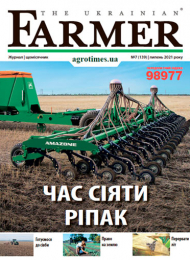
Ефективність Низівського елеватора — надійне обладнання та професіоналізм
Надійний елеватор
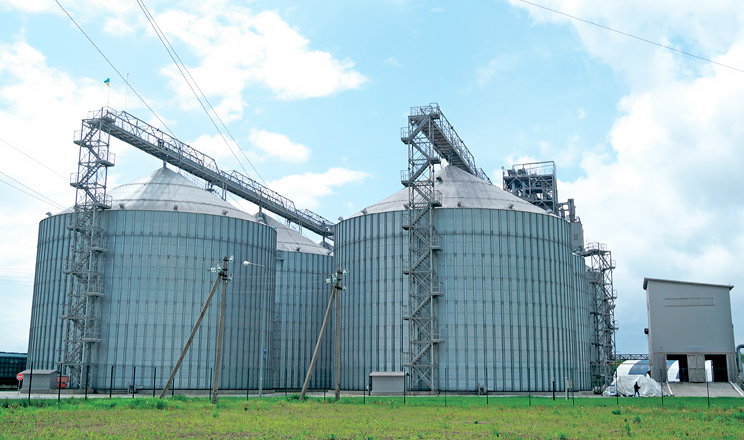
На думку власників Низівського елеватора, ефективності можна досягти високим рівнем надійності обладнання та професіоналізмом персоналу
Надійно і чесно
У смт Низи під Сумами 2014 року розпочав роботу елеватор, що входить до структури «AVIS УкрАгро» і має офіційну назву ТОВ «Зернова Індустрія». Цей об’єкт створювали насамперед під власні потреби, бо треба було забезпечити доробку й зберігання зерна з власних угідь (близько 20 тис. гектарів), на яких вирощують переважно кукурудзу і сою. Тож потреба в сушінні й зберіганні була значною — скільки доводилось возити зерно на елеватор «НІБУЛОН» майже за 200 км, бо ближче елеваторів, з якими можна було стабільно співпрацювати, не було, а наявні не забезпечували прийнятних умов. Доводилося стояти в чергах, періодично виникали питання щодо якісних показників зерна. Тож елементарний підрахунок показав, що інвестиція у власний елеватор дозволить працювати значно ефективніше.
Перед початком будівництва власник відвідав багато українських елеваторів, а також неодноразово їздив до США, щоб перейняти досвід створення таких об’єктів. Після збирання й аналізу інформації було вирішено, що обладнання має бути надійним і мати максимально можливий строк експлуатації. На той час (2012–2013 рр.) в Україні будували багато елеваторів, однак вітчизняне обладнання ще не набуло значного поширення через недостатні експлуатаційні характеристики. Відомі закордонні виробники мали перевагу у вигляді багаторічного досвіду, відпрацьованих технологій і якісних матеріалів. Саме тому переважну більшість обладнання було придбано за кордоном.
І ефективно, і продуктивно
Щорічні потреби в сушінні кукурудзи доволі значущі. Щорічний обсяг вирощування цієї культури становить близько 100 тис. тонн. Щоб не лишати кукурудзу в полі на зиму, треба було забезпечити не лише швидке збирання, а й сушіння. Ураховуючи, що елеватор працює ще й з іншими фермерами, потрібно було забезпечити об’єкт сушарками великої потужності. Тому вирішили придбати високопродуктивну баштову сушарку SUKUP, а також шахтну сушарку італійського виробника Bonfanti.
