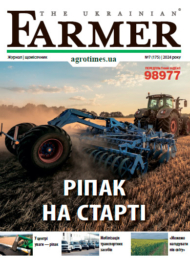
Робота кожного елеватора має власні особливості, які відбиваються на всіх аспектах експлуатації — від приймання до відвантаження
Адаптуючись до реалій
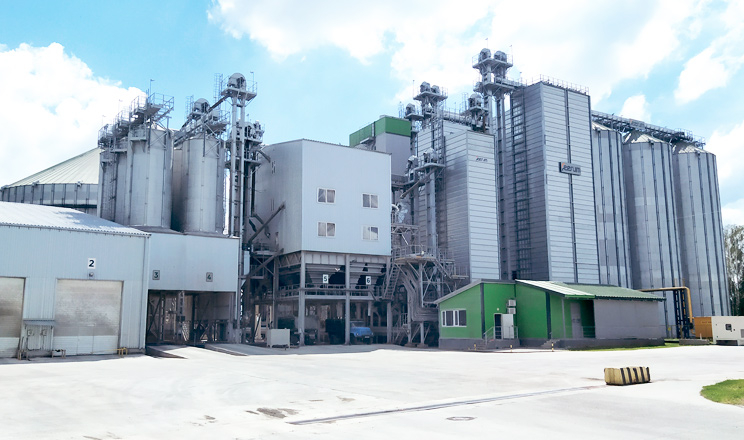
Робота кожного елеватора має власні особливості, які відбиваються на всіх аспектах експлуатації — від приймання до відвантаження.
Коли ринок змушує аграріїв кардинально трансформувати сівозміну, вони це роблять не вагаючись. Однак разом із виробничими підрозділами доводиться й елеватори готувати до роботи в нових умовах. Саме за таких обставин можна побачити гнучкість підприємств зберігання, та чи легко їм адаптуватись до нових викликів. Це — своєрідний іспит, який надає можливість оцінити як будівельників і проєктантів, так і експлуатаційну службу.
Вистояти й працювати далі
У компанії «Епіцентр Агро» цього року від кукурудзи практично повністю відмовились, зробивши ставку на олійні культури — ріпак і соняшник. Кукурудза на сьогодні не дає потрібної «економіки», й до того ж логістичні ризики є актуальними, попри активну роботу портів Великої Одеси. Саме тому ми завітали на елеватор «Переробник», що на півдні Київщини, щоб дізнатись, як підприємство впоралось із проблемами перших років війни та як готується до нових умов роботи.
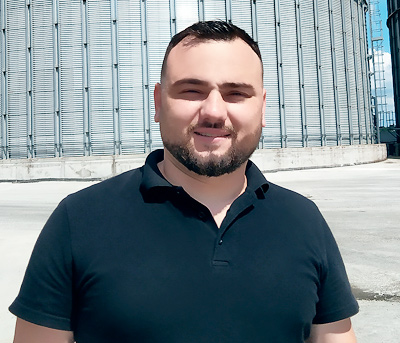
Євгеній Маринін, директор підприємства, розповів, що припинення морських перевезень сильно «вдарило» по експортних можливостях. Подекуди зерно зберігали більше як рік, що впливало на собівартість і нарощувало втрати в умовах низьких цін на продукцію. Незважаючи на відверто «страшну» економіку, доводилось утримувати підприємство у відповідному технічному стані. Це вдалось зробити, і тепер елеватор працює та вдосконалює свою роботу.
«Прокачати» елеватор
Як відомо, жоден елеватор не будували так, щоб після початку експлуатації не доводилось щось удосконалювати. Певною мірою так сталось і тут. Добудовували маршрути, оптимізували транспортне обладнання, розпочалась робота з автоматизації внутрішньої логістики. Нині в планах керівництва — довести все до того рівня, коли удосконалення покращать основні показники: оперативність приймання, собівартість доробки й зберігання, а також спростять більшість виробничих процесів. Хоча вже на сьогодні можна говорити про помітні зрушення в бік оптимізації. Наприклад, минулого сезону понад 120 тис. Тонн відвантажили протягом п’яти місяців. І це враховуючи, що елеватор не має залізничного відвантаження! За 15 год відвантажували понад 100 вантажівок. Наразі триває робота з автоматизації приймання, щоб зменшити час простоїв автомобілів і скоротити тривалість операцій усередині підприємства.
