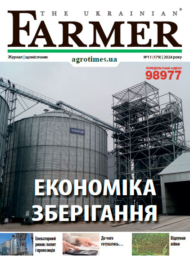
Елеватор у сучасних умовах має тільки один шлях розвитку — поступовий, оскільки повернення інвестицій значною мірою залежить від реалій сьогодення
Покрокове зростання
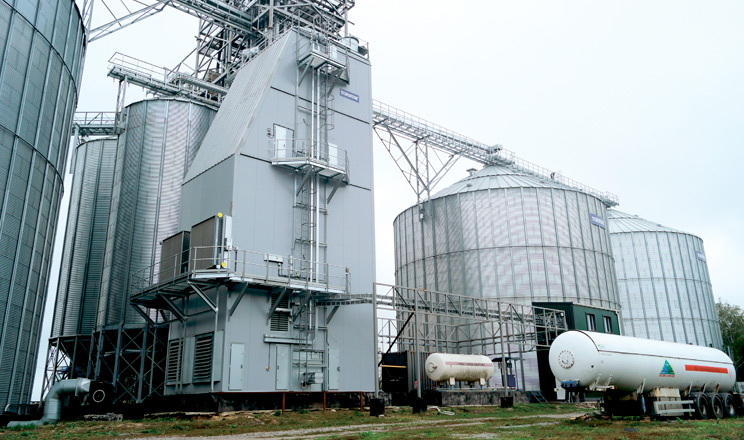
Елеватор у сучасних умовах має тільки один шлях розвитку — поступовий, оскільки повернення інвестицій значною мірою залежить від реалій сьогодення.
Коли планується будівництво елеватора для середнього агропідприємства, підхід до інвестицій має бути ще ретельнішим, ніж коли йдеться про зернові хаби. Доводиться шукати баланс між продуктивністю й реальними обсягами перевалювання, які передбачаються в перші роки експлуатації. Створюючи запас потужності «на майбутнє», власник добровільно збільшує обсяг вкладень, які повернуться не так швидко, як би йому хотілось. З іншого боку, якщо є впевненість у стабільному розвитку підприємства і збільшення обсягів перевалювання, «зайва» продуктивність швидко перетворюється на корисну й починає приносити прибуток. Треба тільки визначитись із головним питанням — де знайти достатньо грошей, щоб побудувати елеватор бажаних розмірів і не заморожувати кошти на тривалий період?
Непросте будівництво
Для таких обставин поетапне будівництво є одним із найвигідніших рішень. Прикладом такого будівництва є підприємство ТОВ «Елеватор “Родина”» з Вінниччини, де щороку збільшуються потужності й не зупиняється основна робота.
Власник підприємства Сергій Гоцуляк запланував створення елеватора напередодні повномасштабного вторгнення, підготував проєкт, а підрядник навіть розпочав земельні роботи. Початок війни зупинив будівництво на кілька місяців, але далі роботи вели й далі. Спочатку замовили обладнання транспортери, норії, силоси, але через воєнні дії завод зупинився. Встигли виробник обладнання поставив тільки один силос і частину транспортного обладнання. Замовнику довелось шукати іншого постачальника. Оскільки сушарку купували в компанії TORNUM, вирішили звернутись до шведського виробника з проханням поставити силоси власного виробництва і транспортери SKANDIA Elevator. Незважаючи на війну і труднощі з логістикою, обладнання доставили в найкоротші строки, і будівництво пішло далі без затримань.
Упродовж будівництва все складалося не так просто, як здавалось на перший погляд. Ще за радянських часів на обраній ділянці працював цукровий завод, і на місці, де планували звести елеваторні споруди, був яр. Його засипали, він заріс бур’яном і кущами, тож візуально ділянка мала вигляд придатної для будівництва. Розташування поруч із залізницею було додатковим плюсом, тому до придбання не вивчили повністю історію цього місця. Коли ділянку придбали й зробили «геологію», зрозуміли, що на місці яру ґрунт не може витримувати значних навантажень. Довелось забивати 14-метрові палі, що відчутно збільшило вартість загальних будівельних робіт. Як зазначив власник підприємства Сергій Гоцуляк, спочатку потрібно було вивчити історію цієї ділянки, поспілкуватись із людьми, з’ясувати всі особливості. Це дало б повнішу уяву, з чим доведеться стикнутись під час будівництва елеватора.