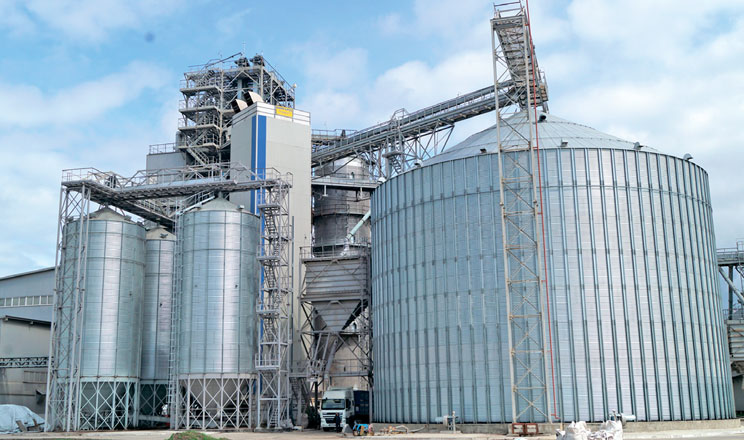
Чому зробили саме так? Однієї сушарки було недостатньо, щоб справлятись із сушінням у пікові періоди. Крім того, хотілось мати можливість сушити не лише кукурудзу, а й такі культури, як ріпак. Продуктивність баштової сушарки SUKUP 7024 — 170 т/год за умови знімання 5% вологості по кукурудзі. Сушарка Bonfanti забезпечує продуктивність у 120 т/год. Витрати газу тут становлять близько 1,2–1,4 м. на зняття тонно-відсотка вологості залежно від стану зерна, а також температури й вологості навколишнього повітря. Сушать зерно як теплою осінню, так і холодною зимою. Доводилося запускати сушарки навіть за температури –20 °С з попереднім розігрівом, щоб автоматика «побачила» доступний температурний режим. Саме у цей час комбайни могли збирати, тож довелось і сушити кукурудзу за не найсприятливіших умов.
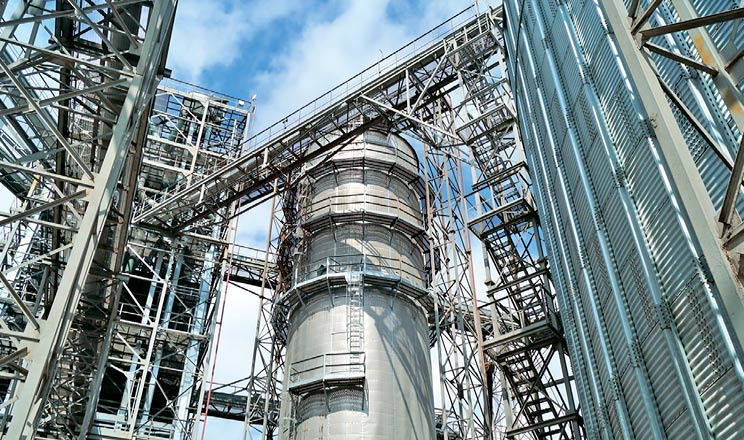
Сушарка SUKUP може працювати як в автоматичному, так і в ручному режимі, але жодного дня вона не працювала в «автоматі». Оператори змінюють режими на основі власного досвіду — збільшують або зменшують температуру сушіння, а також регулюють швидкість вивантаження. Це дозволяє раціональніше витрачати пальне і разом із тим працювати з максимальною продуктивністю. Сушарка Bonfanti залежно від культури має окремі програми, за якими працює. Тут на вході й виході встановлено датчики вологості, за якими комп’ютер коригує параметри сушіння в межах програми. Іноді оператори змінюють налаштування вручну — зазвичай для зерна з одним рівнем вологості одного коригування достатньо.
Згідно з початковим проєктом було встановлено два хопери для вологого зерна на сушарку. Тобто можна було одночасно нагромаджувати по 1000 т. Цього виявилось замало, і за три роки додали ще по одному хоперу на 500 т кожен. Це дало змогу краще розподіляти культури за рівнем вологості та якісними показниками.
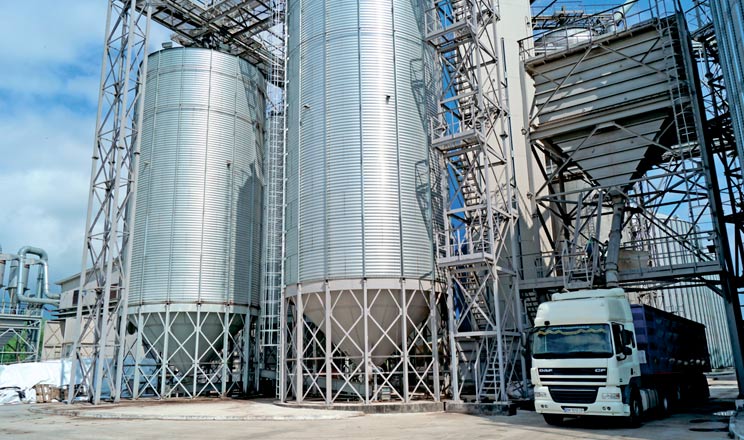
Сепаратор і скальператори обрали від компанії Buhler, бо цей виробник є лідером галузі й гарантовано може забезпечити потрібну якість і продуктивність очищення зерна. І навіть висока ціна не є причиною відмовлятись від якості та надійності. Досвід експлуатації показав, що з очищенням зерна проблем не виникає, машини стабільно працюють за максимальних навантажень, і це значною мірою додає стабільності у функціонуванні всього елеватора.
