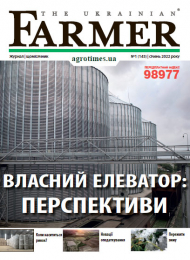
Будівництво фермерського елеватора завжди пов’язано з дефіцитом коштів і неможливістю помилитися під час вибору обладнання
Елеватор у полі
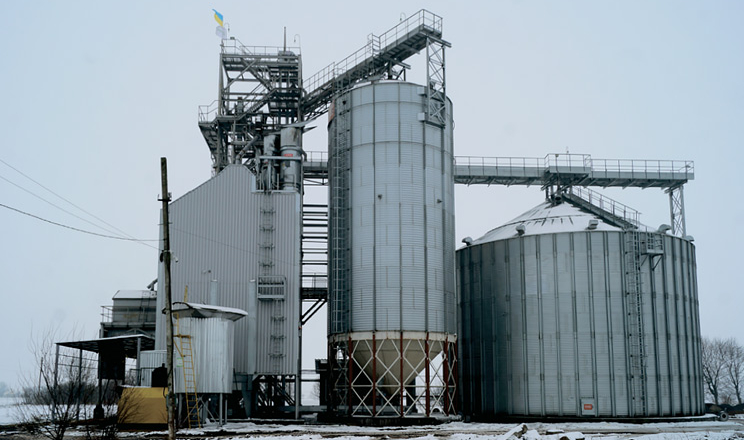
Будівництво фермерського елеватора завжди пов’язано з дефіцитом коштів і неможливістю помилитися під час вибору обладнання
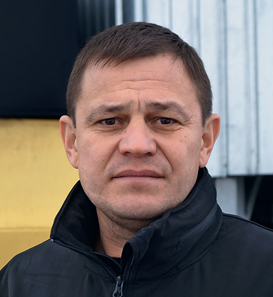
Для невеликого господарства будівництво власного елеватора завжди є непростим питанням. Виникає потреба в один-два роки вкласти чималу суму грошей в об’єкт, який буде окуповуватися тривалий час. При цьому ціна помилки може бути дуже високою, і доводиться постійно балансувати між ціною і якістю обладнання, а також його ефективністю. У ПСП «Злагода» до усього ще додалась проблема енергопостачання: поруч із перспективним місцем будівництва не було газопроводу потрібної потужності, щоб підключити до нього сушарку. Довелось одразу розглядати альтернативні джерела енергії, і в результаті зупинилися на твердому паливі.
Взагалі потреба в елеваторі з’явилась у господарстві не так давно — ще кілька років тому підприємство займалось вирощуванням цукрового буряка і зернових культур ранньої групи. При цьому 80% зернових належали до насінницьких посівів. Відповідно, обсяги зберігання були мінімальними — буряк вивозився на цукровий завод, насіння зернових продавалось перед сезоном сівби озимих і висівалося на власних полях. Із 2000 га кукурудза займала не більше 100 га — збільшувати її частку не дозволяла сівозміна. Однак настав момент, коли прибутковість цукрового буряка відчутно зменшилась, а також скоротився попит на насіння пшениці. Було прийнято рішення відмовитись від цих напрямків і перейти на вирощування кукурудзи і сої. Відповідно, з’явилася потреба у сушінні і зберіганні великої кількості зерна, і наявні потужності не могли задовольнити потреб підприємства. Отже, у 2017 році розпочали проєктування невеликого фермерського елеватора із сушаркою шахтного типу.