Оптимізація внутрішньої логістики
На в’їзді нині водії послуговуються електронними картками, що ідентифікують транспортний засіб і дозволяють подальший рух. Працює світлофорне регулювання, але в найближчих планах — зробити розмітку і встановити шлагбауми й інформаційні табло, які вказуватимуть напрямок руху для певного автомобіля. Це зменшить витрати часу на внутрішню логістику й спростить «життя» водіям. Наприклад, якщо картка «не відкриває» шлагбаум до завальної ями, це означатиме, що автомобіль прямує не на ту завальну яму. Навіть для тих, хто приїздить до елеватора вперше, не буде можливості заблукати й помилитись із маршрутом.
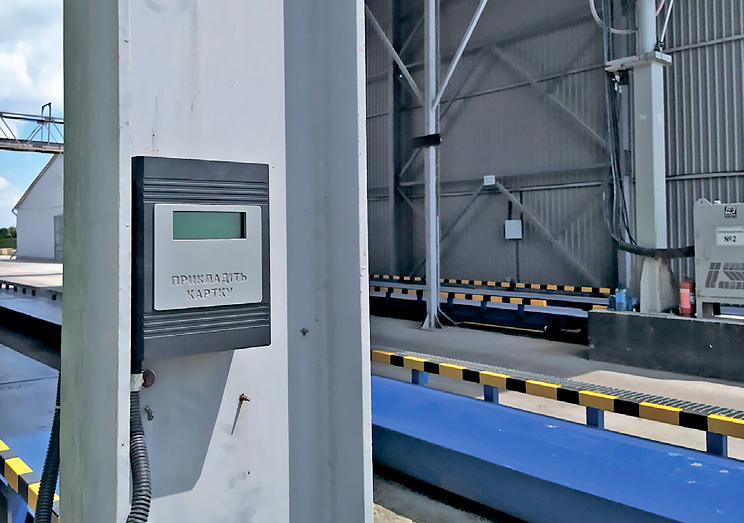
Тестується робота електронної черги, яка значно зменшує простої вантажівок. Таким чином, тільки на логістиці компанія зможе заощадити значні кошти й покращити загальну ефективність приймання й відвантаження зерна.
Насамперед — контроль
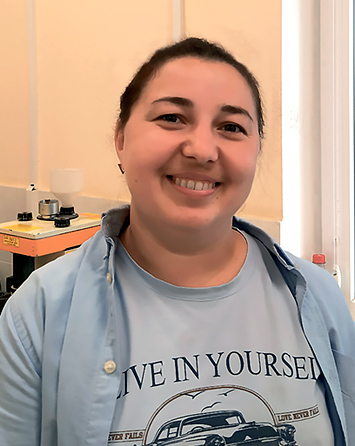
Лабораторія стоїть на сторожі інтересів компанії й однакового ретельно контролює як власне, так і давальницьке зерно. В останні роки частка останнього зменшилась, але нині компанія планує залучати більше сторонньої продукції. Наприклад, цього сезону точно прийматимуть пшеницю, соняшник, ріпак і сою. Упродовж сезону в лабораторії постійно працюють п’ять фахівців. Коли триває активне приймання, для перепочинку не лишається й хвилини. І навіть після того, як збирання завершується в кінці дня, елеватор працює й далі, а разом із ним і лабораторія: відбирають зразки на кожному етапі доробки й закладають на зберігання, підсумовують результати дня. Зміна триває добу, тож лаборантам доводиться працювати не менше за інших спеціалістів. За словами заступниці завідувача лабораторії Ганни Сірош, у сезон активного приймання машину з кукурудзою пропускали за 6–7 хвилин.
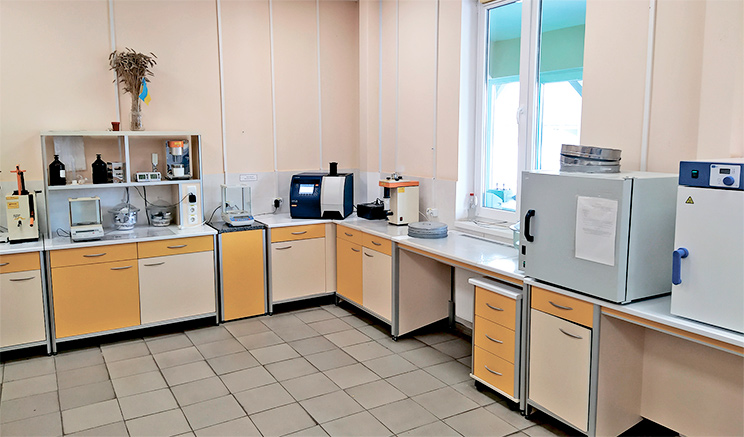
Цього сезону очікуються олійні культури, тому аналізи триватимуть довше. Нині відпрацьовують алгоритм, за яким можна було б максимально оптимізувати цей процес. Наприклад, коли зерно надходитиме з одного поля, визначатимуть тільки «швидкі» показники, а ті, що потребують більше часу, робитимуть не для всіх машин, або робитимуть із запізненням, щоб розуміти, що реально є в силосі.