Первинне очищення зерна виконує скальператор барабанного типу із системою пиловидалення. Тут відбирають усі великі домішки, лишається тільки те, що проходить крізь вічко 20 . 40 мм. Далі зерно спрямовують у силоси на зберігання або в хопери для вологого зерна, якщо потрібне сушіння.
Для доведення зерна до базових показників застосовують інший сепаратор TAS від Buhler. За словами головного інженера підприємства, це досить зручна машина з простими регулюваннями й заміною сит. Щоб зробити процес очищення максимально ефективним, у лабораторії є практично повний комплект сит. Спочатку лаборант пробує пересівати зерно на різних ситах і дивиться, де відбувається найкраще очищення. Відповідно до отриманого результату налаштовується сепаратор і починається очищення.
Із самого початку розглядали силоси закордонного і вітчизняного виробництва. Однак уже на першому етапі стало зрозумілим, що закордонні пропозиції надто дорогі. Своєю чергою, продукція українських компаній відрізнялась кращим співвідношенням ціни та якості. Розглядали пропозиції кількох заводів, але зупинились на продукції KMZ Industries. Ця компанія пропонувала дах із несними конструкціями у вигляді ферми, що гарантувало хорошу стійкість до снігових навантажень. Це стало вирішальним, бо такі речі, як уміст цинку, можна отримати від будь-якого виробника, а панелі й ребра жорсткості виготовляють на однакових станках, тож відмінностей між ними практично немає. У результаті не пожалкували — територіальна близькість дала змогу оперативно вирішувати різні питання, що виникали в процесі будівництва.
Кожен силос оснащено 15 термометричними кабелями. Відстань між датчиками становить 1,25 м. Зачисні шнеки французького виробництва DENIS працюють і сьогодні. На одному зі шнеків замінили кілька підшипникових вузлів й оливу. Більше капітальних ремонтів не було. Редуктор, що замінили, ще був у робочому стані, однак видавав шум і вібрацію невідомого походження. Навіть виробник не зміг визначити, що з ним не так. Але вирішили замінити, щоб не створювати проблем у сезон. Днища перфоровані під ріпак, на кожному силосі встановлено чотири вентилятори по 22,5 кВт кожен, які використовують у сезон пшениці й кукурудзи.
Непросте будівництво
Елеватор побудували на території асфальтобетонного заводу. Тож перед початком будівельних робіт довелося виконати чималий обсяг демонтажу. Коли рили котлован під норійну вежу, стикнулись із потребою знизити рівень ґрунтових вод. Котлован розміром 15 . 15 м швидко наповнився водою, стінки осипались і утворилася воронка діаметром 25 м! Довелося ставити 12 потужних помп, які працювали більше як шість місяців. Після встановлення металевого кесона змогли зробити фундамент норійної вежі, і тільки тоді «відпустили» воду. Схожа ситуація сталася і під час будівництва фундаменту під автоприймання. Після завершення будівництва зробили гідроізоляцію підземних приміщень. Усього на будівництво і монтаж технологічного обладнання витратили один рік.
Транспортне обладнання
У підприємстві не застосовують стрічкові транспортери. Тут працюють тільки норії і ланцюгові транспортери від американського виробника SWEET. Претензій немає, все обладнання футероване зносостійкою сталлю (днище й бічні стінки). Приводи норій і горизонтальних транспортерів обрали від американського виробника Dodge. За період експлуатації жодних претензій до редукторів або електродвигунів не виникало. На сьогодні зношення виявлено тільки на найбільш навантажених маршрутах — це відвантаження. Приймання здійснюється на дві ями, звідки зерно розподіляється по усьому елеватору. А на відвантаженні фактично працює одна лінія. Цього року планують замінити лише зірочки, а ланцюги поки що в нормальному стані. Конвеєрні скребки з поліетилену пройшли тривалий період експлуатації й також мають відчутне зношення. Тому в Дніпрі замовили поліуретанові накладки, які прикрутили до скребків. Кожну накладку можна повертати різними сторонами, тобто з них можна отримати чотири ресурси. Конвеєри спираються на підтримувальні лижі, які час від часу доводиться замінювати. Але це витратні матеріали. Деякі короткі конвеєри перевели на поліуретанові ролики, і вони нормально працюють. Першу заміну зробили три роки тому, й поки що все працює без зауважень. На деяких приймальних конвеєрах довелося замінити ланцюги через потрапляння у завальну яму різних металевих предметів. Але це трапляється на будь-якому елеваторі.