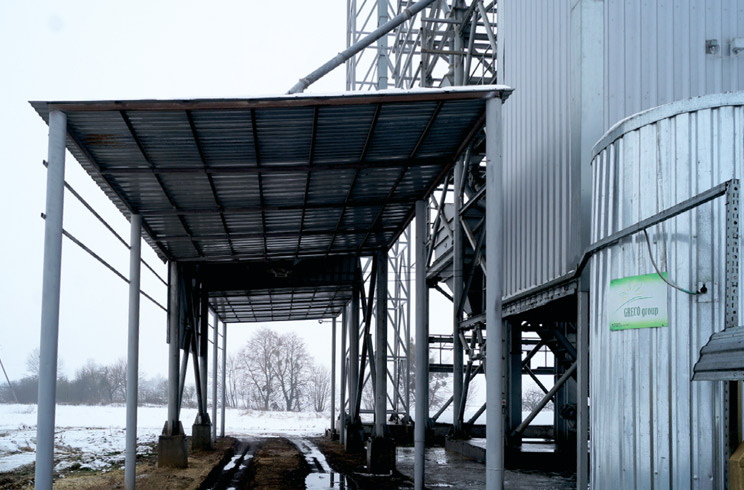
Перші складнощі, з якими довелось зустрітися, — це глинисті ґрунти. Навіть під невеликий силос, сушарку і норійну вежу висотою лише 28 м від поверхні землі довелося спочатку бити палі й лише потім влаштовувати фундаменти. Під усі підземні споруди рили котловани і після бетонування галерей засипку виконували привозним піском — місцеві ґрунти для цього не підходили. Зараз територія елеватора забетонована мінімально, виключно щоб забезпечити більш-менш прийнятні умови роботи. Елеватор працює третій сезон, і тут досі спостерігаються просадки ґрунту. Тому лише наступного року планується привести територію підприємства у більш зручний для пересування людей і техніки стан.
Непрості ґрунтові умови і висока вартість будівництва змусили розбити будівництво на черги. На даний момент разом із приймальним блоком, норійною вежею, хопером для вологого зерна, сушаркою і теплогенератором зведено лише один силос на плоскому днищі на 2000 т із 6 запроєктованих. На елеваторі продовжують використовувати підлогове сховище, яке дає змогу відкласти будівництво інших силосів. Територія підприємства дозволяє також зберігати зерно у пластикових рукавах.
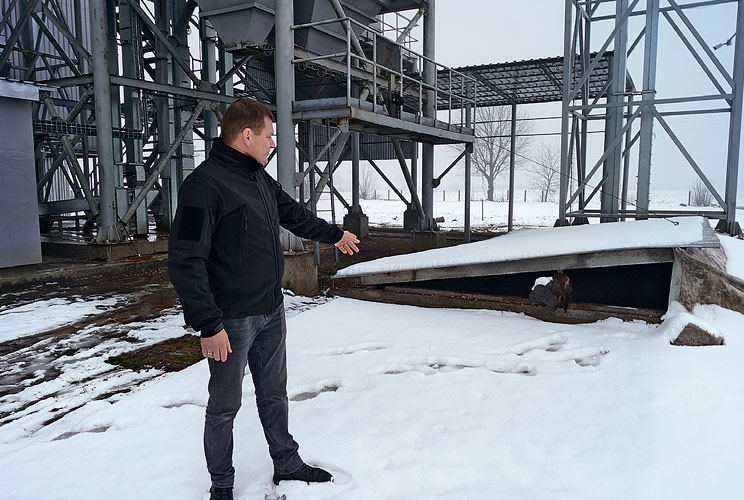
Вибір обладнання відбувався за критеріями наявності усіх компонентів в Україні й доступної ціни. Оскільки для невеликого підприємства будівництво навіть найпростішого елеватора є значною інвестицією, потрібно було знайти оптимальний варіант. І він знайшовся у вигляді пропозиції від вітчизняного виробника KMZ Industries. Власники вивчали схожі проєкти цього виробника у Рівненському регіоні, і зрозуміли, що вітчизняний виробник здатен створити якісне обладнання за прийнятну ціну.
Починаючи від поставки обладнання і монтажу й закінчуючи оцифровуванням елеватора — усе робили спеціалісти KMZ Industries. Це дало змогу не лише пришвидшити виконання багатьох процесів, а й скоротило кількість відповідальних осіб до 3-х. Тепер коли у директора виникає будь-яке питання, він знає, що один із трьох спеціалістів допоможе.