Приймання без затримань
Дві завальні ями розраховано на одночасне приймання по 60 «кубів», що дозволяє приймати 3–4 машини підряд. Транспортне обладнання має продуктивність 175 т/год, тому елеватор за добу реально встигає приймати понад 3000 т. На етапі проєктування більшість транспортерів запланували стрічкового типу. Вибір такого типу транспортного обладнання базувався на економічності й ощадності до зерна. Проте практика показала, що разом із перевагами є й недоліки, які певною мірою ускладнювали роботу підприємства в критичні моменти. Тому було вирішено замінити стрічкові транспортери на ланцюгові. «Стрічка» лишилась тільки в підсилосних галереях, щоб менше травмувати зерно перед відвантаженням.
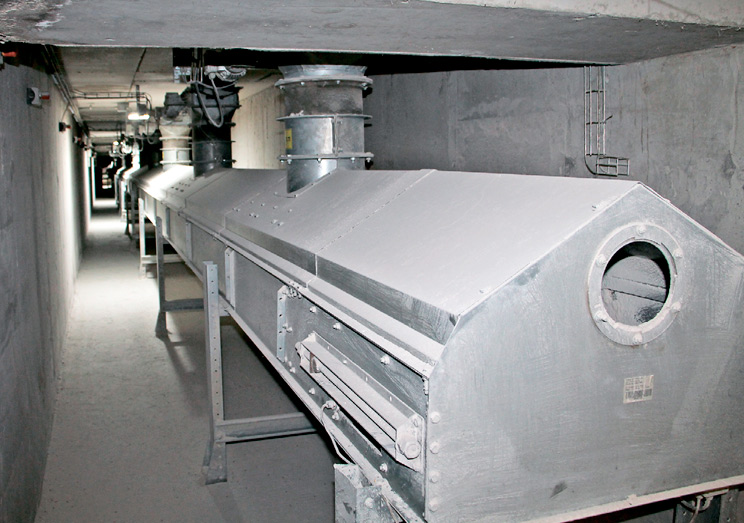
Попереднє очищення відбувається на двох барабанних сепараторах OLIS ЛУЧ ЗСО-200. Вони добре виконують свою роботу з будь-якими культурами, і питань щодо якості очищення або продуктивності не виникало. За потреби оператори міняють решета й проводять сервісні роботи. Упродовж п’яти сезонів підприємство перевалило близько 700 тис. тонн, і за цей час машини показали, що здатні ефективно працювати в різних умовах.
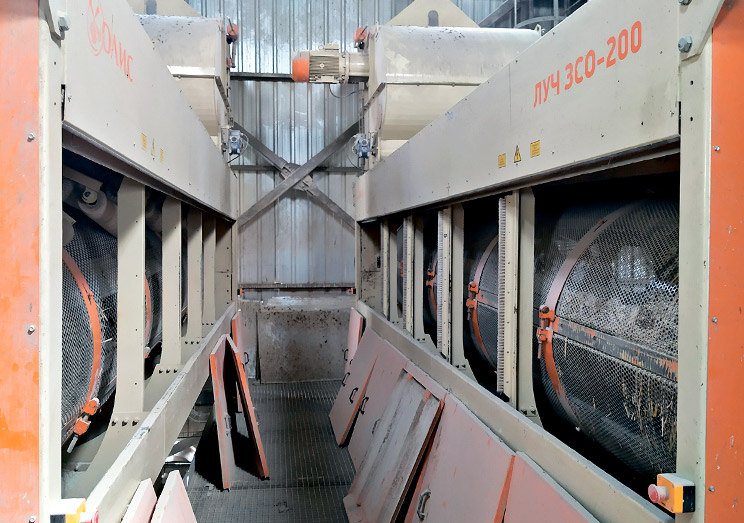
Доведення зерна до базових показників за чистотою виконують на плоскорешітних сепараторах Buhler TAS 206. Це саме та гарантія якості, що потрібна для виконання умов експортних контрактів. Кожен керівник елеватора погано спить у сезон, але коли він знає, що перед відвантаженням зерно пропускають через сепаратори Buhler, це додає впевненості й спокою. Однак у «Переробнику» машини TAS 206 нерідко чистять соняшник перед сушінням. Виробники сушарок радять цю культуру сушити якомога чистішою, щоб не допустити залягань і не сприяти загорянням.
