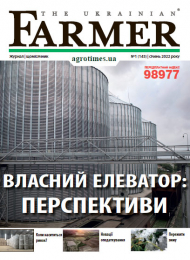
Початкові проєкти елеваторів не завжди передбачають розвиток підприємства, що ускладнює їхню модернізацію в майбутньому
Отримати максимум від «лінійника»
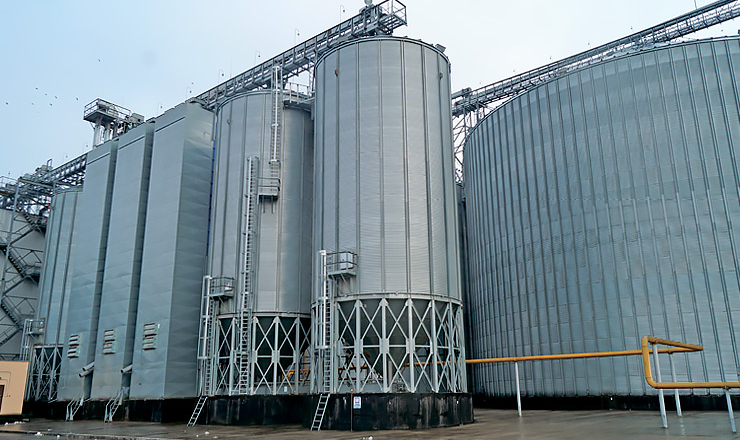
Початкові проєкти елеваторів не завжди передбачають розвиток підприємства, що ускладнює їхню модернізацію в майбутньому
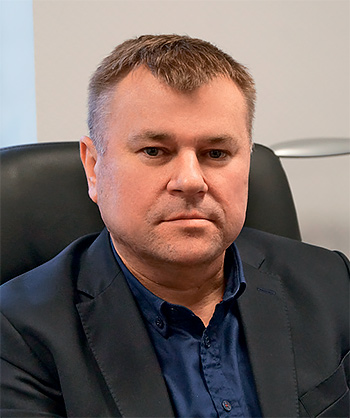
Ямпільський елеватор філії «Рідний край» ПрАТ «Зернопродукт МХП» є найбільшим лінійним елеватором компанії. Його потужність одночасного зберігання становить 75 тис. тонн, і це не враховуючи рукавного зберігання на 50 тис. тонн. Підприємство будували для забезпечення місцевого агровиробничого кластера потужностями для доробки й зберігання різних видів культур. Безпосередньо будівництво розпочалось у кінці 2012 року.
Планом було передбачено — створити елеватор із двома лініями приймання по 100 т/год кожна. Загальна потужність одночасного зберігання передбачалась в об’ємі 105 тис. кубічних метрів. Цей план був реалізований, і у 2013 році розпочали експлуатацію: пусконалагоджувальні роботи проводили на ранніх культурах, а повноцінне приймання розпочали на пізній групі.
У перший сезон прийняли близько 50 тис. тонн кукурудзи — саме таке завдання було поставлено перед підприємством. З наступного року елеватор перейшов на повноцінну цілорічну роботу з власним зерном, яке привозили з полів філії «Рідний край» ПрАТ «Зернопродукт МХП». На сьогодні підприємство приймає п’ять культур: озиму пшеницю, ріпак, кукурудзу, соняшник і сою. Окрім того, закуповує зерно від місцевих господарств для власних потреб компанії, а саме — для виробництва комбікормів. Спочатку купували соняшник і сою, а тепер до цього переліку додали кукурудзу. Загальний річний вал зерна різних культур становить 200 тис. тонн, що дорівнює 2,7 обороту елеватора. Близько 85% культур експортують, і тільки соняшник і сою спрямовують до власних переробних підприємств.
Мінімум часу на приймання
На ваговому комплексі працюють пневматичні пробовідбірники Rakoraf. Проте їх хочуть перемістити на треті автомобільні ваги, які встановили цьогоріч для збільшення пропускної здатності підприємства, а замість них на основних двох лініях планують використовувати автоматизований рейковий пробовідбірник компанії STORK. Лабораторія робить аналізи максимально швидко, для цього її повністю оснастили сучасним обладнанням.
