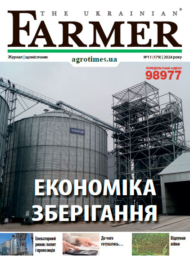
Обережне інвестування у власні елеватори дає змогу поступово збільшувати потужності й оновлювати обладнання без зайвих втрат
Стратегія успіху
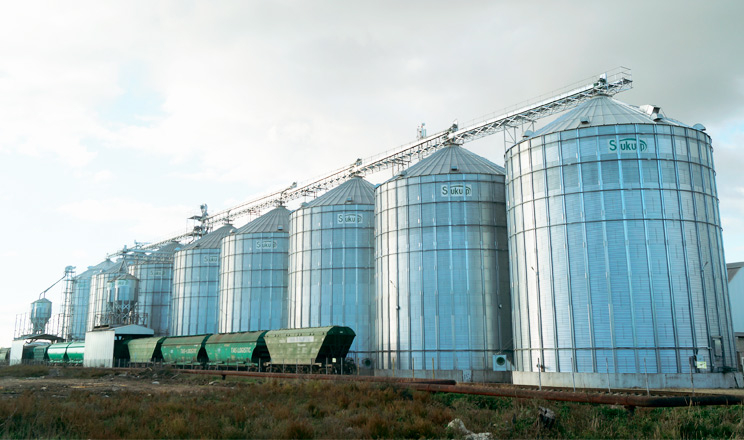
Обережне інвестування у власні елеватори дає змогу поступово збільшувати потужності й оновлювати обладнання без зайвих втрат.
Структура будь-якого великого агровиробника передбачає наявність власних елеваторних потужностей, які б повною мірою забезпечували потреби в доробці й зберіганні зернової продукції. Без цього розраховувати на нормальну ефективність бізнесу важко. Проте й будівництво елеватора завжди пов’язано з пошуками оптимальних технологічних рішень і обладнання, тому що від цього залежать терміни окупності й ефективність роботи об’єкта.
У компанії «Волинь-Зерно-Продукт» під час створення елеватора у Луцьку ухвалювали багато нестандартних рішень, спрямованих на зменшення вартості будівництва без втрати продуктивності та якості роботи. Підприємство працює понад 10 років, тож тепер можна оцінити, чи все було зроблено правильно.
Три в одному
Коли 2012 року починали будувати елеватор, підприємство обробляло значно менше земель, і, відповідно, обсяги виробництва аграрної продукції були меншими. Однак будівництво починали з розрахунку на поступовий розвиток, тому майданчик обрали з хорошим потенціалом. Така інвестиція виявилась виправданою, що дало змогу поступово нарощувати потужність елеватора. Нині тут побудовано три черги, кожна з яких являє собою окремий елеватор із завальною ямою, блоком очищення, сушаркою, хоперами, силосами й точкою відвантаження. Тільки ваговий комплекс і лабораторія працюють одночасно для всіх потужностей. Такий підхід дав змогу інвестувати в будівництво поступово, відповідно до тих обсягів зерна, з якими доводилось працювати.
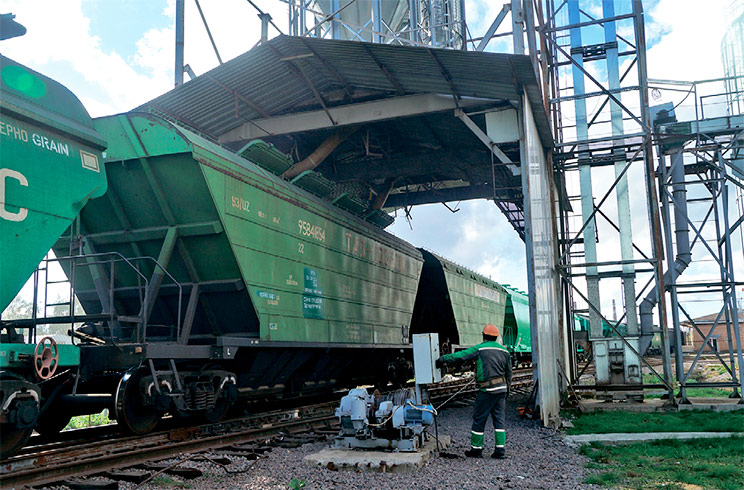
Саме будівництво також намагались оптимізувати. На підприємстві завжди працювало багато кваліфікованих спеціалістів, і це дало змогу залучити їх до виготовлення металоконструкцій і навіть частини обладнання. Це значно скоротило витрати на його придбання, і водночас елеватор не втратив у своїх характеристиках. Наприклад, частина транспортного обладнання власного виробництва працює й досі. Це саме стосується накопичувальних місткостей у точках автомобільного відвантаження — їх виготовили із залізничних цистерн. І хоч вони мають незвичний вигляд, свою функцію виконують на відмінно вже понад 10 років.