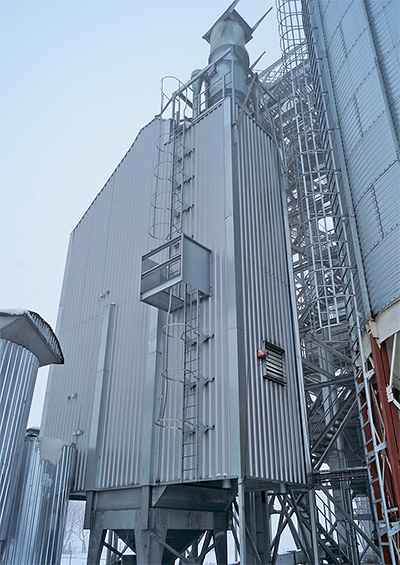
Елеватор будували три компанії. Одна з них виконувала усі бетонні роботи — від завальної ями і до фундаментів під усі будівлі й бетонування частини прилеглої території. Друга компанія виготовила і змонтувала всі металеві конструкції (окрім технологічного обладнання). Причому директор відмітив, що усі елементи були зварені та привезені у готовому вигляді, і на будівельному майданчику ніхто нічого не підганяв і «болгаркою» не підрізав. Усе склали, як конструктор. Технологічне обладнання, відповідно, монтувала бригада KMZ Industries.
Продуктивність приймання елеватора становить 75 т/год. Однак сушарка обмежує загальну продуктивність: практика показала, що кукурудзу з вологістю 32% вдається висушувати до 14% у кількості 220 т на добу. Зі зниженням початкової вологості до 25% продуктивність сушарки зросла до 300 т на добу і навіть вище. На току працює окрема невелика сушарка продуктивністю 100–120 т на добу, тож разом встигають сушити до 400 т на добу. Саме стільки встигає зібрати комбайн за день.
На елеваторі працює невеличка лабораторія, яка визначає основні (механічні) показники зерна та контролює наявність захворювань та шкідників. Для більш складних аналізів зразки возять до сусідів, де є відповідне обладнання. Оскільки обсяги зерна, що надходять на елеватор, відносно невеликі і працюють в основному з власним зерном, такий спосіб визначення якості зерна є достатнім.
Через завальну яму і норії зерно завантажується у вентильований хопер, який вміщує 650–700 т або на очисну машину КБС — теж виробництва KMZ Industries. Зазвичай після власних комбайнів кукурудзу одразу сушать без попереднього очищення. Наймані комбайни традиційно не забезпечують потрібний рівень чистоти, тому зерно спершу чистять і лише потім відправляють на тимчасове зберігання або сушіння. Після сушарки зерно переміщують у силос або у проміжний бункер на відвантаження у підлогове сховище.
Тільки тверде паливо
Сушарка Brice-Baker 10/24 виробництва KMZ Industries на елеваторі працює разом із теплогенератором Greko Group. Із самого початку підприємство не розглядало можливість підключення до газової мережі. Найближча точка підключення розташовується за 2,5 км, тож вкладати скажені кошти у газопровід не було жодного сенсу. Теплогенератор обирали із можливістю працювати на різних видах твердого палива.
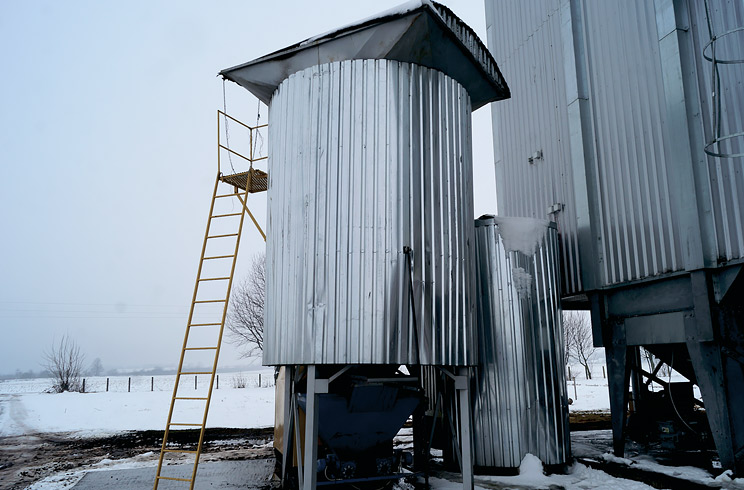
Перше паливо — це щепа. Її виготовляють самостійно за допомогою подрібнювача з обрізків деревного виробництва. Залежно від порід дерева, вологості та інших характеристик витрати на зняття одного тонно-відсотка складають 4,5–7 кг. Відповідно, для зняття 10% на 300 т потрібно до 20 т палива. До щепи підмішують органічні відходи, що лишаються після очищення зерна, у пропорції до 20%. Більше не додають, оскільки стає складно контролювати температуру теплоносія.
