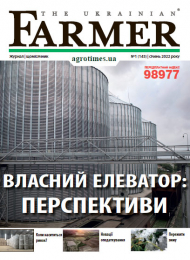
Робота з давальницьким і придбаним зерном вимагає надавати найкращий сервіс та інвестувати в модернізацію елеватора
Оптимальна модернізація
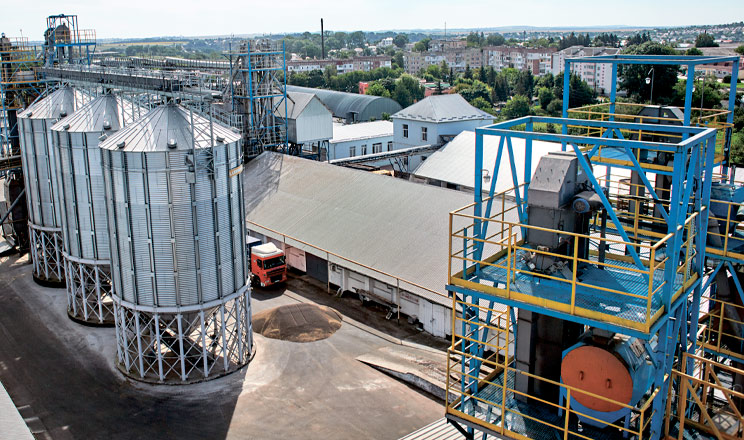
Робота з давальницьким і придбаним зерном вимагає надавати найкращий сервіс і обережно інвестувати в модернізацію елеватора
Збаразький комбінат хлібопродуктів має довгу історію — його будували ще у 1960-ті роки за радянських часів. Відтоді багато чого змінилось у країні, і саме підприємство змушене було підлаштовуватись під потреби сучасності. Наразі це потужне підприємство з великими обсягами перевалки. І це до того, що власного зерна тут немає. Це яскраво свідчить про популярність підприємства серед місцевих аграріїв. Ми завітали до підприємства, щоб подивитись, чим заохочують аграріїв привозити зерно саме сюди.
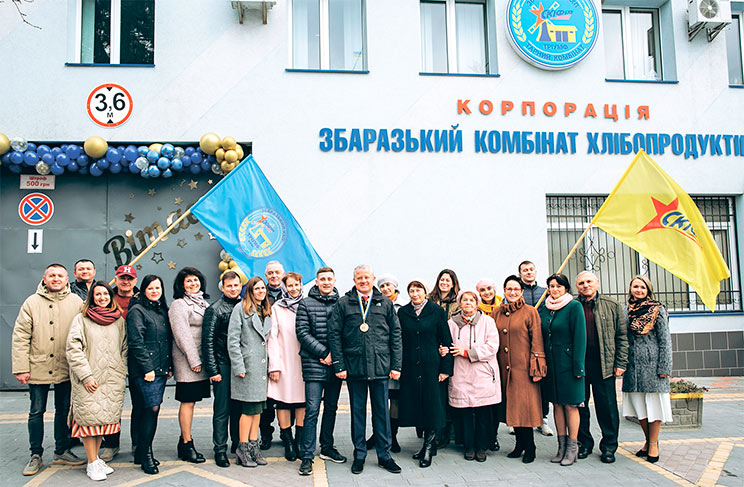
Екскурсію підприємством нам провів головний інженер Володимир Кравчук. Він розповів, що зі звичайного зерносховища з підлоговими складами підприємство поступово модернізували до рівня, що не поступається, а можливо, навіть і кращий за сучасні «суцільнометалеві» елеватори.
Наростити продуктивність
До підприємства привозили зерно всі навколишні агропідприємства. І коли обсяги збіжжя почали збільшуватись, постало питання про модернізацію. Усе потребувало уваги — від приймання до відвантаження. Тому старі технологічні лінії суттєво переробили, щоб наростити продуктивність усіх процесів.