Після першої черги
Фактичне введення в експлуатацію елеватора відбувся ще 2022 року — тоді прийняли перше зерно. Проте будівництво не зупинялось. Добудовували силоси, транспортери й норії. Одразу побачили й різницю у якості обладнання різних виробників: виготовлення елементів силосів і їх оснащення було на голову вищим у шведського виробника. Робота транспортерів також кардинально відрізнялась — обладнання SKANDIA Elevator працювало тихо й не вібрувало, тоді як обладнання від іншого виробника створювало неабияку кількість шуму й вимагало постійної уваги технічного персоналу.
Елеватор із самого початку розраховували під власні потреби, тому понад 90% зерна приймається з власних полів. Хоча в майбутньому власник припускає більше залучати продукції від навколишніх фермерів. Нині основними культурами є пшениця, соняшник і кукурудза. Ріпак хоч і вирощують, проте на елеватор не возять — використовують підлогові склади в інших локаціях. Річне перевалювання сягає 30 тис. тонн, а обсяг одночасного зберігання становитиме 33 тис. тонн після завершення монтажу нового силоса від TORNUM на 6 тис. тонн.
Приймання й доробка
За робочий день підприємство приймає близько 1000 т зерна, але за умови цілодобової роботи зможе приймати до 3000 т. Нині працює одна завальна яма, другу добудовують. Транспортні системи для кожної лінії приймання проведено окремі, щоб можна було одночасно працювати з двома культурами або однією культурою з різними показниками. Для тимчасового зберігання заплановано зведення чотирьох хоперів по 500 т, з яких два вже працюють. Інші планують монтувати пізніше.
Транспортне обладнання складається з ланцюгових транспортерів і має продуктивність 150 т/год. Очищають зернопродукцію на плоскорешітних сепараторах Хорольського заводу (БСХ-200). Норії в основному працюють від шведського виробника.
Підхід до сушіння
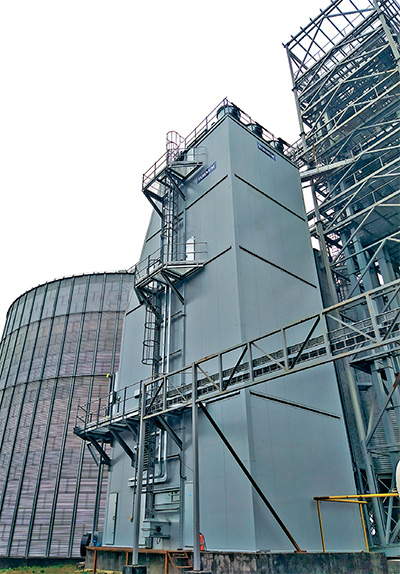
Коли обирали сушарку, дивились на досвід сусідів. Їздили на елеватори різних форматів і переконались, що саме шведський виробник створює найзручніше та найефективніше обладнання. Тому вирішили придбати сушарку TORNUM REX — мабуть, найбільш автоматизовану і захищену серед усіх, що є на ринку. Залежно від вхідної вологості сушарка може просушити 700–1000 т/добу. Як паливо використовують скраплений газ, оскільки вартість підведення окремої магістралі є надто дорогою. Попередні підрахунки показали, що потрібно близько 20 млн гривень тільки для того, щоб користуватись газом. Вирішили, що таке «задоволення» є надто дорогим, і поки що зупинились на пропан-бутані з перспективою перейти на тверде паливо.
Витрати скрапленого газу на зняття тонно-відсотка становлять 1,5 л — це виходить 50–55 грн. Якщо перейти на альтернативне паливо, можна зменшити собівартість сушіння, але поки що підприємство сконцентровано на інших завданнях. Будівництво відбувається поетапно, і на сьогодні завершується будівництво ще одного силоса. Наступного року ретельніше розглядатимуть питання встановлення твердопаливного теплогенератора.