Незважаючи на те, що Рівненщина багата на лісові ресурси, цього року в регіоні було неможливо придбати пелети. На початку сезону сушарка працювала на щепі, а пізніше вдалося придбати на Черкащині кукурудзяні пелети, а на Вінниччині — соняшникові.
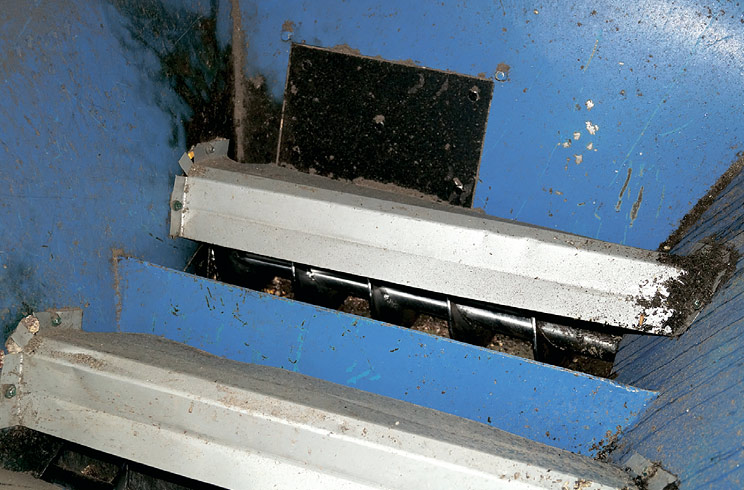
Деревні пелети у господарстві намагаються не використовувати або ж купують їх виключно у надійних постачальників. За три сезони сушіння вже кілька разів стикались із ситуацією, коли для збільшення ваги деревних пелет до сировини додають звичайний пісок, який під дією високої температури починає плавитись у топці і спікається у великі «коржі». Через це доводиться чистити котел кожні кілька годин. Соняшникова пелета згоряє практично без залишку, і за її використання котел чистять раз на кілька днів. Кукурудзяна пелета має такі ж гарні якості, а її ККД взагалі найбільший серед усіх видів твердого пали ва, що використовується господарством. Якщо соняшникової пелети потрібно 5–6 кг на зняття одного тонно-відсотка, то кукурудзяної — менше як 4 кг! При цьому ціна пелет із різних матеріалів відрізняється несуттєво (соняшникова — 4750 грн/т, кукурудзяна — 5150 грн/т).
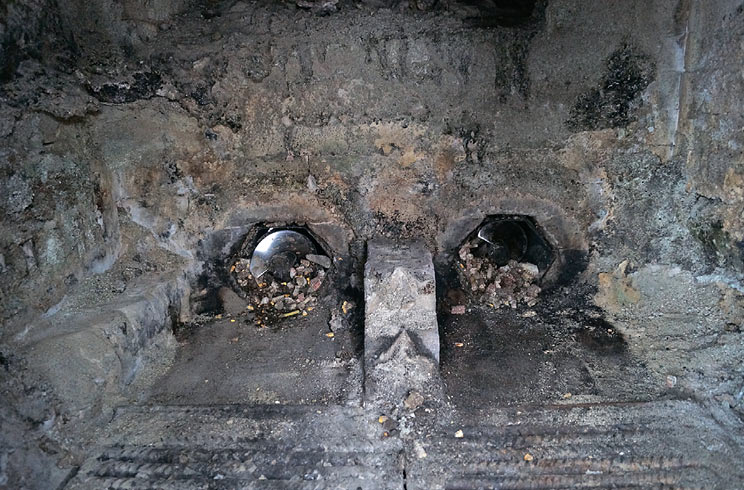
Теплогенератор має оперативну ємність для твердого палива на 12 м3. Якщо використовують пелети, вистачає одного завантаження на добу. Щепу доводиться вантажити кілька разів. Паливо зберігається у підлоговому сховищі (щепа — насипом, пелети — у біг-бегах на піддонах).