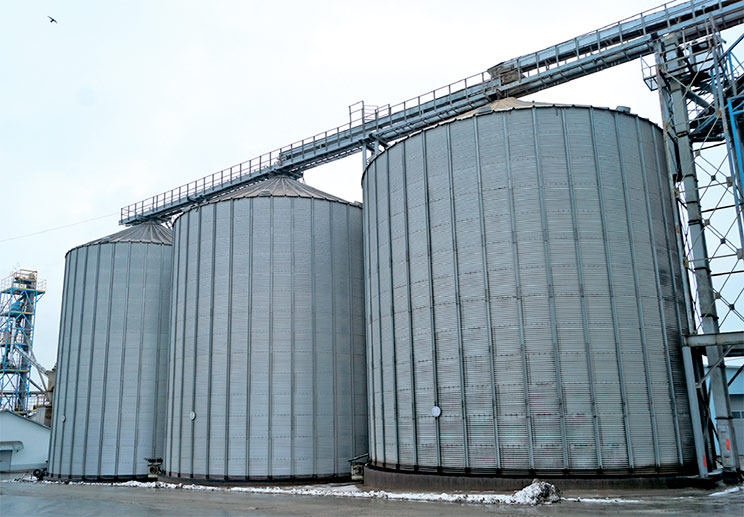
Розпочали з лабораторії. Тут усіляко намагалися зробити дві речі — пришвидшити визначення показників зерна і забезпечити максимальну точність. Для цього лабораторію оснастили автоматичним пробовідбірником, який відбирає зерно за допомогою шнека. Шнек дає змогу відбирати пробу більш об’єктивно, бо вакуум часто втягує більше сміття — воно легше і менше за розміром. Відповідно, показники погіршуються, хоча насправді зерно є чистішим. Тут цієї проблеми вдалось уникнути, клієнти задоволені й не скаржаться на роботу лабораторії. Крім того, було придбано прилади Інфраскан та Інфратек, різнотипне обладнання для вимірювання вологості, а також інші прилади, що потрібні для оперативного аналізу характеристик усіх типів зерна. Це дало свій ефект: на виконання аналізу витрачають у середньому до 15 хв.
Друге завдання полягало у профілактиці роботи обладнання: підприємство почало роботу 1969 року, і до сьогодні експлуатують 13 підлогових складів. Відповідно, там працює досить старе обладнання, що потребує уваги. Ураховуючи, що періоди між сезонами дуже короткі, потрібно за цей час встигнути все перевірити й провести регламентні роботи. Для цього знадобилося підібрати й навчити персонал, який нині становить основу технічної надійності підприємства.
Сушіння дедалі дорожчає
На підприємстві вже майже 10 років працюють модульні сушарки. Дві з них — тримодульні, одна — двомодульна турецького виробника Adakurutma. Упродовж сезону сушарки працюють досить напружено, бо основна культура, яку сушать, це кукурудза, і часто вона надходить із вологістю 30% і більше. Отже, обсяги сушіння великі, і витрати газу (і грошей) відповідні. На тонновідсоток витрачають близько 1,7 м3 газу.
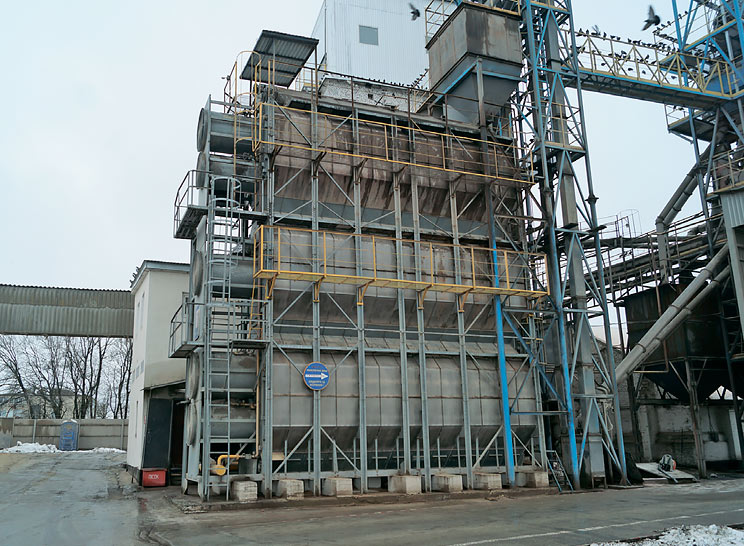
За словами Володимира Кравчука, питання застосування альтернативних джерел енергії постійно обговорюється, але в умовах саме цього підприємства перейти на дешеве тверде паливо поки що не можливо. Якби сушарки були шахтними, ніхто б не вагався. Однак до модульних сушарок теплогенератори технологічно досить важко приєднати. На кожен рівень сушарки потрібно подавати теплоносій різної температури, і без теплообмінників це не реалізується. Втрати на теплообмінниках будуть надто великими й зведуть нанівець усю економію, що можна отримати з використання твердого палива. Тому поки що підприємство й далі використовує природний газ і сподівається, що ціна його рано чи пізно знизиться до прийнятного рівня. Можливо, коли придбають нові сушарки (шахтного типу), одночасно розглядатимуть встановлення твердопаливних теплогенераторів.
