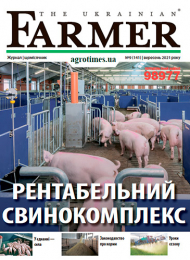
Надійне обладнання елеватора ТОВ «Фарвуд» допомогло в багатьох ситуаціях
Розрахувати власні сили
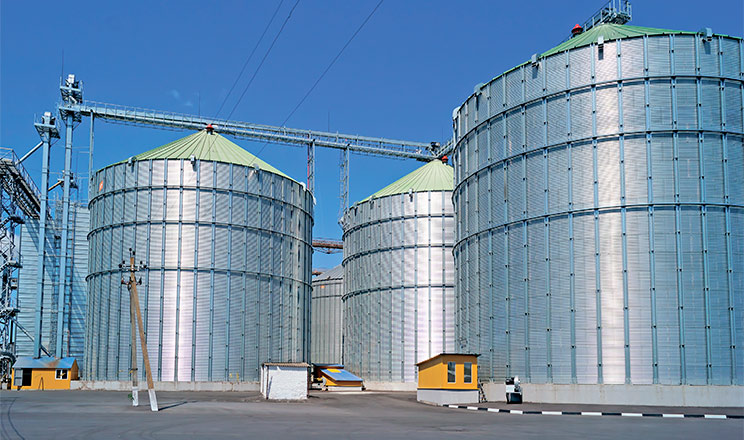
Досвід будівництва елеваторів і вибору обладнання показує, що ключовими аспектами є надійність обладнання і економічна ефективність технологічних процесів.
Вдалий старт
Коли створюють новий елеватор, є багато моментів, які неможливо передбачити навіть найдетальнішим контрактом. Тож, приїжджаючи на новий об’єкт, завжди чекаєш почути щось цікаве — будь-який досвід може допомогти тим, хто ще не торкався цієї справи й не може об’єктивно оцінити власні потреби та можливості.
Схожа ситуація відбувалась із будівництвом елеватора ТОВ «Фарвуд» в с. Оратів, що на Вінниччині. Будівництво першої черги розпочинали, не маючи досвіду, проте розуміння власних можливостей не дало наробити помилок. Обрали перевіреного підрядника й обладнання відомого американського виробника GSI. Можливо, це було не найдешевше рішення, однак за ці гроші було придбано не лише відомий бренд, а ще й надійність і довговічність. Для перших років роботи й відсутності досвіду в персоналу надійне обладнання допомагало в багатьох ситуаціях.
Перша черга будувалась із залученням обладнання американського виробника. Було зведено два хопери по 500 т, баштову сушарку і три силоси по 2 тис. тонн і 2 силоси по 5 тис. тонн. Норії та ланцюгові транспортери також узяли від цього виробника, щоб не ускладнювати логістику й отримати високий рівень якості усього комплексу.
Будівництво першої черги завершилось 2010 року, і відтоді це обладнання чітко працює. Очисне обладнання обрали вітчизняне — було встановлено сепаратор БСХ-100 і скальператор, проте основну роботу виконує саме БСХ-100. Коли працювала тільки перша черга, продуктивності цієї машини вистачало, однак тепер, коли введи в експлуатацію другу чергу, виникла потреба в збільшенні продуктивності очищення. Наразі керівництво розглядає варіанти заміни очисного обладнання на сучасніше і продуктивніше.
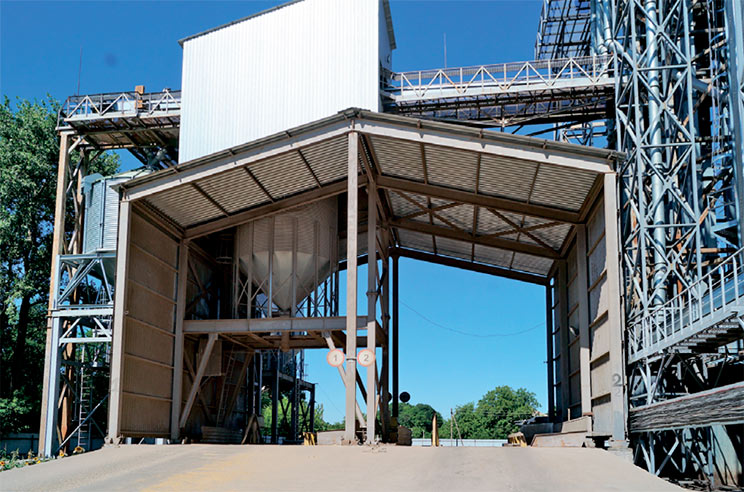
Під час будівництва першої черги було відразу змонтовано блок автомобільного і залізничного відвантаження. Автомобілі завантажуються на одній із завальних ям — безпосередньо над нею було встановлено проміжний бункер на 78 т. Пункт залізничного відвантаження був розрахований на роботу з одним вагоном.