Покрокова стратегія
На сьогодні потужність одночасного зберігання становить 125 тис. тонн, а обсяг перевалювання — близько двох обертів на рік. З ранньою групою доводиться відпрацьовувати швидше, щоб звільнити потужності під приймання пізніх культур. Їх, залежно від ситуації, можна зберігати від кількох місяців до пів року і довше.
Аграрні компанії господарства обробляють близько 55 тис. гектарів, і кількість власної продукції доволі велика. Однак підприємство активно приймає давальницьке зерно й завдяки йому подвоює обсяг перевалювання. Елеватор приймає ячмінь, ріпак, пшеницю, жито, сою, соняшник і кукурудзу. Також можуть приймати інші культури — за індивідуальними контрактами. Усе це стало можливим завдяки великій кількості силосів і підлогових складів.
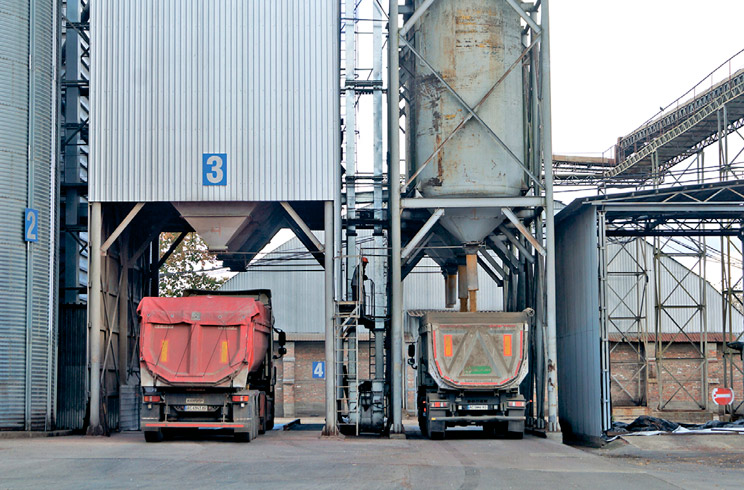
Автотранспорт на в’їзді зважують, автоматичним пробовідбірником відбирають зразки, і пневмотранспортом відправляють у лабораторію. Визначення якісних показників продукції виконують на найсучаснішому обладнанні, тож це триває мінімум часу.
Три лінії здатні приймати загалом до 6 тис. тонн на добу. Однак у складних умовах цей показних помітно знижується через відносно невелику продуктивність транспортного обладнання. Воно має продуктивність 100 т/год, і цього було достатньо, коли обсяги приймання були значно меншими. Однак із кожним роком навантаження на елеватор збільшується, і коли привозять вологу кукурудзу, транспортери фізично не видають навіть 0 т/год. Ураховуючи, що більшість транспортного обладнання має значне напрацювання, його вирішили не оновлювати, а замінити на продуктивніше (200 т/год). Це покращить умови збирання — комбайни не молотитимуть цілодобово, а тільки у сприятливі періоди доби.