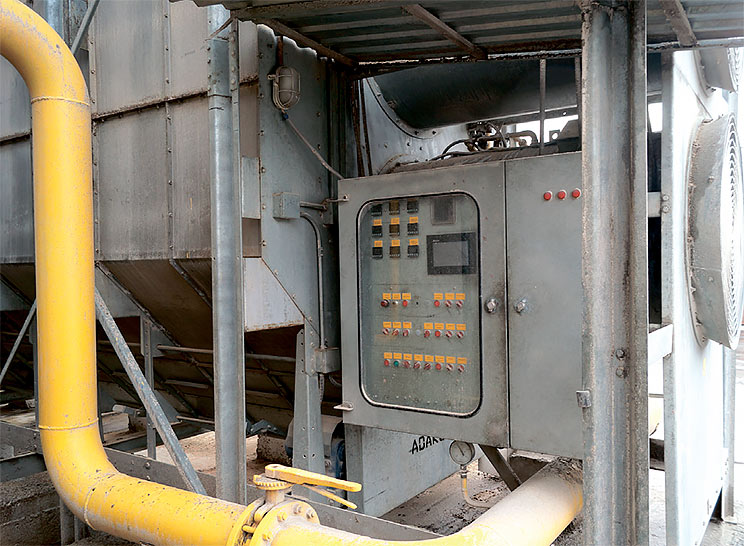
Сушарки чистять щотижня й частіше, залежно від культури та її стану. Крім того, слід ураховувати, що перфорація сушарок розрахована на сушіння всіх типів культур із ріпаком включно, тому під час сушіння кукурудзи з високим умістом вологи очищати доводиться частіше. До того ж продуктивність сушарки знижується через розмір перфорації. Продуктивність кожної з трьох сушарок становить близько 250 т/добу.
Найкраще очищення — своє!
Очисне обладнання — від фірми Buhler (вторинне очищення) і власного виробництва (сепаратори попереднього очищення «МІКРА» і скальператори). Експлуатація різних машин показала, що кожна має недоліки й переваги, і знайти ідеальний варіант виявилось або неможливо, або надто дорого. Зважаючи на те, що підприємство має власні ресурси для побудови очисних машин,__ вирішили взяти найкращі рішення різних виробників і зібрати їх у власних очисних машинах. Цим питанням особисто опікувався головний інженер Володимир Кравчук, і результат виправдав сподівання. Тепер на всіх трьох лініях для первинного очищення застосовують очисні машини власного виробництва.
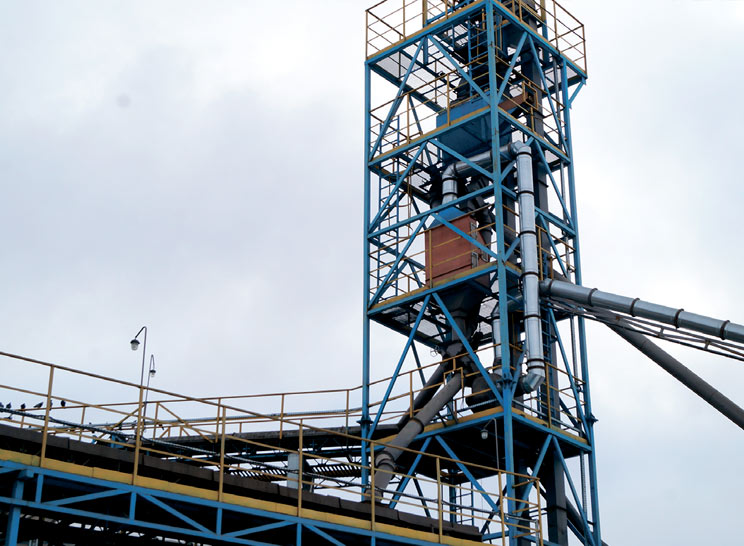
Прийняти та відвантажити
Слід згадати, що нинішній власник отримав підприємство напівзруйнованим. Воно не функціонувало, і переважної більшості обладнання не було. Підлогові склади не мали верхніх транспортерів, нижні галереї були частково розібраними. Тому спочатку обсяги приймання були відверто малими, і тільки за кілька років удалось вийти на рівень 40 тис. тонн.