До чистоти — особлива увага
Від типу і якості палива залежить частота очищення котла — від кількох разів на день до разу на кілька днів. Процес відбувається досить швидко, тому навіть сушарку не вимикають. Раз на одну-дві доби доводиться чистити і саму сушарку. На це витрачають близько години. В базовій комплектації сушарки не було передбачено спеціальних майданчиків для очищення, і роботи доводилось виконувати у незручних умовах. Щоб спростити цей процес, у KMZ Industries замовили додаткове обладнання, яке дозволяє легко і швидко чистити Brice-Baker без жодної небезпеки для персоналу.
Процес очищення виглядає так: перекривають подачу гарячого повітря, верхнім витяжним вентилятором видаляють гаряче повітря, працівник піднімається всередину, чистить сушарку, після чого продовжують сушіння. Особливу увагу до очищення необхідно приділяти під час сушіння кукурудзи із високою вологістю, коли лушпиння швидко налипає на внутрішні стінки сушарки і провокує подальше інтенсивне накопичення решток. Відповідно, утворюються потенційно небезпечні місця для загоряння органічної маси. Окрім того, легкі рештки кукурудзи швидко налипають на лопатях вентиляторів, і їх також необхідно періодично чистити. У господарстві це роблять не рідше разу на тиждень, оскільки мають досвід розбалансування лопатей. Незначна вібрація швидко перетворилася на голосний гуркіт, і в результаті довелось демонтувати вентилятор і по новій балансувати лопаті. Добре, що це вдалося зробити швидко, і сушарка простояла мінімальний час. Допоміг спеціаліст монтажної служби KMZ Industries: по телефону він чітко керував усім процесом відновлення — від демонтажу до найскладніших операцій із налаштування. За словами директора елеватора Володимира Степанчука, така допомога є чи не найціннішим у співпраці з KMZ Industries. У будь-який час можна розраховувати на підтримку, і це дає впевненість у безперебійній роботі підприємства в розпал сезону.
Керування
АСУ ТП (автоматизована система управління технологічним процесом), яку на елеваторі також проваджували спеціалісти KMZ Industries, дозволяє працювати в повністю автоматичному режимі, щоб мінімізувати вплив людського фактору на якість роботи. Проте усе може працювати і в ручному режимі, коли немає інтернету або інші причини впливають на працездатність автоматики. Нічого складного у цьому немає, оскільки схема елеватора досить проста. Тут немає сотень маршрутів, і зерно переміщується за допомогою кількох горизонтальних транспортерів і 5 норій. Навіть із задіяними сушаркою і теплогенератором роботи для операторів небагато. Автоматика слідкує, щоб параметри не вийшли за допустимі межі, і за потреби одразу сигналізує про можливі негаразди. Таким чином можна вчасно зреагувати на проблему і вирішити її швидко і з мінімальними витратами.
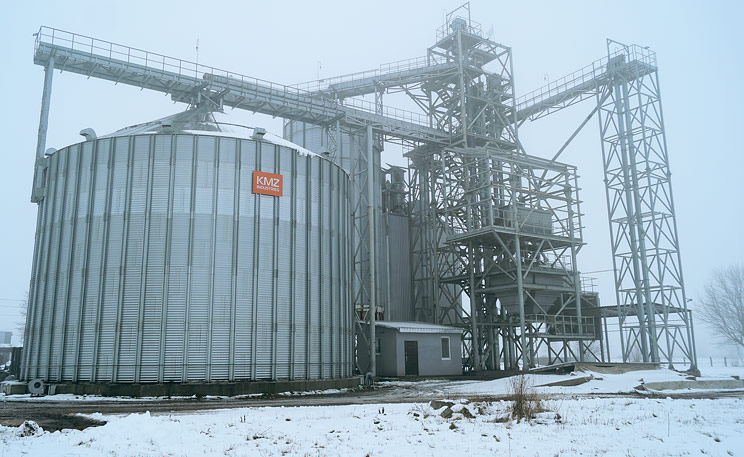
Силос оснащено кабельною термометрією на 7 кабелів. Також у хопері встановлено один кабель, щоб мати розуміння про ситуацію із зерном. Крім того, силос обладнано аераційними вентиляторами, які використовуються вкрай рідко. Враховуючи, що силос лише один, і перевантажувати зерно у разі початку процесів самозігрівання нікуди, доводиться «прокручувати» зерно через транспортні системи і завантажувати назад у силос. На крайній випадок можна задіяти власний автотранспорт і перевезти зерно до підлогового сховища або запакувати в пластикові рукави.
