Сушіння зерна потребує чималих витрат і тому змушує аграріїв шукати альтернативні джерела теплової енергії.
Секрет економного сушіння
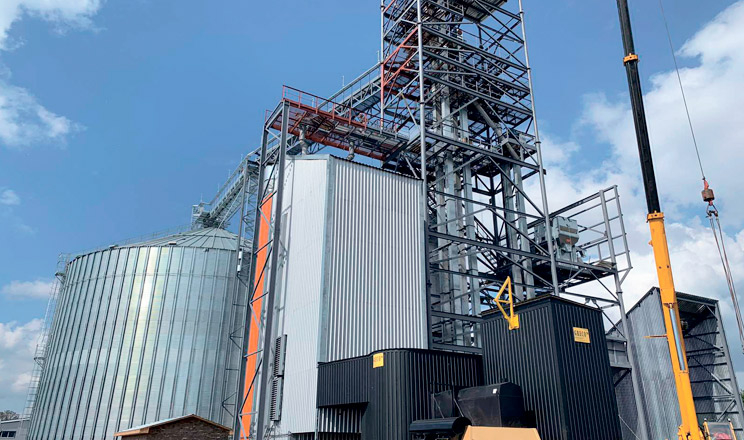
Сушіння зерна потребує чималих витрат, і тому змушує аграріїв ретельно рахувати гроші й шукати альтернативні джерела теплової енергії.
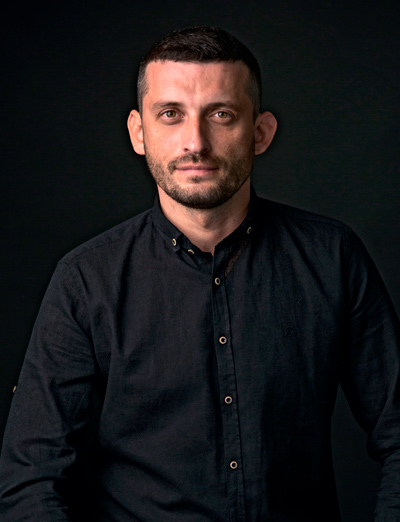
Собівартість аграрної продукції є основним чинником, що впливає на заробітки аграріїв. Зменшити витратну частину можна багатьма шляхами, і один із них — це дешеве паливо.
Останні 5–6 років природний газ перестав бути стабільним щодо ціни, і нерідко собівартість зняття тонно-відсотка вологості перевищувала 150 грн. Крім того, з газом працювати не завжди зручно. Важко наперед сказати, якою буде осінь і скільки доведеться сушити, а ліміти потрібно замовити заздалегідь. Усе це підштовхує аграріїв до пошуку альтернативних джерел енергії, які б конкурували за ціною і доступністю з газом.
Ми поспілкувались із генеральним директором компанії Greco Group Іваном Корженком, який розповів про сучасні тренди в альтернативній теплогенерації для сушіння зерна.
— Чому відмовляються від газу?
— Насправді тут кілька причин, і кожна з них є критичною. З року в рік ціна на газ суттєво змінюється, і неможливо вгадати, коли буде вигідно працювати з цим паливом, а коли — ні.
Кожен бізнесмен хоче прогнозованості, а з газом — це лотерея. Крім того, існують чисто організаційні труднощі, як ліміти й бюрократія підключення. Наприклад, підприємство може швидко побудувати елеватор, але підвести газ до початку сезону не встигає. Що у такому разі робити? Пропускати сезон? З лімітами також ситуація складна — буває досить складно передбачити обсяги сушіння, а постачальники газу вимагають точних цифр заздалегідь. Розв’язати проблему можна тільки альтернативними джерелами енергії. Щодо повної відмови від газу як природного, так і скрапленого, я б не радив цього робити. Їх можна лишити як запасний варіант, а за відповідної цінової ситуації використовувати, як основне паливо.
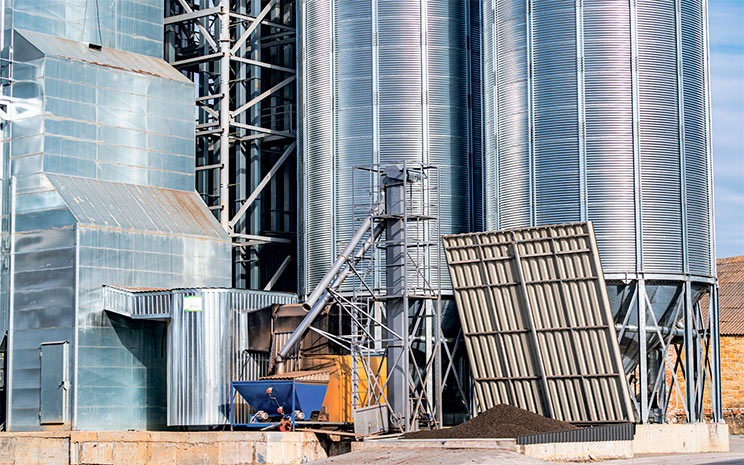
— Які варіанти альтернативної енергії для сушіння зерна набули поширення в Україні?