Збільшення обсягів перевалювання та зберігання спонукало власників до будівництва другої черги. До того ж це стосувалось не тільки силосів і транспортного обладнання. Збудували ще одну сушарку і збільшили вдвічі потужність залізничного відвантаження. Будівництво розпочали у 2019 році, а в сезон 2020-го працювали з новими потужностями. Будівельний підрядник був той самий, а от обладнання вирішили придбати в польського виробника FEERUM, який виграв тендер і зобов’язався поставити один 500-тонний хопер, шахтну сушарку продуктивністю 500 т/добу і три силоси по 8000 т, збільшивши таким чином обсяг одночасного зберігання до 40 тис. тонн. Це збільшило річний обсяг перевалювання до 80 тис. тонн. Крім того, було вирішено про добудову транспортних ліній, щоб покращити швидкість відвантаження й зробити можливим одночасну роботу з кількома культурами. Подвоїли потужність залізничного відвантаження, встановивши ще дві проміжні місткості по 78 т. Це дало змогу відвантажувати по 10–12 вагонів на добу.
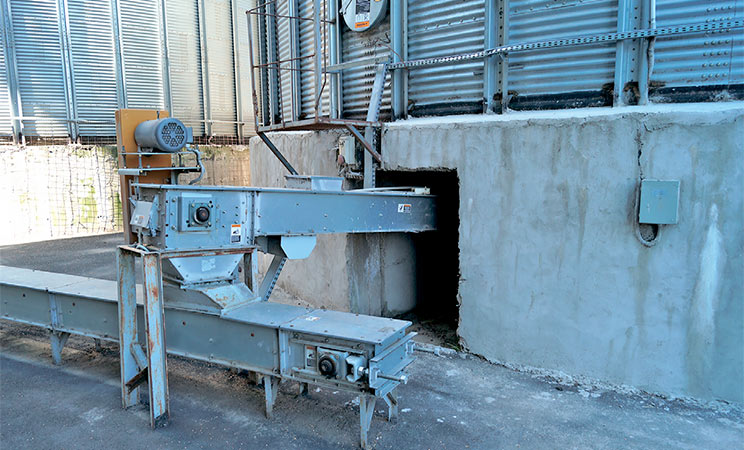
Звичайна робота
Кожен елеватор розпочинається з лабораторії та вагової. Тут усе як усюди: двоє ваг, пробовідбірник, лабораторія із сучасним обладнанням. Після визначення всіх параметрів автомобілі розвантажуються на двох завальних ямах. За потреби тут може застосовуватися бічне автовивантаження. Після цього зерно спрямовують на попереднє очищення й далі — на тимчасове зберігання до одного із хоперів. Наступним етапом є сушіння або переміщення до основних силосів. Переважну більшість зерна відвантажує залізничний транспорт, тож цілком зрозумілим кроком було збільшення продуктивності саме цієї ділянки під час будівництва другої черги.
Керування елеватором здійснюється з операторської. Тут установлено три монітори, два з яких відповідають за обладнання першої черги, третього вистачає для обладнання другої черги. Окремий «ящик» передбачено для керування теплогенератором: на ньому встановлено всього десяток кнопок, тож розібратись у його роботі зможе навіть недосвідчений оператор.
Транспортне обладнання складається переважно з ланцюгових транспортерів, норій і самопливів. Тільки під силосами FEERUM для вивантаження зерна застосовують стрічкові транспортери. Унаслідок цього зменшуються експлуатаційні витрати, і зерно практично не пошкоджується.