ГОВОРЯТЬ ЕКСПЕРТИ
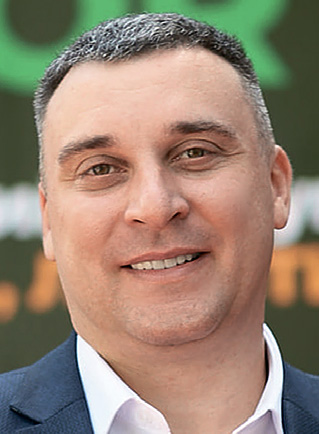
В’ячеслав Степанчук, директор із будівництва та монтажу KMZ Industries
— Монтаж елеватора клієнт від початку замовив у нашого заводу. Тут було залучено 15 наших монтажників, а зведення усього комплекту обладнання на об’єкті ми здійснили за 3 місяці.
Замовник отримав впевненість у правильності монтажу і розширену трирічну гарантію на наше обладнання. Завдяки участі нашого спеціаліста вдалося вирішити і озвучену проблему з вентилятором — так вдалося уникнути тривалого простою сушильного обладнання. Для елеваторів, особливо фермерських, де немає можливості утримувати ремонтників, — це дуже важливо мати таку підтримку в подібних ситуаціях, особливо коли в гарячу пору простої вкрай небажані.
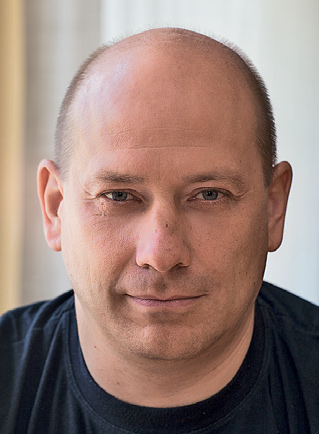
Олексій Ломакін, керівник департаменту автоматизації та електрифікації KMZ Industries
— ПСП «Злагода» — дуже вдалий приклад типового фермерського елеватора: акуратний, компактний, із базовим набором необхідного обладнання: сушарка, хопер, силос, сепаратор, транспорт — нічого зайвого. Понад 70% наших замовлень на автоматизацію за останній рік — це саме такі фермерські елеватори, які зараз добре розуміють переваги впровадження АСУ ТП, зокрема в умовах дефіциту кадрів на зерносховищах, і одразу включають її як обов’язкову у вартість зведення об’єкта.
Автоматизація «Злагоди» включала сушарку, управління транспортними маршрутами (їх тут справді небагато) і також термометрію в силосах — усі показники ми вивели на екран в операторській для керування зерносховищем з єдиної точки. Для автоматизації використовували власну програму, на нашому підприємстві виготовляли також і шафи управління.
До речі, оскільки сушарку Brice-Baker ми одразу продаємо лише автоматизованою і вона вже має встановлене програмне забезпечення власної розробки нашого заводу — то загальну автоматизацію елеватора ми зробили на її базі (використовуючи один промисловий контролер). Це прискорило процес і допомогло власнику заощадити на придбанні стороннього ПЗ.
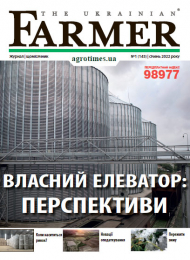