— Це скраплений газ і тверде паливо, хоча отримати економічну перевагу, порівнюючи з природним газом, вдається тільки використовуючи тверде паливо. Проте й тут потрібно уважно вивчати ефективність різного обладнання: з одними теплогенераторами можна досягти витрат палива на рівні 2 кг на тонно-відсоток вологості, а з іншими — понад 10 кг. Наприклад, у теплогенераторах виробництва Greco Group застосовується технологія піролізного двофазного горіння, що забезпечує високий ККД і низьку собівартість сушіння на рівні 8–12 грн за тонно-відсоток по кукурудзі. Далі замовник може обрати потрібну модель: теплогенератор прямої дії, з напівтеплообмінником або повноцінним теплообмінником. Кожен варіант має свої переваги й недоліки, і тут усе залежить від потреб і умов роботи. Близько 95% замовників обирають теплогенератори з напівтеплообмінником — це найбільш високопродуктивна серія.
— Більшість теплогенераторів доводиться встановлювати на вже робочі об’єкти. Чи складною є інтеграція?
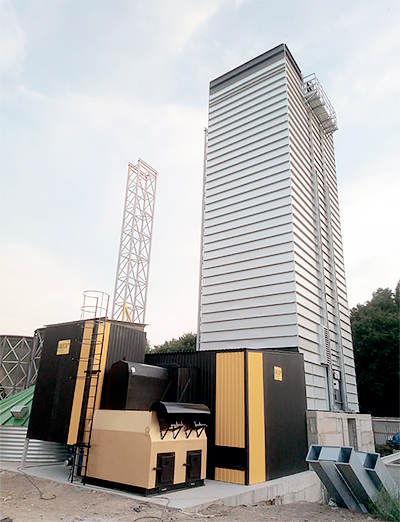
— Багато хто пов’язує теплогенератор із додатковим персоналом і брудними процесами. Проте для наших рішень додатковий персонал не потрібен. Ми широко застосовуємо автоматизацію, а як додаткове оснащення пропонуємо віддалене керування. Це стосується як невеликих «фермерських» теплогенераторів на 3 МВт потужності, так і 20-мегаватних, які працюють на пелеті, щепі, зернових відходах й інших сипких матеріалах. Віддалений доступ надає змогу контролювати роботу теплогенератора, виявляти невідповідності й оперативно втручатись у налаштування, коли це справді потрібно. Наприклад, для великих агропідприємств, у яких одночасно працюють кілька теплогенераторів у різних локаціях, важливо мати змогу стежити за процесами в усіх місцях одночасно.
Теплогенератори приєднуються практично до будь-яких сушарок, і блок керування сушарки «сприймає» теплогенератор як газовий пальник. Автоматика зернової сушарки керує генератором як пальником. Конструкцію теплогенераторів розроблено так, щоб вона охоплювала мінімум простору. Нерідко це відіграє вирішальну роль, коли підприємство хоче перейти з газу на тверде паливо й для встановлення додаткового обладнання практично немає місця.
— Як піклуєтесь про безпеку експлуатації Ваших теплогенераторів?
— Оскільки практично вся небезпека виникає внаслідок дії людського чинника, ми постійно зменшуємо його вплив на роботу нашого обладнання. Наприклад, установили програмне блокування, яке не дає оператору вносити небезпечні зміни в налаштування. Теплогенератори не потрібно щодоби зупиняти на очищення. У деяких випадках очищення потрібно робити раз на 3–4 тижні. Проте ми все ж радимо робити очищення теплогенератора кожні 5–6 днів під час роботи з кукурудзою й синхронізувати цей процес з очищенням сушарки. Під час сушіння соняшнику сушарку варто очищувати щодоби. Люди часом нехтують цими вимогами, хоча потрібно завжди пам’ятати, що зернова сушарка є потенційним джерелом небезпеки, і немає значення, з яким джерелом тепла вона працює.
— Скільки часу потрібно для виготовлення й монтажу теплогенератора?
Це може здаватись нереальним, але ми маємо досвід виконання замовлення протягом двох тижнів. Це і виготовлення, і монтаж. Коли вводимо в експлуатацію, замовник остаточно розраховується. Інші виробники на це витрачають 2–3 місяці, а іноді й значно більше. У чому відмінність? Зазвичай після отримання замовлення і передплати виробник закуповує матеріали або бере їх із власного складу і починає виготовляти обладнання «з нуля». Ми ж маємо кілька переваг. Наші теплогенератори маю модульну конструкцію, що дозволяє використовувати певні елементи для моделей різної потужності. Крім того, найпопулярніші моделі ми маємо на складі. Для цього вкладаємо власні кошти в склад матеріалів і виробництво, але ми можемо запропонувати надшвидке рішення, якого ніхто не має. Зазвичай, коли ми отримуємо замовлення, нам доводиться виготовляти тільки повітряні канали, оскільки їх конфігурація і розміри на кожному об’єкті різні.
— Чи працює з Вашим обладнанням програма державної компенсації?
— Так, наша компанія входить до переліку вітчизняних виробників, на обладнання яких держава надає 25% компенсації. Її нараховують на суму угоди без ПДВ. Хочу зауважити, що далеко не всі виробники подібного обладнання входять до цього переліку, і я раджу перевіряти це ще до укладання угоди. Щоб отримати компенсацію, замовник після укладання угоди й оплати повної суми подає документи, що підтверджують придбання обладнання вітчизняного виробництва, одному з уповноважених банків. Там перевіряють документи, і потім 25% суми без ПДВ повертають замовнику.
Дякуємо за розмову!
Володимир Василенко