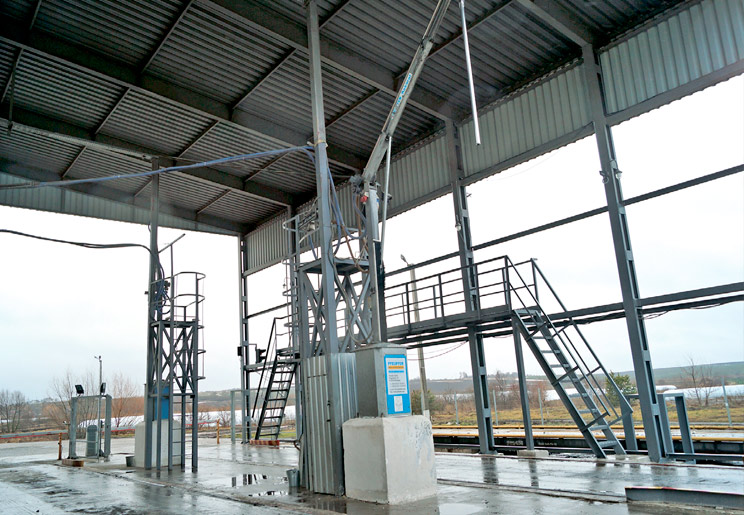
Продуктивність очищення — вузьке місце
За роки експлуатації було виявлено, що продуктивність очищення не завжди відповідає заявленим цифрам. Це спостерігається за роботи з ріпаком і соняшником зі значним умістом сміття, а також за очищення кукурудзи з вологістю 30% і більше. Подібні особливості машин не були враховані в проєктуванні, тому підприємство має хорошу продуктивність приймання на зерновій групі, а на олійній — не завжди. Добудова третьої лінії частково усунула проблему, але все одно в майбутньому очисні машини замінять на продуктивніші.
Головний інструмент елеватора
На кожній із двох ліній приймання було встановлено по три сушарки PETKUS. На момент проєктування елеватора цей виробник ще не мав у своєму портфоліо агрегатів великої потужності. Для кожної лінії була потрібна сушарка продуктивністю 60 т/год, і компанія PETKUS запропонувала встановити три сушарки продуктивністю 20 т/ год. Саме тому довелося встановлювати комплекси з трьох сушарок на кожну лінію. З часом земельний банк компанії у цьому регіоні поступово збільшувався, збільшувались обсяги зерна, і це змусило робити кроки у бік підвищення продуктивності елеватора. У 2018 році виконали масштабну реконструкцію підприємства: добудували ще одну лінію приймання на 100 т/год. Тут установили сушарку французького виробника LAW, яка сушить 40–50 т/год. Це дало змогу підвищити загальну продуктивність сушіння кукурудзи за зняття 10% вологості до 180 т/год.
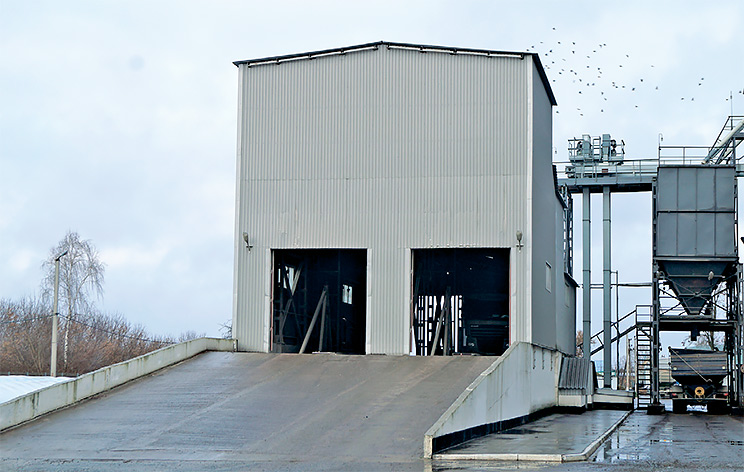
Потреба у додатковій продуктивності сушіння з’явилась і через зміни в термінах збирання кукурудзи. Якщо раніше для цього виділяли 60 днів, то тепер намагаються завершувати збирання за 40–45 днів. Це пов’язано насамперед із посівною кампанією озимих культур — після збирання ранніх гібридів кукурудзи в поле відразу заходять трактори й сіють пшеницю. Другий момент пов’язаний із небажанням лишати кукурудзу в полі на зимівлю. У будь-якому разі це призводить до помітних втрат урожаю через діяльність людей і диких тварин, а також погіршується якість зерна. Крім того, пізнє збирання часто пов’язане з підвищенням вологості зерна, що тягне за собою додаткові витрати на сушіння.