Оптимальне очищення
Зерно очищають на трьох барабанних сепараторах OLIS ЛУЧ-200 і скальператорі СКО. Роботою сепараторів ЛУЧ тут повністю задоволені. Вони мають хорошу продуктивність і виконують як попереднє очищення зерна, так і готують партії до відвантаження в порти. З ними навіть насіння вдається робити, якщо підібрати правильно решета і не намагатись працювати швидко. З вологим і сильно засміченим зерном сепаратори також працюють без зауважень. За словами завідувача елеваторного господарства Петра Войтовича головне — підібрати решета і встановити відповідну продуктивність. Плоскорешітні машини навряд чи змогли забезпечити високу продуктивність у складних умовах.
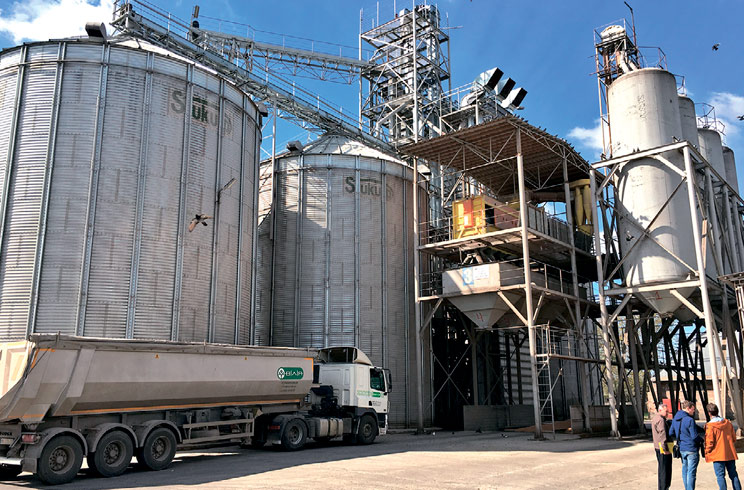
Скальператор СКО використовують менше, бо він виконує тільки попереднє очищення. Дві секції решіт забирають велике сміття, а повітряний сепаратор відбирає легку домішку, чого достатньо для підготовки зерна до сушіння.
Просто й економно
Обсяги сушіння зазвичай великі, але цього року роботи для сушарок значно менше: кукурудза надходить із вологістю від 18 до 23%, тож немає потреби вмикати всі потужності. Наприклад, торік вологість кукурудзи сягала 30% і більше, тому ситуація була зовсім іншого.
Ураховуючи особливості регіону елеватор у Луцьку оснащено трьома сушарками — двома шахтними Strahl 9000 і однією тримодульною Sukup. Залежно від вхідної вологості зерна загальна продуктивність сушіння елеватора сягає 2000–2500 т/добу. Витрати газу в шахтних сушарках — 1,2–1,3 м³, у модульній трохи більші — від 1,2–1,4 м³. Модульна сушарка більш чутлива до погодних умов, тому вітер і низька зовнішня температура сприяють більшим втратам енергії. Однак слід зазначити, що саме модульна сушарка Sukup забезпечує більш рівномірне сушіння внаслідок переходу зерна із зовнішньої зони до внутрішньої й навпаки.
Сушарки Strahl простіші в обслуговуванні. Під час сушіння кукурудзи тільки раз на тиждень повністю звільняють сушарку й очищають, щоб ніде не було залягань. Крім того, італійські сушарки споживають відносно небагато електроенергії — максимальна потужність — 120 кВт. Із сушаркою Sukup клопоту більше: у її верхній частині постійно налипають рештки — саме там відбувається вихід великої кількості вологи. Доводиться щодня чистити цю зону, щоб не знижувалась продуктивність і не збільшувались втрати енергії.