Сушарка працює досить тихо й практично не викидає сміття. Коли ми приїхали на елеватор, саме сушили кукурудзу, тож вдалося подивитись на роботу сушарки зверху, з робочої вежі. Після скидання, коли відкривали жалюзі, кілька секунд у вихідному повітрі спостерігалась мінімальна кількість пилу і рослинних часточок, а далі повітря було повністю чистим. Та й територія навколо сушарки взагалі не була засміченою. Сушильний майстер розповів, що на цьому етапі сушіння відбувається в ручному режимі, оскільки вхідна вологість зерна досить часто змінюється, і більшої економії палива вдається досягати саме завдяки особистій майстерності. Хоча сушарка здатна працювати в автоматичному режимі й навіть адаптуватись до особливостей роботи з кожною культурою — це буде наступним етапом професійного зростання місцевих спеціалістів.
Відвантаження з перспективою
На цьому етапі зеро відвантажують тільки в автомобільний транспорт, який їде в порти. Відстань становить 430–450 км, тому логістика є доволі оперативною. Однак планується будівництво точки залізничного відвантаження, що дасть змогу відвантажувати значно більші партії за коротший час. Залізнична колія — поруч, проєкт уже прораховано й очікує готовності власника до початку робіт.
Цей рік кукурудза випередила всі культури за маржинальністю, тоді як минулого року на ній практично нічого не заробляли. Соняшник навіть за високої вартості приносить менше доходу.
Коментар
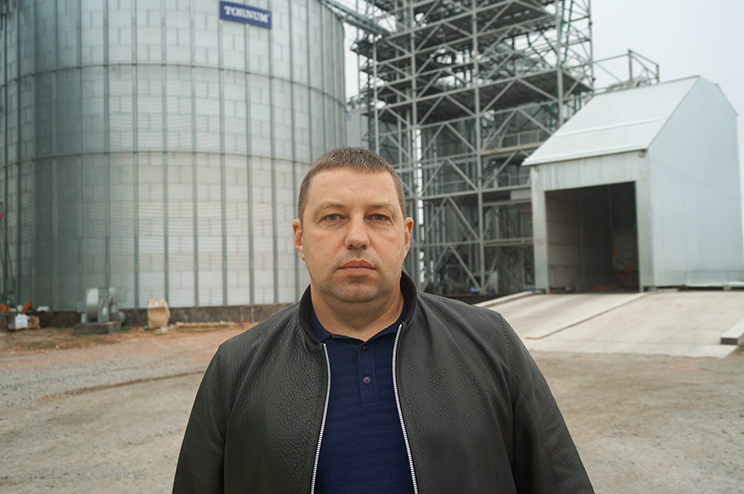
Сергій Гоцуляк, директор ТОВ «Елеватор “Родина”»
Наше підприємство має в обробітку близько 5000 га, протягом останніх 5–6 років ми стабільно вирощуємо приблизно однакову кількість ріпаку, пшениці, соняшнику і кукурудзи. Після введення в експлуатацію нового силоса обсяг одночасного зберігання стане для нас достатнім. Тому наступними кроками стануть підведення залізничної гілки, встановлення твердопаливного теплогенератора й розширення земельного банку задля повного завантаження потужностей елеватора. Це дасть змогу підвищити ефективність роботи, збільшити оберти й пришвидшити окупність інвестицій.
Нині змушені сушити зерно скрапленим газом. Це хоч і дорожче, ніж пелетами, але цього року ми не відчуваємо фінансового навантаження — кукурудза з поля надходить практично сухою. У Вінницькому районі збирали взагалі «у базі», на заході й півночі області вологість не перевищувала 18–20%.
Про оснащення елеватора хочу сказати таке: я радий, що обставини змусили обрати шведського виробника. Ми заплатили більше, але воно того варте. Спокійна експлуатація дає змогу зосередитись на стратегічних завданнях, а не розв’язувати технічні проблеми. Вже нині, після кількох сезонів роботи, я побачив різницю, і добре, що більшість нашого обладнання — від TORNUM і SKANDIA Elevator.
Володимир Василенко
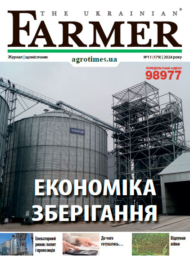