Зупинки сушарок на профілактику відбуваються за графіком, який залежить від типу культур: олійні чи зернові, вологі або практично сухі, забруднені й чисті. Загалом раз на 5–7 днів сушарки зупиняють, їх оглядають і чистять. На це витрачається 2–4 год на одну сушарку.
Наразі підприємство на всіх сушарках використовує природний газ. Витрати на зняття тонно-відсотка в сушарках обох виробників (PETKUS і LAW) практично однаковий — 1,35 м. для зернових і 1,59 м. для олійних. Ще до минулого року це був найвигідніший і найзручніший енергоносій для сушіння зерна. Нині ситуація докорінно змінилась, і компанія не лише розглядає, а й шукає обладнання для використання альтернативних видів палива. Це буде непростим завданням, бо розташування сушарок уздовж силосів суттєво обмежує можливість установлення теплогенераторів. Також є певні сумніви щодо пожежної безпеки теплогенераторів, що працюють без теплообмінників.
У силосах і рукавах
На кожній лінії встановлено по три хопери на 700 м. кожен. Два з них використовують для вологого зерна, один — для сухого. Коли зерно «заспокоїлось» після сушіння, його завантажують у металеві силоси або у поліетиленові зернові рукави. Цю технологію застосовують вже сьомий сезон і досягли чималих успіхів. Загальна кількість зерна, що вантажать у рукави щосезону, у середньому становить 50 тис. тонн. До речі, так зберігають усі культури, окрім ріпаку, який одразу відвантажують (під нього заздалегідь укладають контракти й зберігати його немає потреби).
Зберігають культури в рукавах мінімум три місяці: менше — економічно не вигідно. Тому рукавне зберігання тут триває аж до червня включно. Якість зерна нічним не гірша від того, що зберігають у металевих силосах. Головне — закладати зерно з якісними показниками згідно з ДСТУ. Також треба стежити, щоб під час зберігання не підтікала ґрунтова волога, а також вчасно проводити боротьбу з гризунами й птахами.
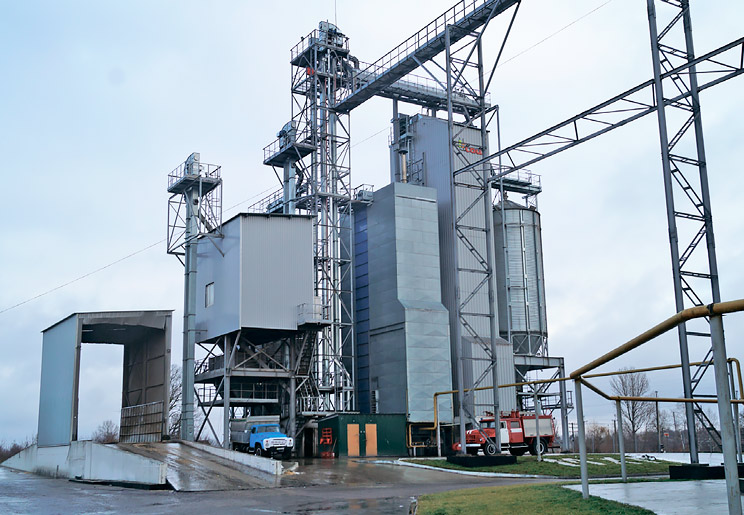
Цього року також почали зберігати в рукавах вологу кукурудзу. Саме на цьому підприємстві термін зберігання становив один місяць, а на інших елеваторах компанії вже становить 65 днів, і планово розвантаження на сушіння буде здійснюватися після 90 днів зберігання. Цю технологію впровадили передусім для того, щоб пришвидшити збирання кукурудзи в полі. Для цього залучаємо максимальну кількість комбайнів та іншої техніки, але технологічна продуктивність елеватора має певні межі. Щоб це не впливало на швидкість збирання, вирішили зберігати вологу кукурудзу в рукавах до того моменту, коли зерно буде повністю зібрано з полів. Це додаткові витрати, однак такий спосіб є вигіднішим, ніж лишати кукурудзу в полі на зиму й потім збирати її у лютому або березні.