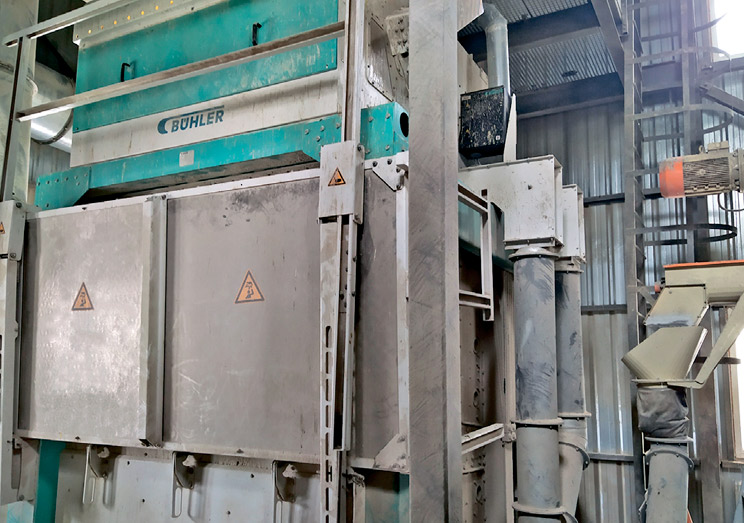
Зерно накопичують у шести хоперах по 1100 т кожен. Тут вирівнюється волога, і за потреби можна увімкнути активне вентилювання. Обсягу накопичення вистачає для роботи сушарок протягом доби-двох залежно від вологості зерна й погодних умов.
Переваги каскадного сушіння
На підприємстві застосовано досить ефективну схему каскадного сушіння. Тут працюють дві потужні сушарки FEERUM у парі з меншими — LAW і FEERUM. Це ефективно охолоджує зерно й видаляє залишкову вологу активним вентилюванням у менших сушарках, не підігріваючи повітря. Коли доводиться знімати тільки кілька відсотків вологості, як великі, так і малі сушарки працюють без використання газу. Взагалі каскадна схема з достатньою кількістю маршрутів робить підприємство максимально гнучкім щодо сушіння. Залежно від типу культури й вологості можна використовувати тільки одну або обидві сушарки з пари, а також обирати потрібні режими їх роботи. Результатом стає зменшення собівартості сушіння або покращення продуктивності процесу. Практика показала, що для зняття тонно-відсотка вологості достатньо витратити 1,1–1,2 м³ газу (по кукурудзі з вологістю до 26%).
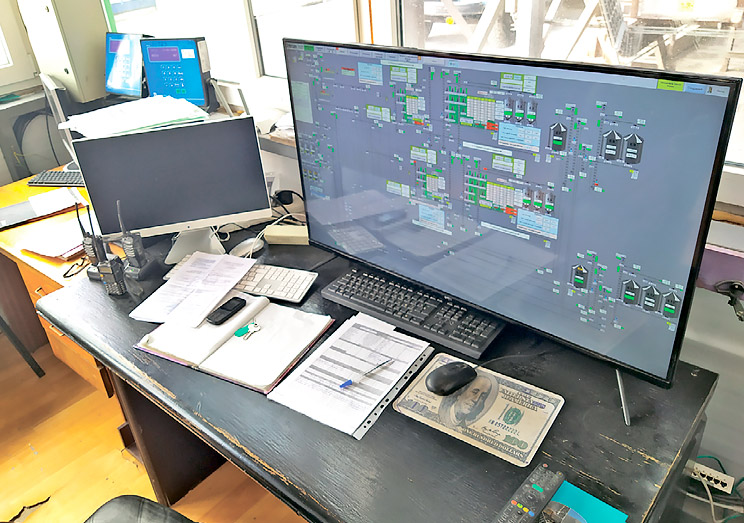
Перші роки експлуатації сушарок FEERUM показали переваги й недоліки цього обладнання. Тут — хороший метал, але немає драбини й галереї для обслуговування (очищення). Наприклад, щоб очистити гарячу зону, доводиться викликати альпіністів. Холодна зона має конструктивні елементи, якими можна скористатися як сходами, але це також не зовсім зручно й безпечно. Нині вирішується питання оснащення сушарок додатковими конструкціями, які б спростили їх очищення.