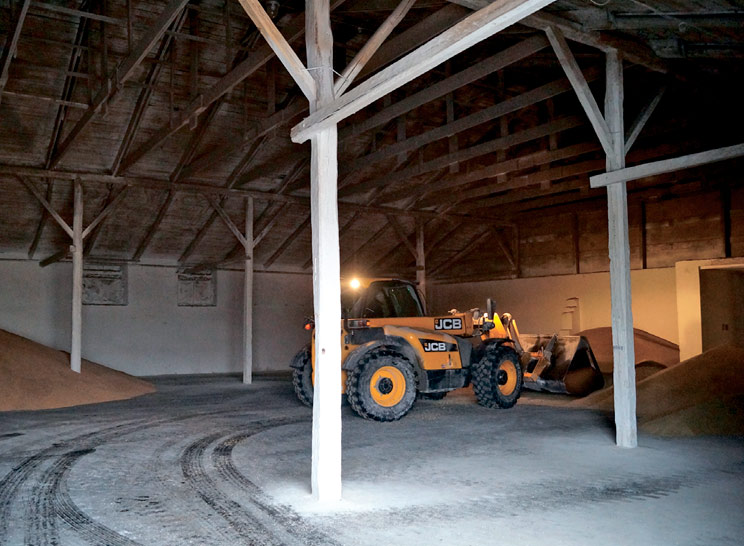
Відтоді відбулося багато змін, і тепер підприємство приймає за рік 220 тис. тонн. На наступний рік планується прийняти 240 тис. тонн, і це на потужностях одночасного зберігання всього у 65 тис. тонн! Зерно звозять як власними вантажівками (у наявності 16 автомобілів), так і транспортом власників зерна. Спочатку встигали вантажити чотири вагони на добу, потім — шість, ще згодом вийшли на показник дванадцять вагонів на добу. І це вже було щось нечуване — усі працювали в авральному режимі.
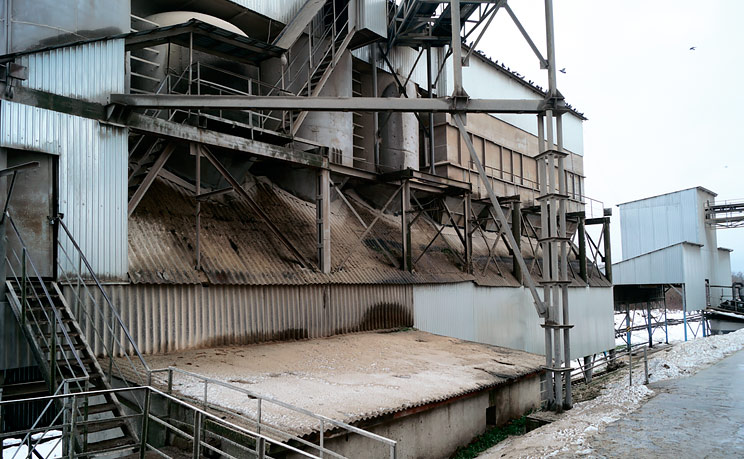
Під час реконструкції було суттєво посилено пункт відвантаження, і тепер за добу встигають завантажувати по 36–40 вагонів. Для цього було встановлено лебідки для переміщення вагонів, збудовано накопичувальні бункери для одночасного завантаження двох вагонів. Залізничні ваги встановили поруч із точкою завантаження, і над ними зробили ще один маршрут, за допомогою якого довантажують кожен вагон до потрібної ваги. Лінія подачі вміщує 12 вагонів, які переміщує між станцією й елеватором власний локомотив.