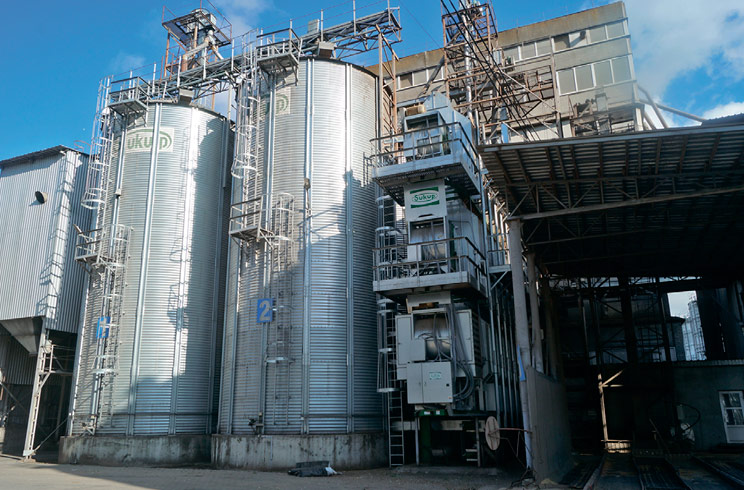
Коли кілька років тому ціна природного газу сильно підвищилась, як альтернативне джерело енергії вирішили використовувати пропан-бутан. Для цього змонтували повний комплекс обладнання, яке за потреби можна буде залучити в будь-який час. Варіанти з твердопаливними теплогенераторами підприємство поки що вивчає. Цей напрям значно складніший у реалізації, бо потребує окремої інфраструктури для зберігання і логістики твердого палива, а також місця для теплогенераторів. Оскільки сушарки досить потужні, потреба у твердому паливі буде неабиякою. За попередніми підрахунками доведеться щоденно завозити по дві фури пелет для кожної сушарки. Ще одним спірним питанням є якісні показники зерна — практично все зерно експортують, тому до вмісту продуктів горіння увага особлива.
Для забезпечення безперебійної роботи під час вимкнення електрики на підприємстві встановили 400-кіловатний генератор. Залежно від транспортного обладнання з цим генератором можуть працювати дві або й навіть три сушарки.
У силосах і ангарах
Тимчасове зберігання зерна здійснюється у металевих плоскодонних хоперах Sukup по 300 т, 500 і 1000 т. Плоскодонну конструкцію обрали через можливість зберігати значний обсяг за відносно невеликої висоти. Це давало змогу не розбудовувати елеватор у висоту і заощаджувати кошти. У перші роки все працювало добре, але з часом, коли обсяги перевалювання збільшились, зачистка хоперів створювала дедалі більше клопоту. Тому було вирішено реконструювати хопери і зробити їх конусними.
Для тривалого зберігання підлогові склади використовують паралельно з металевими силосами. Якщо зерно не потребує доробки, його відразу вивантажують у підлоговий склад. Довантаження «до повного» відбувається через завальні ями й транспортери верхніх галерей. Також використовують американські пересувні похилі транспортери.
Металеві силоси Sukup уміщують по 3000 т, 4500 і 6000 т. Окрім аерації, вентиляції й термометрії силоси оснащено системою прямого вивантаження. Це дає змогу заощаджувати електроенергію й ресурс транспортного обладнання, а також суттєво зменшує пошкодження зерна.
Алгоритм захисту
Для забезпечення біологічного захисту зерна застосовують небулізацію. Компанія SOJAM постачає препарати Пірігрен (для пшениці, жита, ячменю, вівса) і Гранпротек (для кукурудзи). Їх застосовують тільки тоді, коли зерно закладають на тривале зберігання, а також обробляють партії, отримані від сторонніх постачальників із зараженням. Фермери не завжди дотримуються умов безпечного зберігання, і в очікуванні кращої ціни тривалий час тримають неочищене й неохолоджене зерно в ангарах. Коли ж вони вирішують продавати, зерно вже заражене. Аби не допустити проблем під час експорту, таке зерно обов’язково обробляють інсектицидами, і за тиждень воно стає придатним до відвантаження.