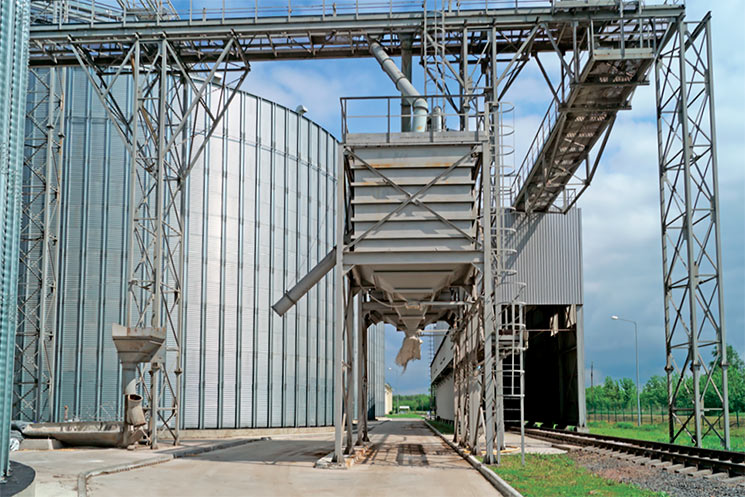
Відвантаження з особливостями
Оскільки підприємство розташовано на великій відстані від портів й інших потенційних покупців зерна, практично все зерно відвантажують залізницею. За одну подачу на елеватор завозять 17 вагонів. Потреби у власному локомоти ві немає, бо станція тупикова, і «Укрзалізниця» працює практично без затримок. Продуктивність обладнання дозволяє відвантажувати маршрут протягом доби, але фактично встигають дещо менше — 34 вагони. Під час будівництва залізничного приймання не влаштовували, бо не було такої потреби. Проте технологічна можливість розвантажити вагон є, якщо раптом якість зерна не відповідає базованим значенням.
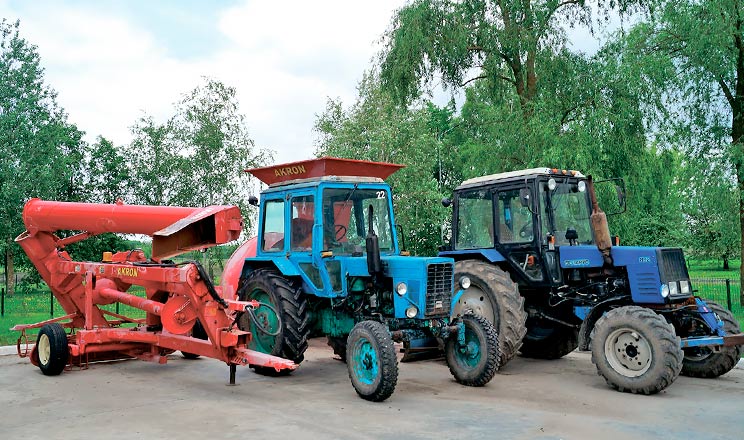
Керування з одного комп’ютера
Оператор на моніторі бачить, як працює весь комплекс і кожна окрема лінія. Фактично це людина, яка є очима всієї зміни: у разі спрацювання датчика підпору, зупинки обладнання, заповнення бункера вся інформація через радіостанцію доноситься іншим працівникам зміни — від керівника до слюсаря. Персонал розуміє, що відбувається на підприємстві, які лінії працюють, куди спрямується зерно.