У силосах і рукавах
Компанія FEERUM поставила не лише сушарки й транспортне обладнання — силоси також її виробництва. Нині на території підприємства збудовано сім силосів по 15 тис. тонн. Незважаючи на великий діаметр, конструкція силосів достатньо міцна. Під час експлуатації виявили й недолік — слабку підвіску кабельної термометрії. Тепер працюють над удосконаленням кріплення — треба зробити так, щоб кабелі добре тримались і водночас від перевантажень не пошкодити конструкцію даху.
Ураховуючи великий діаметр силосів, було цікаво, як працюють зачисні шнеки. Виявилось, що тут також не обійшлось без ускладнень: опорні підшипники швидко зносились, і їх довелось замінити на фторопластові втулки. Виготовили деталі самостійно, і після успішних випробувань на одному силосі замінили в інших.
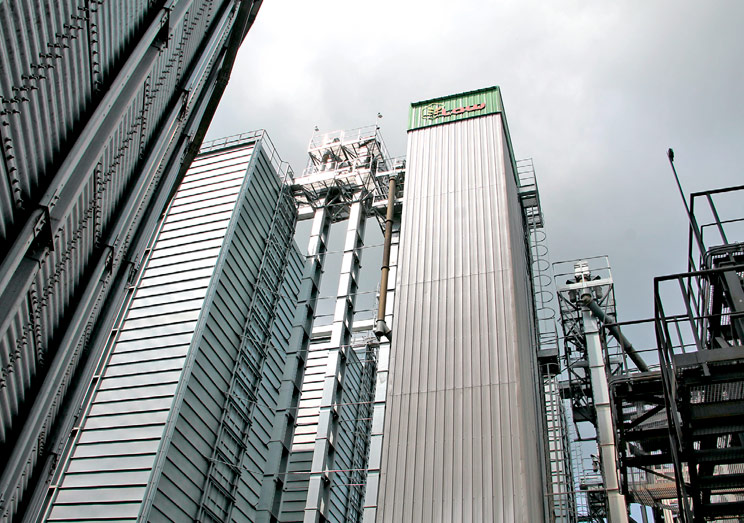
Досвід тривалого зберігання показав, що без фумігації зерна втримати якість на належному рівні буває складно. Для запобігання псуванню продукції вирішили застосовувати хімічні препарати, якими обробляють зерно під час закладання на зберігання. Було придбано відповідне обладнання, яке встановлюють на потрібну норію. За потреби обладнання можна швидко перемістити. Встановлення потребує мінімум часу, для цього треба зробити отвір у корпусі норії й уставити туди форсунку. Препарати купують у компаній «Сожам». Вони довели свою ефективність — зерно зберігається без проблем шість місяців і довше. За словами керівника елеватора небулізація дає змогу не заглядати в силос тривалий час і бути впевненим у якості продукції.
Експортні обмеження 2022–2023 рр. змусили підприємство зберігати близько 45 тис. тонн зерна в рукавах. Для цього використовували майданчики поруч із елеватором, а також на віддалених локаціях. Незважаючи на те, що доводилось постійно перевіряти якість, і шкідники періодично пошкоджували рукава, зерно нормально зберегли аж до того моменту, коли звільнились місткості елеватора. Зберігали зерно за вологості до 20% протягом 2–4 місяців, і проблем із якістю не виникало.