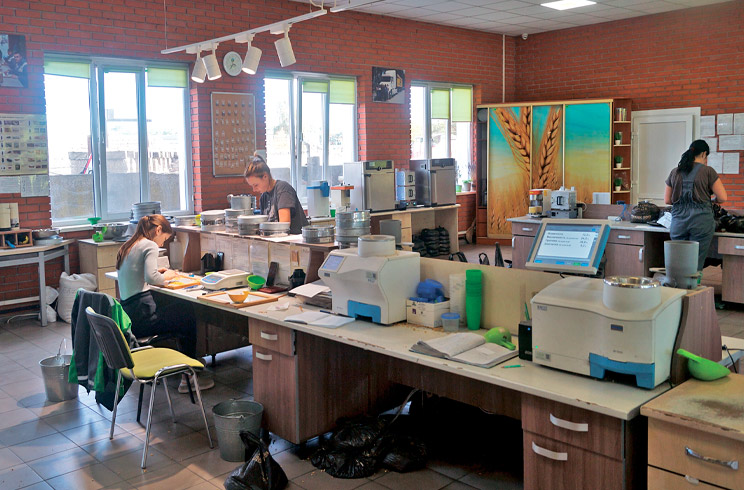
Готові до різних напрямків
У точках відвантаження накопичувальні місткості зробили із залізничних цистерн — кожна з них вміщує по 50 т. Це дало змогу заощадити кошти на обладнанні без втрат продуктивності й функціональності. Зерно відвантажують в основному залізницею, однак коли блокували порти, доводилось залучати автотранспорт.
Залізничний маршрут зазвичай вантажать дві доби, але за потреби можуть пришвидшитись і зробити це за 36 год. Торік більшість зерна експортували у Європу, для цього навіть збудували термінал у Лукові, де зерно перевантажують на вузьку колію у будь-які вагони. Після відкриття портів напрямок змінився у бік Одеси. З Луцька маршрут до Одеси рухається 2–3 доби, що дає змогу оперативно виконувати зобов’язання за експортними контрактами.
ГОВОРИТЬ ЕКСПЕРТ
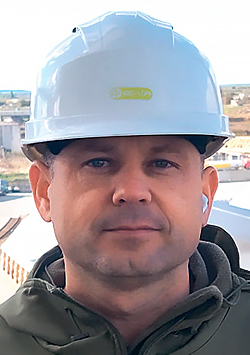
Петро Войтович, завідувач елеваторного господарства ТзОВ «Волинь-Зерно-Продукт»
— Із самого початку елеваторний підрозділ компанії розвивався поступово. Ніхто не будував одразу великі елеватори, оскільки на це не було грошей, та й потреби у великих потужностях не було. Навпаки, шукали способи заощадити кошти й скоротити час повернення інвестицій. Якомога більше робіт під час будівництва намагались виконувати власними силами. Так ми завантажували працівників і зменшували собівартість елеватора. Зі збільшенням обсягів вирощування добудовували потужності елеватора — це відбувалось синхронно. Таким чином, ефективність інвестицій завжди була високою. Навіть нині підхід до наших підприємств зберігання є вкрай прагматичним: елеватори повинні виконувати свою роботу з мінімальною собівартістю.
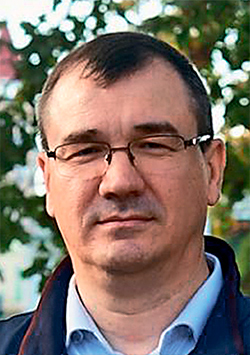
Володимир Чеглатонєв, комерційний директор компанії OLIS
— З компанією «Волинь-Зерно-Продукт» ми співпрацюємо з 2013 року, і за цей час поставили майже два десятки наших сепараторів. В основному це барабанні сепаратори ЛУЧ200, а також скальператори СКО й очисні машини Горизонт-400. Оцінку роботи нашого обладнання щоразу дає наш клієнт, коли купує нові сепаратори для своїх підприємств. Це означає, що техніка повністю відповідає очікуванням замовника за якістю роботи, витривалістю й вартістю експлуатації. Хочу наголосити, що з компанією «Волинь-ЗерноПродукт» нам дуже приємно і комфортно працювати, бо там працюють досвідчені фахівці. Вирішувати з ними будь-яке технічне питання приносить задоволення, оскільки ми розуміємо один одного з пів слова. Також ми є постачальником значної кількості лабораторного обладнання, і за цим напрямом співпраця з «Волинь-Зерно-Продукт» також є успішною та взаємовигідною.
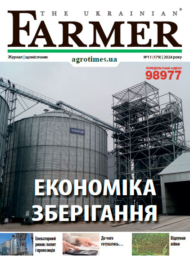