блакитного палива у достатній для промислового використання цілей. Однак навіть те, що дешевим цей енергоресурс у найближчій та й віддаленій перспективі точно не буде, змушує замислитись про пошук альтернативи.
Доволі цікавим є досвід агрофірми «Ольгопіль», яка із самого початку навчалася обходитись без «труби». Незважаючи на розташування (південний схід Вінницької області), підприємство має доволі значну потребу в сушінні зерна. Сушать кукурудзу, ріпак, соняшник, сою, іноді пшеницю.
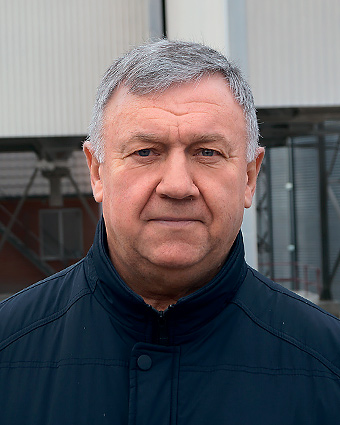
Власник підприємства Павло Каленич розповів, що в кожному з трьох відділків працюють сушарки (дві Bonfanti й одна FEERUM) продуктивністю 700, 500 і 400 т на добу. Кожну з них оснащено твердопаливним теплогенератором українського виробника «Греко Груп». Однак до цього було пройдено шлях від застосування солярки й скрапленого газу. Ці види палива були доступними, і на цьому їх переваги закінчувались. Вартість сушіння була надто високою, щоб забезпечити належні економічні показники, і власник почав шукати варіанти. Направду вибір був не дуже великим, бо тільки твердопаливні теплогенератори могли забезпечити бажану собівартість сушіння. Залишилось обрати теплогенератор і шахтну сушарку та пов’язати роботу обох пристроїв. На той час (5 років тому) великого досвіду застосування твердопаливних теплогенераторів в Україні було не так багато, і Павло Каленич розв’язував досить цікаву технічну й організаційну задачу.
Обравши сушарку італійського виробника Bonfanti, було вирішено оснастити її вітчизняним теплогенератором від «Греко Груп». Для Bonfanti це взагалі перший досвід такого симбіозу в Україні, бо раніше усі моделі сушарок тут працювали тільки на газу. Проте жодних труднощів поєднання з твердопаливним теплогенератором не викликало. Українські спеціалісти швидко змонтували обладнання й налаштували його. Персонал пройшов навчання і досить швидко опанував усі особливості експлуатації сушарки разом із твердопаливним теплогенератором.
Як паливо тут використовують пелети із соняшникової лузги. Власний соняшник відвозять до олієекстракційного заводу, а назад везуть пелети. Так отримують паливо за мінімальною вартістю та ще й економлять на логістиці.
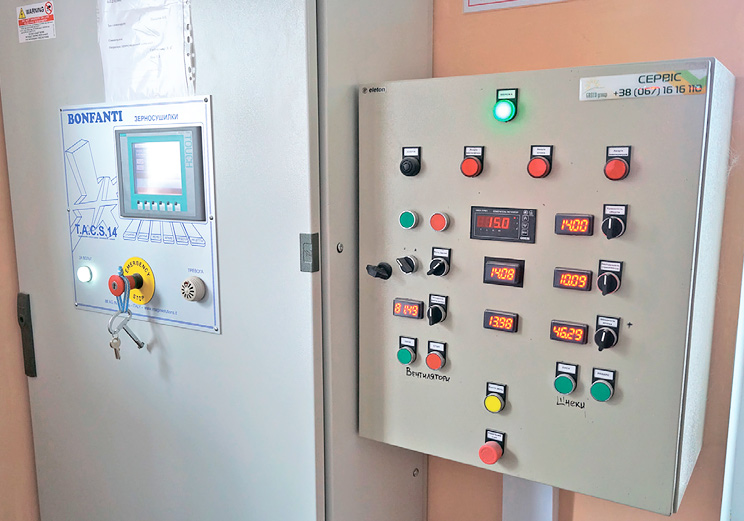
За словами власника підприємства, вартість сушіння на твердому паливі завжди була низькою. Звісно, у часи, коли ціна природного газу була невисокою, ті елеватори, що були приєднані до газової мережі, не знали проблем і демонстрували навіть кращу економію. Проте такі часи тривали недовго, і минулого сезону підприємство у повному обсязі відчуло економічний ефект від твердопаливного теплогенератора. Це не лише свобода від газової залежності та диктатури розподільчих мереж — це досить великі гроші, які могли бути спаленими в сушарках.