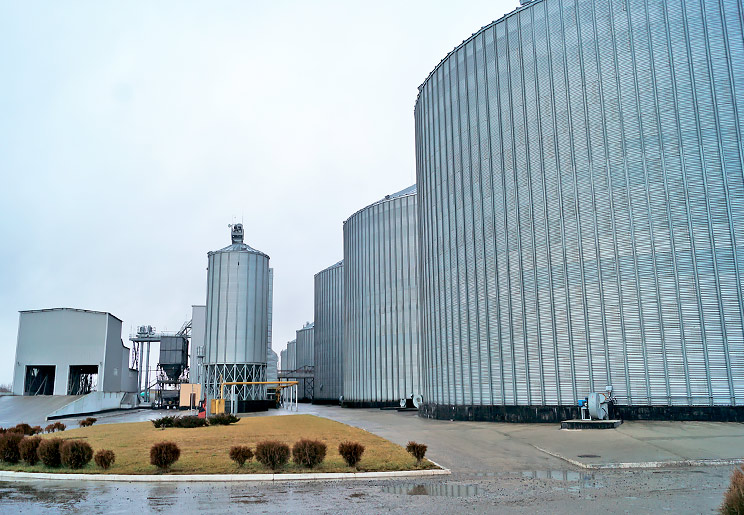
Окрім вологої кукурудзи в рукавах мають досвід зберігання соняшнику з вологістю 10–11% протягом 90 днів. Довелось постійно контролювати стан культури (проколювати рукав і відбирати зразки для перевірки). Але коли настав час вивантажувати, соняшник мав такі самі органолептичні показники, як і відразу після збирання.
Для боротьби з гризунами залучають підрядні організації. По території підприємства і на майданчиках для зберігання зернових поліетиленових рукавів улаштовують пастки для гризунів, а також установлюють газові пушки й звукові пристрої для відлякування птахів. Періодично їх вмикають і вимикають, щоб переривати процес звикання до небезпечних звуків.
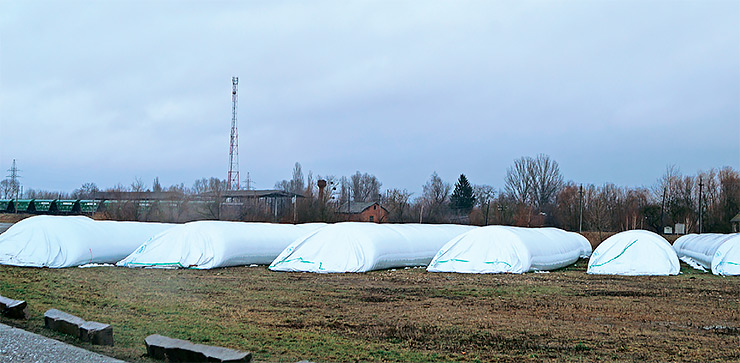
Металеві силоси зберігання мають різний об’єм: три силоси — на 15 тис. м. і три силоси — на 20 тис. м.. Цієї кількості не завжди вистачає, бо одночасно доводиться працювати з різними культурами. Проте планування дозволяє розподіляти потоки зерна, і якщо з логістикою не виникає труднощів, дискомфорту в роботі немає. Звісно, затримання з вагонами або зміни в планах відвантажень тих або інших культур створюють проблеми, але все можна вирішити за допомогою зернових поліетиленових рукавів. Тому в найближчому майбутньому добудова нових силосів не розглядається. Взагалі сучасна концепція компанії ПрАТ «МХП» у напрямі зберігання дещо змінилася: нові елеватори будують взагалі без силосів, а для тривалого зберігання застосовують тільки поліетиленові рукави. З економічного погляду це значно ефективніше, ніж одразу вкладати чималі капітальні інвестиції в будівництво фундаментів, силосів зберігання й транспортні системи. З тим усю іншу інфраструктуру елеватори мають — від ваг, лабораторій і завальних ям до залізничного і автомобільного відвантаження.
Залежність від Укрзалізниці
Через віддаленість від основних магістралей удається відвантажувати тільки по дев’ять вагонів на добу. Локомотив їздить із Шепетівки, і в сезон навантаження на нього досить велике. Таким чином, через обмеження від Укрзалізниці підприємство встигає відвантажувати у 2–3 рази менше, ніж теоретично могло б відвантажувати з огляду на власні технологічні можливості. Власний тепловоз поки що купувати не збираються, бо за нинішніх обсягів перевалки потужності відвантаження вистачає.