До зберігання — особливі вимоги
Підприємство працює з такими культурами: ріпаком, пшеницею, ячменем, соєю, кукурудзою та соняшником. Тож сезон розпочинається рано і триває аж до відвантаження останніх тонн збіжжя. До того ж кожна культура вимагає особливого ставлення, і лабораторія змушена ретельно контролювати стан зерна і параметри зберігання.
Силоси першої черги будували на високих фундаментах, завдяки цьому обійшлися без підземних галерей. Системи вивантаження розташовуються над поверхнею землі, що певною мірою спрощує їх експлуатацію. Три нових силоси FEERUM по 8000 т зробили на низьких фундаментах із підземними галереями. Для вивантаження зерна тут застосовують стрічкові транспортери. Самі силоси оснащено зачисними шнеками й кабельною термометрією.
Дах польських силосів вкрито полімером (зеленого кольору), що дає кілька важливих переваг: покращується захист від корозії, полегшується сходження снігу і найголовніше — зменшується нагрівання зони над зерном. Це особливо важливо для зберігання олійних культур, які є досить чутливими до перегріву. Та й інші культури зберігаються у стабільніших умовах.
Усі силоси оснащено кабельною термометрією. Як тільки лабораторія бачить підвищення температури, одразу вмикають аераційні вентилятори. Їх установлено по два на кожен силос.

Сушити економно
Першою сушаркою підприємства стала баштова модель GSI продуктивністю до 500 т на добу. Вона забезпечувала якісне сушіння зерна, і продуктивність її також не викликало зауважень. Однак витрати газу не вдавалося зменшити до прийнятного рівня. Щорічні витрати на блакитне пальне становило 7–8 млн гривень. Тому, коли обирали сушарку для другої черги, зупинилися на шахтній моделі FEERUM FTD 4/28 продуктивністю 500 т на добу.
Коли ж постало питання приєднання сушарки, з’ясувалося, що потужності місцевої газової мережі бракує, щоб «наситити» два потужних споживачі. Намагалися домовитись із газовиками, щоб ті дозволили вмикати сушарки тільки по черзі, але марно. Тоді почали розглядати альтернативне пальне, і врешті-решт перевели сушарку FEERUM на роботу з твердопаливним котлом, що працює на пелетах. Теплогенератор придбали в компанії Greco Group, яка виготовила обладнання з урахуванням усіх місцевих вимог, виконала монтаж і ввела в експлуатацію.
Спочатку ідея роботи з твердопаливним котлом не викликала ентузіазму в керівництва, бо була певна недовіра до стабільності температури сушильного агента та якості самого сушіння. Однак усе змінилося, коли почали сушити перші партії зерна. З’ясувалося, що вартість сушіння в сушарці FEERUM із теплогенератором на пелетах є меншою у 7–8 разів, ніж у баштовій сушарці GSI. Тобто якщо газу раніше спалювали на 70–80 тис. гривень на добу, то пелет витрачали всього на 10–12 тис. До того ж продуктивність обох сушарок була практично однаковою. Одразу змінився вектор роботи: минулого сезону працювала тільки шахтна сушарка FEERUM. Баштову сушарку GSI вмикали всього на один день, коли треба було терміново довести до кондиції партію зерна. На кінець сезону було вирішено перевести й баштову сушарку на пелети, щоб суттєво скоротити витрати й запропонувати клієнтам кращі умови на сушіння. Однак газове обладнання залишать, щоб у разі відсутності пелет або зменшення цін на блакитне пальне можна було обирати вигідніший варіант.