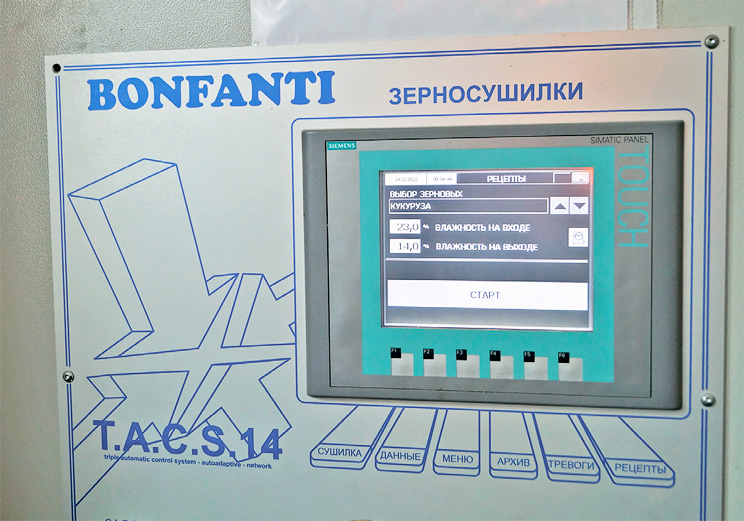
Порівняти витрати на паливо досить просто: ціна 2,5 кг пелет, що витрачають на зняття тонно-відсотка вологості, — близько 15 грн за умови ціни 6 грн/ кг. Якщо ж сушити газом, доведеться витратити щонайменше 35–45 грн. Ураховуючи, що агрофірмі «Ольгопіль» вдалось придбати пелети по 3 грн/кг, за сезон заощадили мільйони гривень.
Пелети зберігають насипом і у біг-бегах. Коли працює сушарка, пелети 1–2 рази на тиждень завантажують у проміжний 20-тонний бункер, звідки транспортер подає їх у витратний бункер теплогенератора. Щоб оператор не відривався на процес подачі палива, у витратному бункері встановлено датчик наповнення: як тільки кількість пелет доходить до встановленого рівня, транспортер вимикається. Оператор за допомогою камер тільки контролює наявність палива у витратному бункері. Безпосередньо до камери згоряння пелети подають два шнеки. Швидкість їх обертання встановлює автоматика теплогенератора залежно від потрібної температури теплоносія.
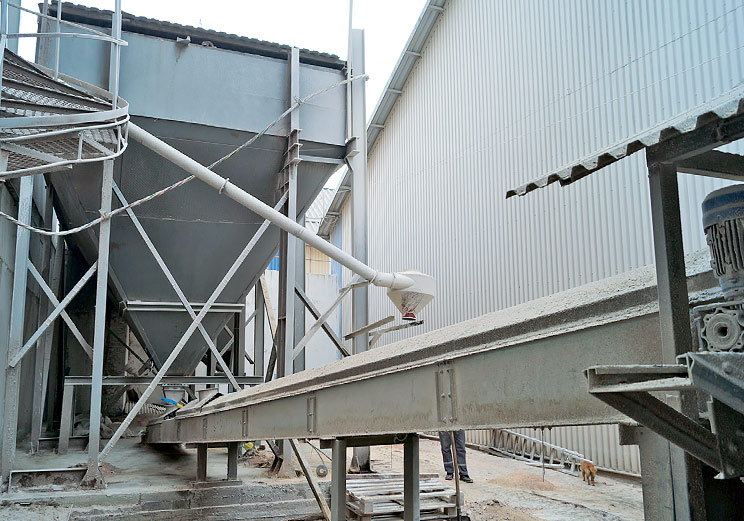
За словами оператора Івана Попа, щороку проводять обов’язкове технічне обслуговування теплогенератора: ретельно готують до наступного сезону сушіння, а за потреби проводять й оперативну сервісну підтримку саме під час сушіння, бо на вагу кожна годи на. Раз на 1–2 тижні очищають камеру згоряння від золи. Ці роботи виконують під час планової зупинки сушарки на очищення. Коли працюють із кукурудзою, сушарку чистять раз на 3–4 дні. Очищення всередині сушарки триває не більше як 2 год, до того ж всередині одночасно працюють три людини. Такий підхід дає змогу уникати проблем і бути впевненим, що жодних несподіванок не станеться.