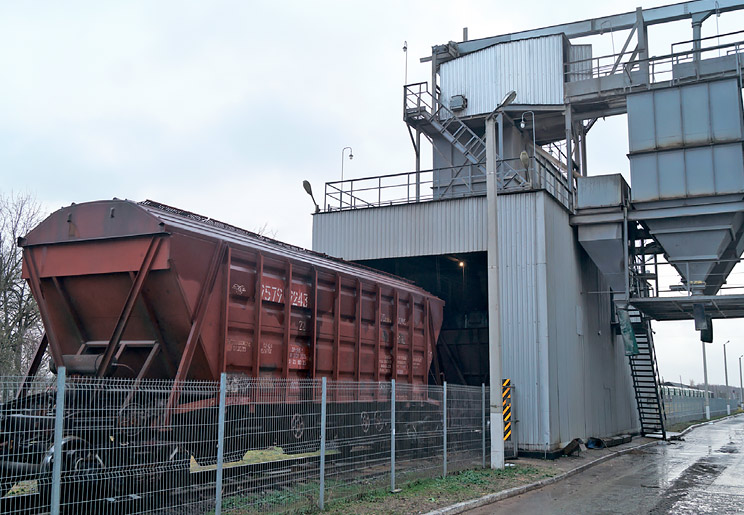
Автоматизацію — на новий рівень
На сьогодні на підприємстві відбувається реалізація проєкту повної автоматизації підприємства. Під час будівництва автоматизацію зробила компанія PETKUS. Після наступних модернізацій до кожної нової технологічної лінії автоматизацію робили інші компанії. Усе це працювало, але не було єдиного взаємопов’язаного керування всіма системами підприємства. Нині разом із компанією «Зернова Столиця» реалізується проєкт «Розумний елеватор». Перший етап — автоматизація всіх технологічних процесів (уже реалізований), тривають тільки деякі незначні корегування системи. Також у процесі реалізації проєкт автоматизації внутрішньо складської логістики, щоб зважування, відбирання зразків і визначення потрібної точки вивантаження теж відбувалося без участі людей-операторів.
Додатковий заробіток на відходах
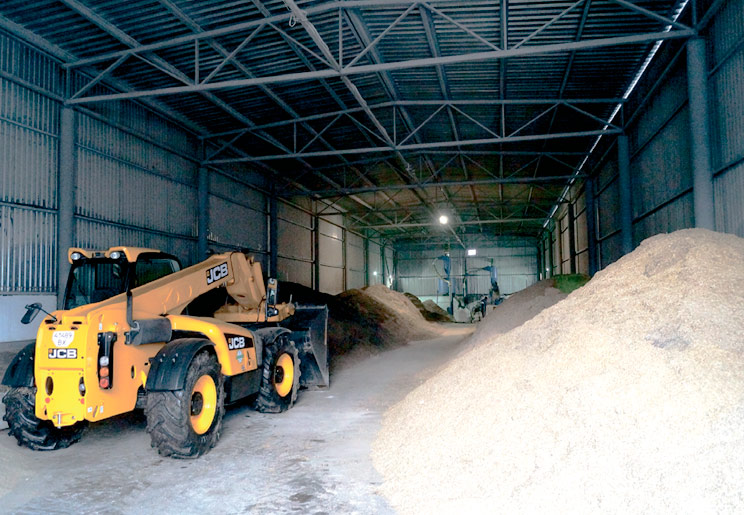
У процесі технологічної роботи підприємства виникає значна кількість органічних відходів. Це — смітна домішка, яка відокремлюється від зерна очисними машинами. Відходи збирають в окремому ангарі, роблять із них тверде паливо у вигляді брикетів, а також харчову добавку у вигляді борошна для годівлі тварин. Кінцевий продукт пакують у біг-беги й відвантажують автомобільним транспортом. Таким чином, вдається уникати забруднення довкілля, скорочувати викиди метану і навіть трішки заробляти. Брикети мають вологість близько 10%, тож їх спалювання у будь-яких котлах відбувається без жодних проблем.
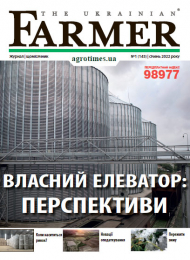