ГОВОРИТЬ ЕКСПЕРТ
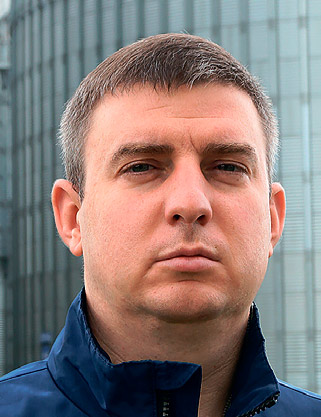
Олександр Гребеник, директор ТОВ «Зернова Індустрія»
— З початку роботу елеватора власник одразу поставив завдання — завойовувати авторитет серед місцевих аграріїв, щоб вони були задоволені цінами на зерно й послугами, лабораторія працювала прозоро і не виникало спірних питань щодо якісних показників. Це, своєю чергою, мало мало сприяти збільшенню обсягів перевалки й, відповідно, збільшити прибутки підприємства. На той момент практично усі аграрії були добре знайомі із проблемами елеваторного бізнесу і шукали більш прийнятні умови. Тому чесну роботу елеватора швидко оцінили й повезли зерно до нас. Впевнений, що відділ трейдингу забезпечує до 30% перевалки нашого елеватору насамперед завдяки адекватним умовам роботи.
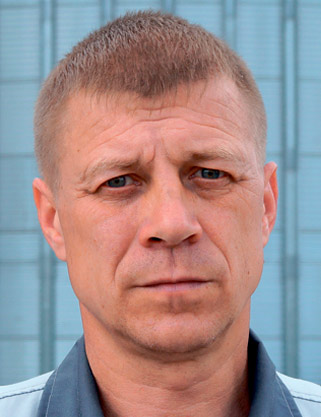
Юрій Остапенко, головний інженер
— В експлуатації складнішою є шахтна сушарка Bonfanti. Це стосується насамперед газових пальників та їх автоматики. Наприклад, була ситуація, коли якась комаха залізла всередину, перекрила важливий канал, і ми не могли запустити сушарку, доки усе не прочистили. Однак працювати з цією сушаркою легше. Конструкція баштової сушарки SUKUP простіша, але потребує більше уваги під час роботи. Наприклад, під час активного сушіння кукурудзи її доводиться мити. Верхня зона перфорації засмічується лушпинням, яке слід видаляти. Ми робимо це без зупинки сушіння. Операцію повторюють не рідше одного разу на тиждень. Шахтна сушарка очищується винятково під час зміни культур, а у міжсезоння виконується «генеральне прибирання» усіх внутрішніх поверхонь із використанням щіток і скребків.
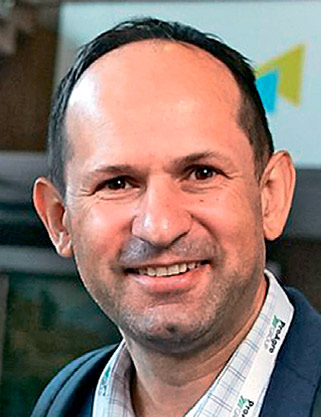
Олексій Кривульченко , технік компанії «Бонфанті»
— Компанія Bonfanti поставила на елева тор «Зернова Індустрія» велику шахтну сушарку моделі XL 295 CE продуктивністю 1500 т на добу у 2014 році. Її обрали для одночасної роботи з баштовою сушаркою іншого виробника, щоб забезпечувати більш ощадне сушіння.
Сушарка має кілька важливих переваг: вона простіша і зрозуміліша для оператора, може працювати в автоматичному режимі з різними культурами. Також ця сушарка не забруднює довкілля, і під час активної роботи територія навколо неї залишається чистою. Важливою перевагою є низькі витрати газу на сушіння. За словами місцевих операторів, із цією сушаркою працювати дуже просто, і до того ж вона не складна в обслуговуванні.
Монтаж здійснювала компанія «БОЕЗ», і це було непростим завданням. Умови були вкрай важкими через надлишок води на будівельному майданчику. Однак, попри труднощі сушарку запустили на початку жовтня 2014 року і почали сушити кукурудзу.
Протягом минулих років сушарка окрім кукурудзи працювала із соєю, зерновими і соняшником. За весь час технічних питань практично не виникало. Значною мірою питаннями експлуатації опікувався головний інженер елеватора «Зернова Індустрія» Юрій Остапенко. Завдяки йому представникам Bonfanti не було потреби їздити на об’єкт для перевірки й обслуговування сушарки.
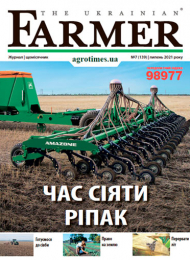