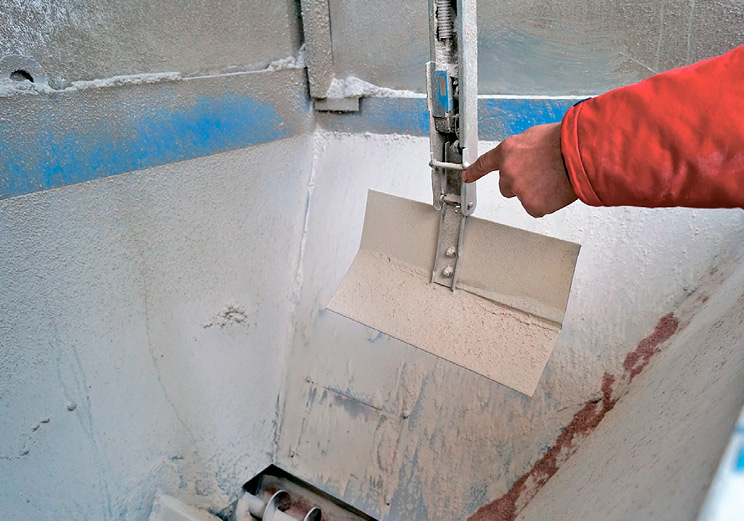
У підрозділі підприємства, що в с. Мельниківці Немирівського району, торік було побудовано новий сушильний комплекс. Ураховуючи успішний досвід, власник знову обрав сушарку Bonfanti з теплогенератором від «Греко Груп». Щойно завершили пусконалагоджувальні роботи, довелося сушити 11 тис. тонн кукурудзи. Так об’єкт пройшов випробування й готовий до подальшої роботи.
Механік Юрій Полянський розповів, що в сушарку одночасно вміщується близько 60 т, а середня добова продуктивність становить 500 т. Усе залежить від початкової вологості зерна. Також він додав, що в процесі сушіння бере активну участь лабораторія, яка контролює вологість зерна на виході. Якщо є відхилення, час сушіння змінюють. Лабораторія також вимірює й вхідну вологість, і цей показник заносять до комп’ютера сушарки. Той, залежно від програми сушіння, розраховує алгоритм роботи.
ГОВОРЯТЬ ЕКСПЕРТИ
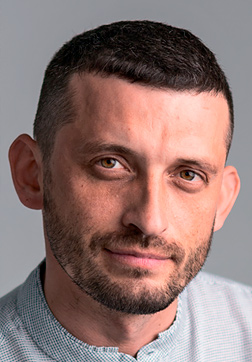
Іван Корженко, директор ТОВ «Греко Груп»
— В агрофірмі «Ольгопіль» один із наших теплогенераторів працює вже 5 років. Ми вдячні Павлу Каленичу, що довірився першим в Україні переобладнати одну з найскладніших сушарок, а саме Bonfanti L 150CE. Після успішного переобладнання цього об’єкта, ми переобладнали 247 об’єктів, з них більше як 80 сушарок Bonfanti максимальної потужності 20 МВт. Він продемонстрував хорошу стабільну роботу й далі успішно працює. Підприємство щороку викликає наших сервісних спеціалістів, які виконують обслуговування обладнання, і це дає змогу працювати протягом сезону, не зупиняючись. Позитивний досвід став результатом того, що у двох інших підрозділах компанії було також установлено сушарки з теплогенераторами від «Греко Груп».
На сьогодні ми оновили модельний ряд теплогенераторів, розширили виробничу базу і далі виконуємо замовлення в найкоротші строки. Тож українські аграрії мають змогу в умовах війни оперативно розв’язати проблему сушіння зерна.
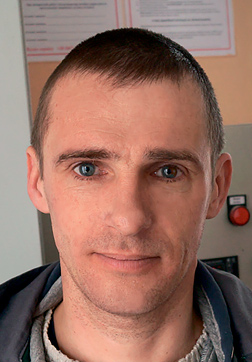
Іван Поп, оператор сушильного комплексу
— Стара сушарка італійського виробництва працювала на солярці й за добу «споживала» близько 1000–1200 л пального. Сушила максимум 300 т на добу. Яка тут могла бути економія? До того ж для наших обсягів бракувало продуктивності сушіння.
Тому було придбано потужнішу сушарку Bonfanti й твердопаливний теплогенератор від «Греко Груп»
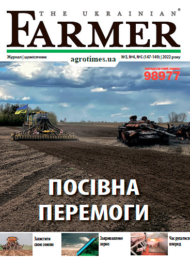