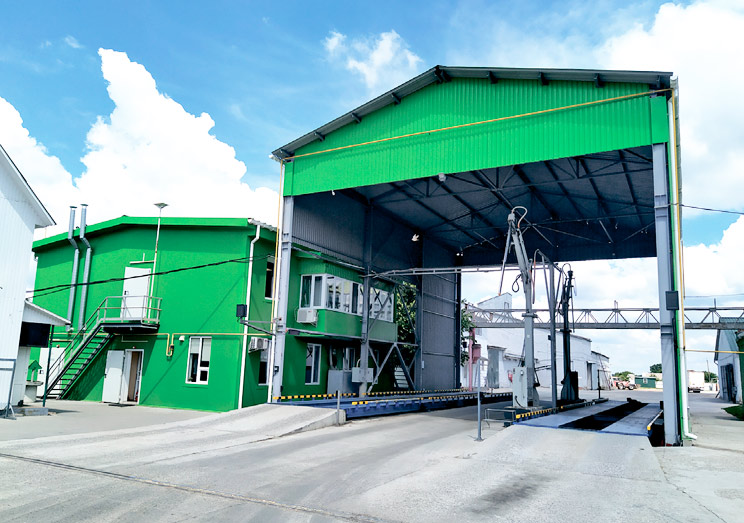
Відвантажують продукцію двома окремими лініями. Кожну з них оснащено накопичувальними бункерами й автомобільними вагами. Завдяки цьому оператор бачить загальну вагу й не випустить автомобіль із перевантаженням.
Регламенти й удосконалення
Євгеній Маринін розповів, що основним завданням на цьому етапі роботи підприємства є підтримка обладнання в робочому стані. Для цього багато зусиль спрямовують на виконання регламентних робіт, а також підготовку критичних вузлів та елементів до нового сезону. Коли вдається відпрацювати без зупинок, компанія не втрачає кошти через простої вантажівок і комбайнів, затримки суден у портах, псування продукції тощо. Тому підготовка обладнання є головним аспектом експлуатації.
За роки роботи довелось замінити частину редукторів і електромоторів на надійніші. Цей досвід показав, на чому економити не варто. Проте система керування елеваторним обладнанням й досі є взірцевою. Вона зручна й інформативна, і навіть має різні варіанти візуалізацій певних процесів. Оператор не втомлюється дивитись на величезний монітор, і впродовж зміни все під контролем. На цей момент відбулась низка модернізацій і дообладнання, з’явились нові маршрути, які поки що працюють у ручному режимі. Найближчим часом їх додадуть до системи керування, що зменшить навантаження на операторів.
Серед обладнання, що швидко зношується, на першому місці — самопливи. Певні ділянки доводиться періодично міняти, особливо там, де великі кути повороту або висока швидкість руху зерна. Футерування допомагає, але не завжди є можливість захищати метал поліуретаном. Залежно від ступеня зношення елементи самопливів ремонтують або міняють.
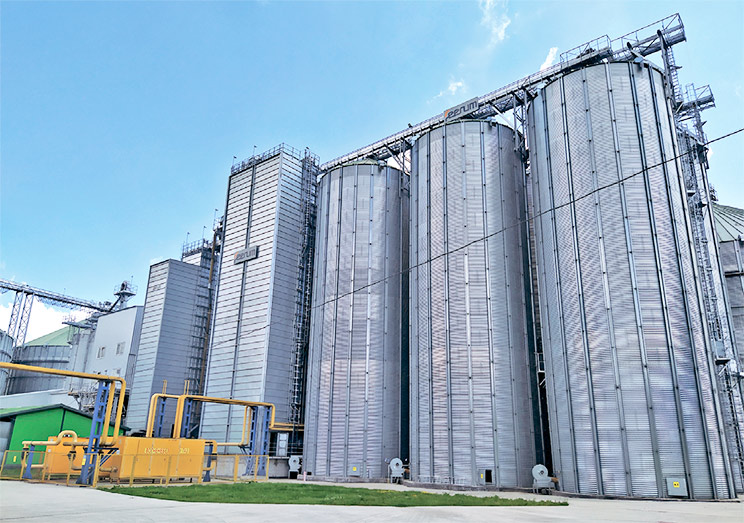
Перспектива
Підприємство спрямовує зусилля на забезпечення насамперед власних потреб у доробці й зберіганні агропродукції. Проте в умовах експорту тут є великий потенціал до залучення давальницького зерна від місцевих виробників. На перший погляд, відсутність залізниці може видаватись обмежувальним чинником, але насправді автомобільне сполучення з портами Великої Одеси є досить зручним і недалеким — до 350 км. Крім того, автотранспорт на такій відстані може відпрацювати оперативніше, і це є чималою перевагою проти залізниці.
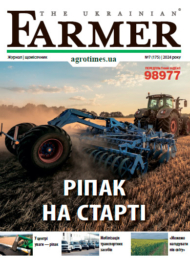