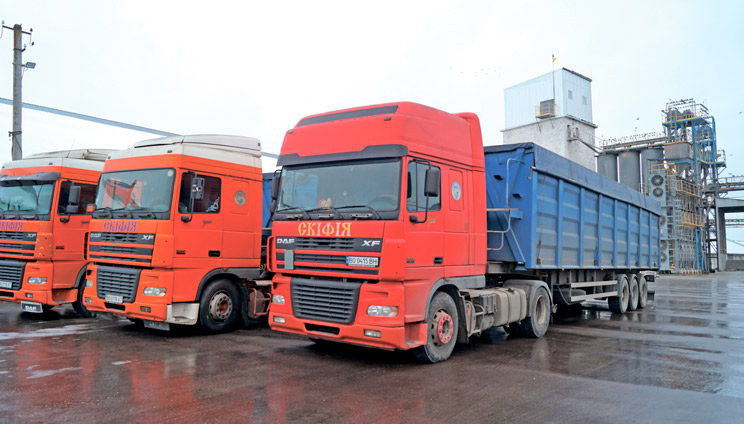
Коли житло поруч
Підприємство розташоване посеред міста, тому особливу увагу доводиться приділяти захисту довкілля. Робота із зерном завжди пов’язана з великою кількістю пилу та решток, і потрібно докладати значних зусиль, щоб усе це не заважало нормальному життю людей. За словами головного інженера Володимира Кравчука, системи аспірації тут виготовляють самостійно. Після звичайних циклонів додатково встановлюють рукавні фільтри, щоб ще краще очищувати використане повітря. Модульні сушарки вносять свою частку забруднень, бо вентилятори у будь-якому разі видувають пил, і забезпечити абсолютну чистоту не вдається. Компанія також планує встановити системи пиловловлення в точках розвантаження — це буде наступним етапом боротьби за чистоту.
Кого обирають
Власник вкладає кошти в переобладнання. Не першому етапі використовували турецьке й іспанське обладнання (силоси Symaga і MySilo). Нині перейшли до вітчизняного виробника «Лубнимаш» — продукція підприємства повністю відповідає сучасним вимогам і коштує менше, ніж закордонне.
Транспортне обладнання купують у фірми «Елеваторні системи» — молодої компанії з Дніпра, яка швидко вийшла на досить високий рівень виробництва, і тепер може конкурувати з добре відомими вітчизняними брендами.
Підрядник «Авангард Житомир», з яким працюють уже не перший рік, забезпечує монтаж і підтримку обладнання. Головною перевагою цього підприємства є надійність, компетентність і порядність, без чого неможливо побудувати довгострокові відносини у виробничому бізнесі.
ГОВОРИТЬ ЕКСПЕРТ
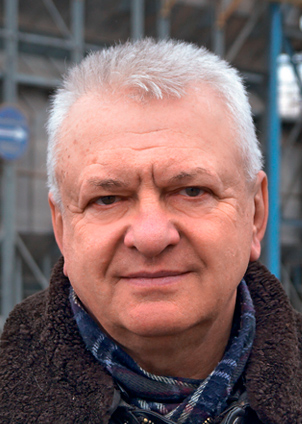
Володимир Кравчук, головний інженер ТОВ «Збаразький КХП»
— До нас приїжджають представники різних виробників елеваторного обладнання і пропонують знести підлогові склади, а на їхньому місці збудувати металеві силоси. Однак я категорично не хочу цього робити. Річ у тім, що підлогові склади мають свої переваги, яких ніколи не буде у металевих силосах, навіть незважаючи на меншу технологічність і потребу в обслуговуванні. Тут зерно краще зберігається, його легше контролювати. Тому доки в нас є можливість опрацьовувати усе зерно, що надходить до підприємства, від підлогових сховищ відмовлятись не збираємось.
Ми встановили три металевих силоси на 2500 т кожен. Там є кабельна термометрія, а також встановлено аераційні вентилятори по два на силос. У разі потреби, коли треба швидко охолодити зерно, через адаптери приєднуємо потужніші вентилятори. Тож не треба вкладати зайві кошти у чотири аераційні вентилятори на кожен силос.
У процесі модернізації підприємства ми позбавились від неефективних маршрутів, поглибили завальні ями, посилили норії, щоб збільшити їх продуктивність. Старі 100-тонні норії «видавали» фактично 45 т на годину, що не влаштовувало з огляду на продуктивність іншого обладнання. Територію підприємства асфальтували й бетонували, у найбільш навантажених зонах вклали залізобетонні плити, щоб транспорт міг вільно маневрувати. Окремо підготували майданчик для рукавного зберігання, однак за вчасної подачі вагонів ця технологія не використовується.
Рукавне зберігання розглядали й навіть підготували під це майданчик. Однак якщо вагони подають вчасно, підприємство встигає звільняти склади під нове зерно.
Підприємство хоч і автоматизоване, але неповністю. Є багато ділянок, де автоматизацію впроваджувати економічно невигідно. Тому в таких місцях працюють люди — вони забезпечують досить великий рівень продуктивності, і підприємство показує хороші результати (3,7 оберту за сезон).