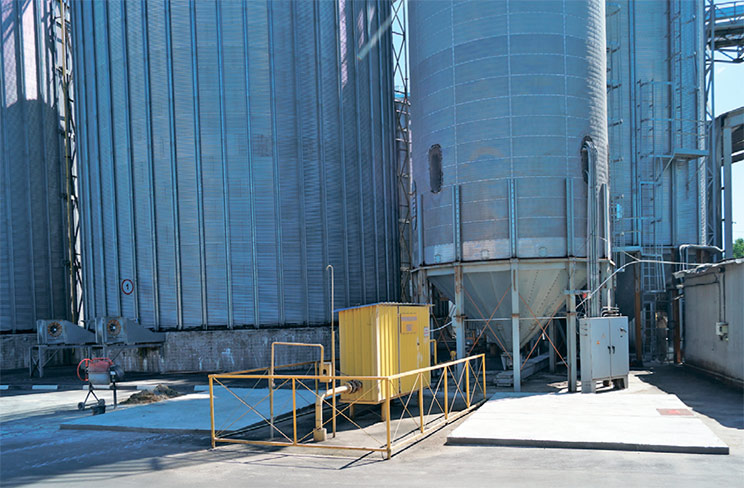
Баштову сушарку чистять тричі за сезон, шахтну доводиться чистити раз на три дні. Це треба робити як із міркувань безпеки й ефективності, так і з погляду коректної роботи. Коли температурні датчики забруднюються, вони починають показувати неправильні дані, й, відповідно, автоматика або оператор установлюють невідповідні параметри сушіння. Тому кожен четвертий день роботи доводиться витрачати кілька годин на профілактичні заходи. З іншого боку, є впевненість, що всередині все нормально, і не варто очікувати неприємних несподіванок.
Неоціненний досвід
Під час монтажу обладнання першої черги кабельні мережі розмістили в горизонтальних коробах. Це було невдале рішення, бо за 10 років сніг, що падав із дахів силосів, у багатьох місцях пошкодив конструкцію кабельних каналів. Крім того, таке розташування кабелів сприяє затриманню там зерна та зернових решток, що привертають увагу гризунів — головного ворога кабельних мереж. Проблема виявилася такою серйозною, що найближчим часом планується розпочати заміну кабелів обладнання першої черги, а самі канали зроблять вертикальними. До речі, другу чергу елеватора будували вже з урахуванням негативного досвіду, і «свіжі» кабельні канали мають вертикальну структуру, без нашарувань і закритих ділянок.
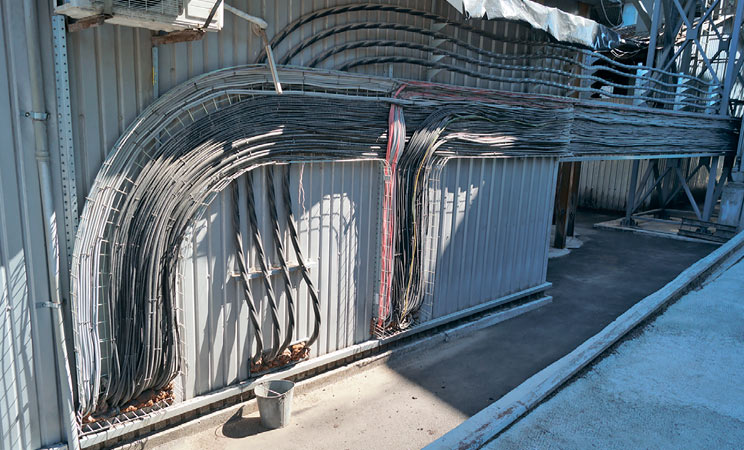
На початку експлуатації пошкодили норійну стрічку GSI. Тут жодних претензій до виробника і монтажної організації — ситуація сталася через форс-мажорні обставини й відсутність досвіду.
Експлуатація показала необхідність футерування коробів із ланцюговими транспортерами. Вони досить швидко зношуються, тож бажано їх захищати із середини полімерними матеріалами або застосовувати зносостійкий метал.
Ще одна помилка «вилізла» через вісім років експлуатації — в одному із силосів просіла центральна частина фундаменту. Причину назвати важко — чи то помилка проєктантів, чи незадовільна якість матеріалів… Довелося ремонтувати, і на сьогодні силос функціонує у штатному режимі.
ГОВОРЯТЬ ЕКСПЕРТИ
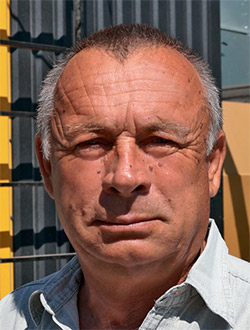
Василь Мельник, інженер-будівельник
— Будівельними підрядниками є компанії «Мур» і «Агрікон Південь». Роботи виконували вчасно. Не можу сказати, що абсолютно все будівництво відбувалося без зауважень — такого просто не буває. Однак питання виникали через певні прорахунки в проєктах. Наприклад, коли добудовували точку залізничного відвантаження, її розмістили надто близько до наявної, і це створювало труднощі для одночасного завантаження двох вагонів. Довелося зміщувати її на кілька метрів, щоб виправити ситуацію. З цим впорались без проблем, і тепер працюємо значно ефективніше. У нас невелика територія, й тільки одна залізнична гілка, на якій уміщується до 12 вагонів. Це відповідає добовій можливості залізничного відвантаження. У межах території вагони переміщує лебідка, а між елеватором і станцією — тепловоз Укрзалізниці.
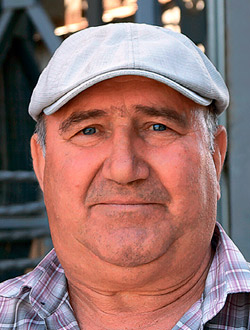
Валерій Ющенко, головний інженер
— Кожне будівництво тягне за собою купу питань, які неможливо врахувати в проєктування. Навіть будуючи на власній ділянці гараж, вилізуть помилки або недоліки. Тут головне, щоб усе вчасно побачити й виправити. На сьогодні елеватор складається здебільшого з обладнання американського (GSI) і польського (FEERUM) виробників. Американське відпрацювало 10 років, і можна сказати, що жодних серйозних питань до нього не виникало.
Досить високий рівень надійності й витривалості дозволив безперебійно відпрацювати багато сезонів поспіль. До того ж експлуатаційні витрати були відносно незначними. Недоліком цього обладнання можу назвати досить високу стартову вартість і відсутність запчастин в оперативному доступі. Коли доводиться чекати тиждень і більше якусь важливу деталь, це, м’яко кажучи, не зручно, особливо під час інтенсивної роботи впродовж сезону.
Польське обладнання відпрацювало всього сезон, тому поки що рано говорити про його витривалість. Проте адаптація до обладнання відбулася нормально, об’єкт працює у штатному режимі.
Хочу сказати про використання стрічкових транспортерів у нижніх галереях під польськими силосами — вони потребують значно менше потужності й водночас не пошкоджують зерно.
Василь Грабар, головний інженер компанії Greco Group
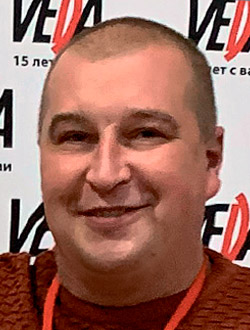
— Наша співпраця з компанією «Фарвуд» розпочалася, коли в них виникли труднощі з при єднанням другої сушар ки — замало було тиску в газовій магістралі. Оскільки нашим обладнанням користується багато сусідніх підприємств, представники «Фарвуд» звернулися до нас із проханням допомогти оперативно вирішити ситуацію. У результаті менше ніж за місяць ми виготовили й установили теплогенератор потужністю 7 МВт, який уже відпрацював один сезон і приніс власникам суттєву економію. Витрати на сушіння скоротились щонайменше у 4–5 разів, і практично все зерно сушилось на сушарці FEERUM із теплогенератором Greco Group. Таким чином, було досягнуто практично повну незалежність від постачання газу, і наступного року власники елеватора планують установити ще один теплогенератор для баштової сушарки, щоб збільшити продуктивність підприємства в пікові періоди збирання кукурудзи. Газ лишиться тільки як альтернативне джерело енергії.
Теплогенератор потребує приєднання 6,5 кВт електроенергії. Ураховуючи, що газовий пальник відповідної потужності має потребу близько 5 кВт, то різниця в 1,5 кВт для такого об’єкта є непомітною. Обладнання повністю автоматизоване, температура теплоносія регулюється подаванням пелет. Запасу пального в оперативній місткості вистачає на 1,5–2,5 доби залежно від режиму сушіння. Оператор сушарки одночасно стежить і за роботою теплогенератора, тож немає потреби наймати додаткового працівника.
Завдяки тому, що піролізний газ допалюється в 4–5 етапів, на виході з теплогенератора не лишається сажі й інших шкідливих домішок і речовин із неприємними запахами. Зерно після сушіння відповідає всім нормам, що підтверджується лабораторними дослідженнями та багаторічним досвідом.
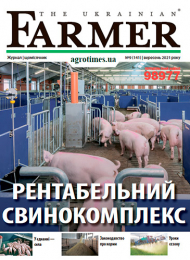