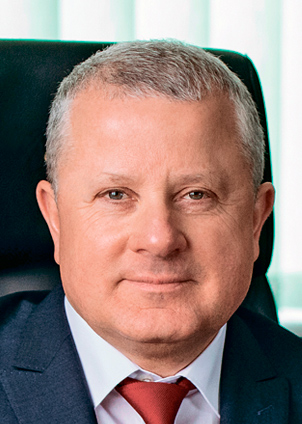
Олександр Шпак, власник корпорації «Збаразький КХП»
— До нашої корпорації крім самого Збаразького КХП входить транспортна і торговельна компанії, а також тарний комбінат. Розпочиналось усе з фірми «Скіфія», яка свого часу придбала Збаразький КХП. Комбінат мав власну переробку і виготовляв борошно та крупи, велику частку продукції експортували. Однак із часом цей бізнес втратив прибутковість, і було вирішено про відмову від цього напряму. Тож усі зусилля сконцентрували на прийманні й доробці зерна та його на експорті.
На сьогодні підприємство розвинулось до рівня, коли без проблем приймає 220 тис. тонн зерна на рік. І це не межа — за сприятливих ринкових умов ми зможемо зробити набагато більше. Щонайменше технічні можливості для цього є. Головне — щоб Укрзалізниця могла впоратись із перевезенням. А цього року ми натрапили на значущі труднощі: через відсутність тяги зерно вивозили надто повільно, і це суттєво вплинуло на загальні результати роботи підприємства. Взагалі підвищити обсяги перевалки до 300 тис. тонн на рік не є проблемою. Нам довіряють, і до нас везуть зерно. Але нам потрібно 800 вагонів на місяць, щоб досягти такого результату. На жаль, Укрзалізниця користується своїм монопольним становищем і суттєво впливає на зерновий ринок України.
Незважаючи на труднощі з Укрзалізницею, підприємство планує й надалі збільшувати обсяги перевалки. На наступний сезон ми плануємо досягти 240 тис. тонн. Це буде досягнуто привабливими цінами, високою якістю послуг, мінімізацією простоїв автотранспорту, швидкою оплатою й щоденним підлаштуванням під вимоги клієнта. Це означає, що за потреби компанія готова робити реконструкцію технологічних ліній і надалі покращувати сервіс на кожному етапі приймання зерна.
У модернізації підприємства ми керуємось принципами доцільності. Передусім нас до цього спонукає конкуренція і вимоги зовнішнього світу. Та сама Укрзалізниця свого часу вимагала збільшити потужність відвантаження до 54 вагонів на дві доби. Були вкладені скажені гроші в оновлення вузла відвантаження, однак Укрзалізниця не може їх вчасно вивезти!
На перших етапах модернізації ми віддавали перевагу імпортному обладнанню, бо вітчизняному не довіряли. На той час культура виробництва у нас була на низькому рівні, й, відповідно, страждала якість. Однак тепер ситуація докорінно змінилась — українські виробники пропонують високоякісний продукт, який нічим не поступається закордонним аналогам. Ба більше: вони готові адаптувати своє обладнання до наших потреб, тоді як закордонні виробники не такі гнучкі.
Зізнаюсь, що свого часу планували глобальну реконструкцію підприємства. Підлогові склади хотіли замінити на металеві силоси, але розумні люди порадили цього не робити. І виявилось, що з підлоговими складами ми гнучкіші й більш оперативні, ніж з «банками». У нас є кілька металевих силосів, але переважна більшість зерна зберігається саме в підлогових складах.
Окремої уваги на сьогодні заслуговує питання сушіння зерна. Ціна на газ підвищилась до такого рівня, що доводиться розглядати альтернативні джерела енергії. Хоча ще рік тому про твердопаливні теплогенератори я взагалі не думав. Тут не було ані економіки, ані продуктивності. Зрозуміло, що нинішня ціна на газ є результатом політичного тиску, і рано чи пізно ситуація зміниться на краще. Однак, якщо покращень не відбудеться, альтернативу шукати доведеться.
Подальший розвиток підприємства залежатиме від потреб ринку. Технічно оновлюватися ми й далі обов’язково будемо. Щодо переробляння: борошно і крупи поки що малорентабельні. Цікавішими є виробництво олії й насіння, тому цілком можливо, що будемо розвиватись у цих напрямах.
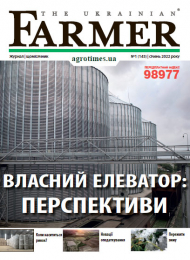